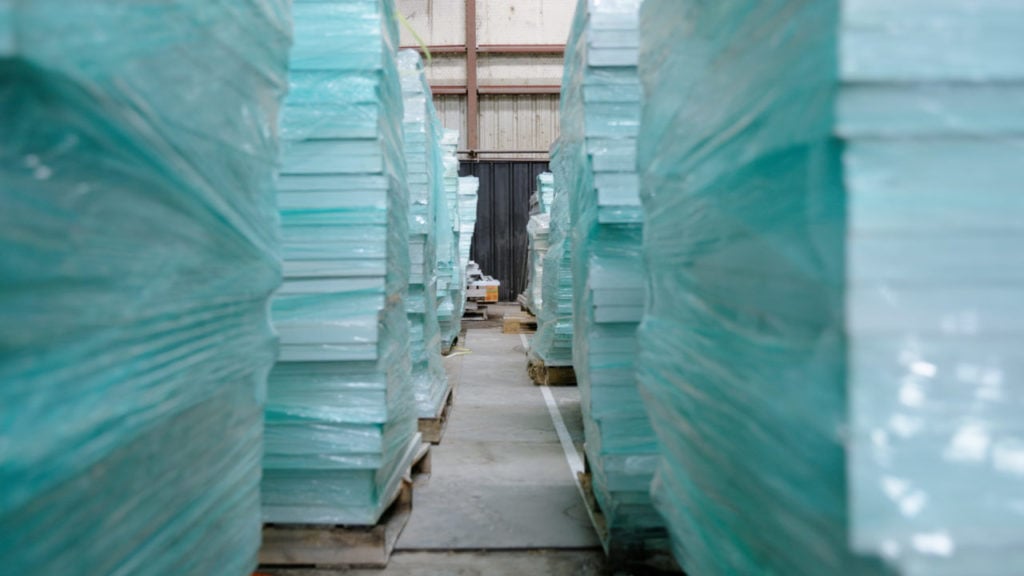
Solar energy has rapidly moved from a promising alternative energy source to dominating the transition away from traditional power sources globally, but the elephant in the room is what will happen to the millions of installed PV panels when they reach end-of-life.
As a relatively new power source, the looming problem has been invisible, but as the commentators in this article suggest, the lifetime of a PV panel is nowhere near as extensive as is generally perceived, so big waste streams will appear far quicker than anticipated. The question of reuse, recycling and waste management of solar equipment also raises big questions on how to manufacture. Should module makers aim for robust panels that last 50 years or should they aim for the highest recyclability potential but with shorter lifecycles.
Unlock unlimited access for 12 whole months of distinctive global analysis
Photovoltaics International is now included.
- Regular insight and analysis of the industry’s biggest developments
- In-depth interviews with the industry’s leading figures
- Unlimited digital access to the PV Tech Power journal catalogue
- Unlimited digital access to the Photovoltaics International journal catalogue
- Access to more than 1,000 technical papers
- Discounts on Solar Media’s portfolio of events, in-person and virtual
There is also a race against time to stop solar energy materials going down the same route as other electronic items, such as fridges, that have historically been dumped illegally by rich countries onto the shores of Africa and other poorer regions when the products reach end of life.
Fortunately, a young Texas-based company is making waves with its PV equipment recycling technology that can extract every single constituent material out of a solar panel, far more than other companies have achieved to date. The firm, Solarcycle, was co-founded by three prominent figures in the industry, who saw the impending waste bottleneck and through extensive research during the Covid-19 pandemic found that very little was being done worldwide to solve the solar recycling issue in terms of both comprehensive and scalable material recovery.
“the average lifetime is closer to 15 years, if not less, and so that means we’re going to start seeing a significant volume of end-of-life panels much faster than most people realise.”
“What we’re doing is somewhat revolutionary,” Jesse Simons, chief commercial officer at Solarcycle, who also served high level positions at US environmental organisation Sierra Club for two decades, tells PV Tech Premium. “What got me to start this company was a realisation that we just weren’t going to have enough raw minerals and materials if we continue with the extractive practices of the past. We dig it up once, use it once, throw it away.”
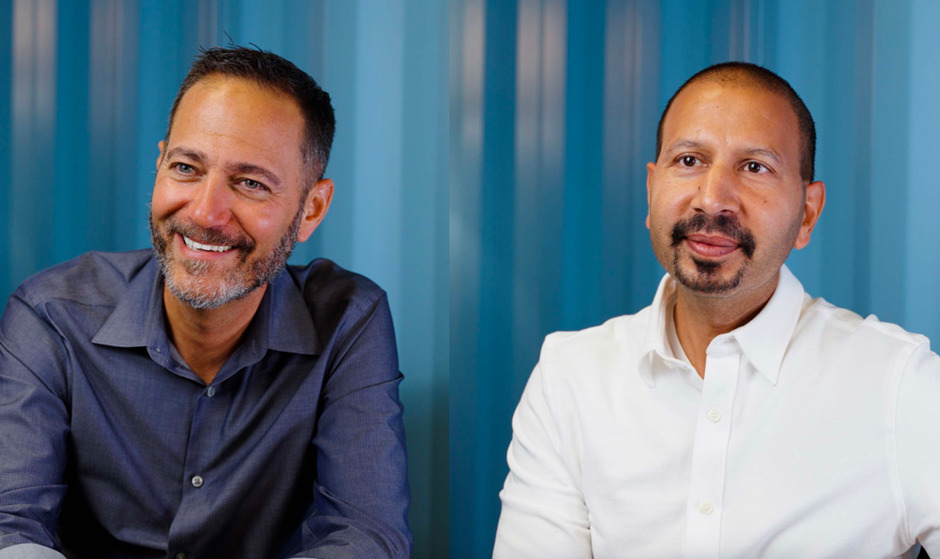
Simons began talking with Suvi Sharma, the co-founder of two huge solar companies, module manufacturer Solaria and PV tracker supplier Nextracker, and who became CEO at Solarcycle. Sharma had started a deep dive into how to make the solar industry fit into a circular economy but had come to the conclusion that while there was some interesting R&D, not enough was being done to bring it to action. Meanwhile, other big names from the likes of SunPower and SolarCity were also original investors in Solarcycle.
