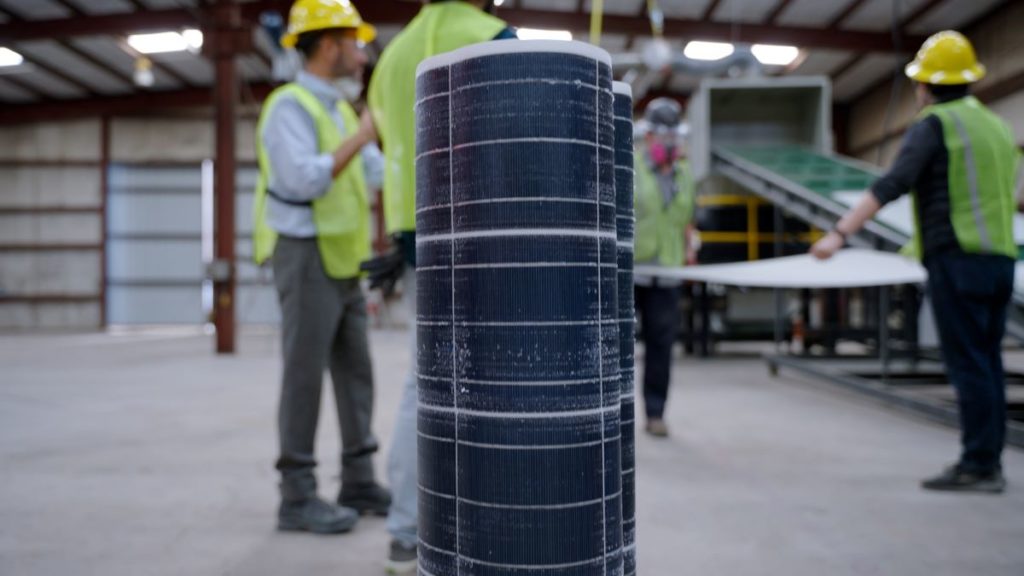
As solar power projects mature, panels increasingly lose efficiency. What do operators do with solar panels once they have reached the end of their lifespan? Will Norman finds out.
Unlock unlimited access for 12 whole months of distinctive global analysis
Photovoltaics International is now included.
- Regular insight and analysis of the industry’s biggest developments
- In-depth interviews with the industry’s leading figures
- Unlimited digital access to the PV Tech Power journal catalogue
- Unlimited digital access to the Photovoltaics International journal catalogue
- Access to more than 1,000 technical papers
- Discounts on Solar Media’s portfolio of events, in-person and virtual
In 2022, recyclable materials from end-of-life (EOL) solar panels were worth around US$170 million globally; by 2030, according to research from Rystad Energy, global recyclable PV materials will be worth in excess of US$2.7 billion, a fifteenfold increase. By the time the global net zero alarm clock goes off in 2050, the value of these materials is forecast to be over US$80 billion.
As the PV industry reckons with its social and environmental impact and the byproducts of its processes, beyond the near-term questions over provenance, manufacturing ethics and the supply chain, concerns about modules’ end-of-life are coming more and more into focus.
The average lifespan of a solar panel is around 25 years; the fleets of modules that were installed in the 2000s are close to reaching the end of their lives, and whether through repowering, decommissioning or manufacturing loss, each year will bring a more-or-less exponential increase in retiring panels.
Long-term thinking is embedded in the PR of PV companies, working as they are to ensure a more sustainable future for a habitable Earth based on clean energy from the planet’s life-giving star. To be genuinely sustainable, the industry needs to make sure that it doesn’t create a new problem in solving an existing one.
As of last year, the world has over 1TW of PV capacity installed via billions of panels. This threshold took decades to reach, and SolarPower Europe predicts that the second TW of PV energy will be on the ground by 2025, with the third possibly following more quickly still. That 1TW will need to expand between 15 and 60 times over to meet 2050’s net zero targets.
With the huge – and important – growth that solar is seeing, and recent policies like the Inflation Reduction Act (IRA) and Green Deal Industrial Plan which have pushed hard on solar deployments, what is going to become of the sheer volume of stuff going out there?
What’s lacking?
Government PV EOL and recycling programmes around the world are dragging their feet.
In Australia, the Queensland state government has announced plans to ban the disposal of PV modules in landfill within the next decade, pending sufficient public and industry proposals. It also committed AU$250,000 (US$168,000) to a pilot Solar Stewardship Scheme which will identify locations and participants to recover materials from decommissioned modules and then establish collection, recovery and recycling processes. This is, however, all a decade away and still at the public RFP stage. A lot of modules can go out of commission, break or be repowered by then.