“The early players in solar all saw this coming, realising it’s going to be a massive wave and we need to ride it and harness it,” says Simons.
Module lifecycles are far shorter than anticipated
The conventional wisdom is that solar panels will last 25-30 years and therefore with most module installations happening in the last 10 years, the big waste problem won’t begin for another 15-20 years away, says Sharma, but his own statistical analysis has found far more disturbing timelines.
“It’s US$1 in a landfill, it’s US$50 to recycle”
“I started realising that the average lifetime of a solar panel is not 25 to 30 years; that’s a maximum lifetime. The average lifetime was actually significantly less because you’ve got everything from manufacturing, yield loss, shipping breakage, installation breakage, product warranty claims, weather damage and repowering. You aggregate all that and you start seeing the average lifetime is closer to 15 years, if not less, and so that means we’re going to start seeing a significant volume of end-of-life panels much faster than most people realise.”
Sharma then found reports that it cost US$1 to landfill a solar module versus US$50 to recycle, while in some cases landfill sites would not even take panels due to confused perceptions of their toxicity. Investigating why it was so cheap to make a panel but so expensive to take apart, Sharma realised the need for an infrastructure of recycling and remanufacturing that matched the technology and scale of the PV manufacturing industry of today.
Simons and Sharma foresaw that with solar moving from up-and-coming niche player to mainstream it was now in the spotlight for a backlash with environmental groups cottoning onto the imminent waste problem of solar, wind and batteries. Thus, they connected with Dr. Pablo Dias, a renowned researcher in PV module and e-waste recycling from the University of New South Wales in Sydney, who was doubling down on low cost but scalable technology for recycling PV. Dias then became Solarcycle’s CTO and third co-founder with the company being incorporated in January 2023.
Sharma summarises the company’s vision as a venture in how to make new solar panels from old solar panels, focusing on extracting the glass, aluminium and silver and feeding it back into the supply chain to create a circular industry. This not only makes the solar industry more sustainable but, less obviously, it also makes it more scalable, because solar module manufacturers already use up vast quantities of the annual world silver supply, taking 15-20% of the global supply at present and forecasts to take 50% in the near future. Such high-level consumption is also found in aluminium and other raw materials. Sharma believes the PV sector needs to quickly grow to ten times larger than it is today and so this recyclability is necessary in the next 5-10 years to make resources available.
The recycling technology
What sets Solarcycle apart is its ability to extract all the solar metals inside the panel. Aside from the aluminium, Simons says that the silver, silicon and copper inside the laminate accounts for less than 3% of the weight of the panel but more than 50% of the value and “nobody else is going for that”, he says.
While the European Union’s Waste electronics and Electrical Equipment (WEEE) regulations caps recycling requirements at just 80% of the weight, Simons adds that 80% of the module weight comes from just stripping off the aluminium frame and the glass, which then leaves out that 50% of value that’s tied up in just 3% of the weight inside the semiconductor.

Solarcycle’s patented process recovers at least 95% of the value of the panel and returns it, in some way, to the domestic supply chain. Material-by-material, its process recovers the following percentages:
- 99% of glass
- 95% of silver
- 80% of silicon
- 98% of copper
- 100% of aluminium
The company’s far-reaching recycling process, which is able to remove every single constituent material out of a PV module, is proprietary and the firm has filed around seven patents on it since being founded.
“We’ve developed electrochemical techniques to remove the metals out of the laminate and there’s really no one doing that today out of a solar panel, because the silver, copper and silicon are hard to extract and then you’ve got to separate them,” says Sharma. “We’re doing all of that in-house, so it’s very comprehensive.”
Solarcycle has designed unique custom equipment that dismantles and de-manufactures a module from end-to-end in a similar but reverse way to how modern factories have specialised equipment to put on frames and lay up solar cells when creating a module. A panel can be processed for recycling in one hour, but since modules arrive in big batches from customers, the firm commits to recycling all the panels within 30-45 days of being picked up.
In terms of weight, all the solar panel material is diverted away from landfill, apart from a menial amount of dust from the remanufacturing process that accounts for less than 1% of the module and this is still classified as zero waste.
Part-2 of this article will discuss how recycling solar PV will reach landfill parity, the company’s global ambition and how PV recycling will have to work towards avoiding dumping panels illegally in less developed countries.
The most recent edition of our downstream journal, PV Tech Power, features a piece on PV end-of-life and recycling.