At the time of writing, the US has no concrete EOL legislation in place and the National Renewable Energy Laboratory (NREL) has said that current recycling rates are around only 10%. Impetus isn’t present to make recycling a financially viable process, as landfill proposes a cheaper and simpler option.
The US Department of Energy released over US$8 million in investments for research and development (R&D) projects into recycling and EOL in April 2023, the first meaningful (if only just) investment into EOL that the US has made. The projects that received funding covered both material recovery and manufacturing research designed to make panels – and their recycling processes – cheaper. Scaling those processes is still yet to be acted on.
Europe is the only place where solar EOL policies really exist, included in the Waste Electrical and Electronic Equipment (WEEE) programme which came into law in 2003 and includes solar materials in its remit. It’s enacted by PV Cycle, a member-based recycling organisation accredited to comply with the scheme.
Europe also has its own fledgling Solar Stewardship Initiative, a member-based collective of companies designed to focus on the responsibility that the PV industry holds for the entirety of its operations.
And whilst WEEE may be a good baseline, the CEO and founder of US-based solar recycling company Solarcycle, Suvi Sharma, told PV Tech Power that the process in Europe calls only for recycling by 85% weight: “If you take the aluminium frame off and some of the cables off and get the copper out of there, and you just grind and crush the rest into some kind of asphalt mixture, you have complied with EU regulation.”
The value of a solar panel isn’t necessarily tied to where the bulk of the weight comes from.
The true bulk of recyclable PV material hasn’t yet crested the horizon, and most likely won’t for a few years, but the backlog is racking up at every new solar farm that breaks ground. For government policy, looking at the manufacturing, deployment and investment expansions that the US has seen following the IRA might provide an early-stage example of the fact that legislation can be effective in pushing the industry forward.
Working from within – a recycling ecosystem?
Solarcycle, Sharma’s company, specialises in PV recycling with a view to establishing a circular solar economy in the US and, ultimately, worldwide. The company recently received US$30 million in Series A funding to expand its capacity and capabilities at its Texas facility, and a further US$1.5 million of R&D money in the DOE’s recent end-of-life investments.
“It’s forecast that by the end of the decade there’ll be over 10 billion panels,” Sharma said to PV Tech Power. “Even 1% of that coming offline in a given year, that’s 100 million panels.” Scaling operations will be key to dealing with that volume, and the emergence of a circular solar economy, but in the face of an arid legislative landscape the only incentives are coming from the industry itself.
Sharma said that Solarcycle’s strategy is to work with leading US asset owners – SunRun, Silicon Ranch for example – to commit them to their long-term recycling programme through strategic partnerships.
In comments to PV Tech Power, chief product officer at US PV manufacturer First Solar, Pat Buehler, said that their in-house thin film recycling programme runs on a similar premise.
“We are fortunate to work with customers that share our values and principles, and that includes understanding that recycling is the right thing to do,” Buehler said. “We offer Recycling Service Agreements to all our customers, and we consistently see demand for our recycling services continuing to grow.”
First Solar was one of the first manufacturers to factor recycling into its operations as far back as 2005, and it has since shipped over 50GW worth of modules, Buehler said. These partnerships and established trends are important for fostering a recycling ‘culture’ and norm in the industry, particularly regarding pipeline or future projects which can have recycling plans and agreements baked into them from conception.
Fundamentally, manufacturing companies that are willing to spend more to back up their ESG credentials are really important, but the issues of scale and incentive still stands to be reckoned with.
In terms of major manufacturers, both Qcells and JinkoSolar stake claims to recycling their own modules. Neither responded to inquiries to elaborate on how they do it or plans for the future, but have publicly announced recycling processes that focus on recovering bulk material from their panels. Jinko claims that 92% of the materials in their panels can now be recycled via thermal and mechanical separation processes to access the different layers of module and cell and extract the different components.
Qcells said that they comply with regulations in every region where they operate and deploy modules, though as we’ve seen that can be a low bar in some cases; NREL’s study says that around 90% of US modules aren’t recycled.
As the US’ primary module producer, First Solar is a somewhat different story. In comments to PV Tech Power, Buehler said that “While most PV recycling processes today focus only on bulk recycling or recovering high-mass fraction materials such as the glass and frames, our high-value recycling process goes further by providing closed-loop semiconductor recovery for use in new modules.”
First Solar is a significant US manufacturer with well-established roots and a host of long-term supply deals, but its in-house recycling processes only deal with its own modules and its own segment of the PV market. The majority of US modules come from other producers who – significantly – use other technology: First Solar’s Cadmium Telluride cells and modules use different processes and materials that will need to be recovered and recycled separately.
Suvi Sharma said that manufacturers who recycle their own panels are “focusing mainly on their own manufacturing yield loss. It’s not this broad recycling infrastructure that has been set up.”
These manufacturers are doing a good thing, of course, but Sharma said that the difference between them and a dedicated recycling company is “Focus, and core competency. The reason I formed Solarcycle was I believed that the industry needed a dedicated, specialised, comprehensive recycling company to take all of these volumes, develop the technology, the equipment, the processes and raise capital to do it.”
He likened the situation to mobile phones: “You don’t have Apple recycling their own cell phones, you have companies that really specialise in that. I see the same thing happening in the solar industry.”
Following the money
As mentioned above, the key to being able to responsibly deal with the deluge of modules coming down the pipe is scale. Legislation and incentives are one solution to force, or coax, scale, but it’s almost always slow. Sharma said that he believes that recycling will be able to scale alongside deployments, partly by becoming cost-effective to developers and manufacturers.
“The competition is always landfill. What we’re trying to do in terms of our technology and equipment is to make it so that the cost to recycle with us is a minimal difference [compared with landfill],” he said. “It’s not there today, today there’s a premium to recycle with us, but we’re working to drive down the cost curve and drive up the value curve on the materials we’re getting.”
He continued: “We decided at Solarcycle to focus on very advanced recycling. It’s not really ‘go for the gold’, it’s ‘go for the silver’ because that’s what’s [valuable] in the panels.”
Mining the silver from the panels, along with the polysilicon, glass, metal framing, creates a genuinely high value process that can save customers money in the long-term, as the company has goals of feeding recovered materials back into the solar supply chain.
The near-term
Not all recycling and EOL is a decade down the line. Suvi Sharma spoke about repowering – the practice of replacing old, out of date or broken modules with new ones:
“For example, [an asset owner] could run their plant for another 10 years, but they’d be better off repowering with newer panels that are much more efficient. We’re already seeing that on the residential/commercial [markets] in a pretty meaningful way, and we’re going to start seeing it on utility-scale next year and in a few years it’s really going to accelerate.”
Module tech and cell efficiencies are constantly improving and the accelerating shift towards n-type and TOPCon/HJT modules is only going to make high efficiencies more available to asset owners with older, less efficient systems. Those old panels have to go somewhere.
“It’s actually happening in Europe quite a bit,” Sharma continued, “in Italy, Germany and some of the early markets that developed in Europe there’s going to be gigawatts being repowered in the next few years. And that’s simply for better land use, bringing the power plant up to a higher nameplate capacity on a given piece of land to maximise the kilowatt hours per hectare.”
Asset owners and manufacturers aren’t going to refuse the energy production and sales boosts that repowering can bring because they’re waiting for a responsible place to put the old panels, and extreme weather damage, age and the increasing production of high-efficiency modules are going to make repowering an attractive prospect very soon.
Not only does this allow companies to ensure the traceability and ethical sourcing of their raw materials, it can also reduce the cost of having to buy or mine new resources at a premium and increase the return on every recycled module. Silver itself is going to become another long-term concern for the industry.
A well-known December 2022 paper from the University of New South Wales forecast that, if PV deployment rates stay on track until 2050, between 85-98% of the world’s silver reserves will be used up by the PV industry. Even by 2027, we will see PV manufacturing use up 20% of the currently available silver above and below the ground.
The Georgia Institute of Technology received funding in the DOE’s recent round of investment to look into replacing the silver contacts in solar cells with copper- and aluminium-based pastes that can be applied more cheaply and to most silicon-based technologies. Reduced costs could incentivise recycling by bringing the premium down for the process.
Other silver-replacement research is ongoing at various institutions, and some modules that don’t use silver are already on the market for rooftop and C&I markets, but the overwhelming majority of projects that are deployed, in construction, in pipelines or awaiting approval are going to be silver-based PERC for the coming years.
The research to replace silver with other, more abundant and cheaper materials will surely take hold eventually, but in the meantime the usage is going to continue growing at ever-increasing rates. The parallel with PV recycling is clear enough: the work that companies are doing will take hold, but until that point the size of the problem only gets bigger.
The logic runs: if you achieve enough financial or industry incentive for companies to recycle – either by high-value material recovery or the example set by significant players in an ecosystem – you don’t need to rely on government legislation. But the challenge will be reaching that point without some impetus from outside the industry.
Pat Buehler of First Solar said that they expect landfill costs to increase in the coming years, which will in turn make recycling more affordable and attractive alongside advances in the process to drive its cost down.
Sharma summed up the state of the issue: “The waste problem is just starting. If you look at the grand scheme of things from an E-waste standpoint, solar panels are a very small percentage of that, but it’s going to see exponential growth.”
“That’s what we’re working to address, to get out in front of and set up the technology and infrastructure. We have to get more solar on the ground. For us, recycling technology is really a way to make solar more sustainable and scalable.”