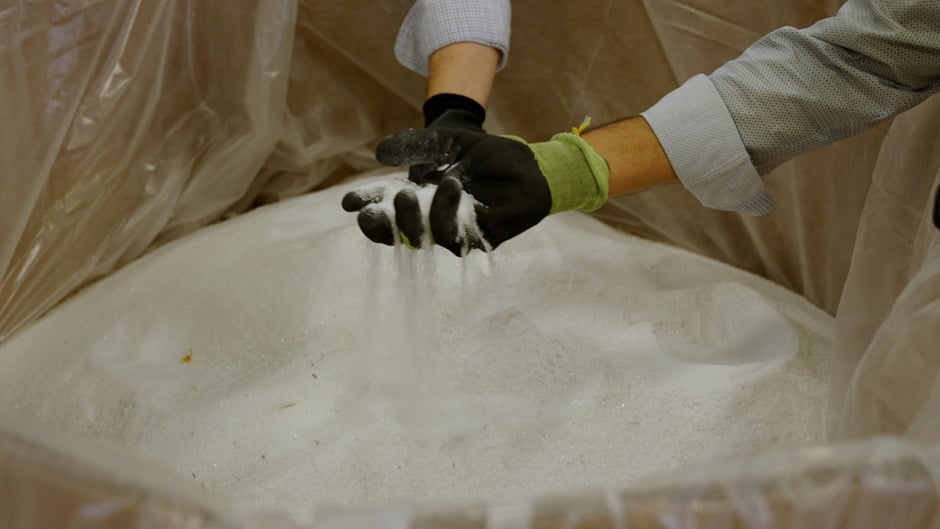
PV Tech Premium talks to Solarcycle’s co-founders about their company’s unique ability to extract every single constituent material out of an end-of-life PV module, how solar panels are not lasting as long as people expected, the race to prevent solar waste from being illegally dumped across the globe, and how modules can have a useful second life.
Part 1 of this article looked at the people behind Solarcycle and how the company is working towards reducing the cost of recycling solar modules to avoid its end-of-life cycle ending up in a landfill, while being able to recycle at least 95% of the value of the panel as it returns it to the domestic supply chain. Part 2 of this article will discuss how recycling solar PV will reach landfill parity, the company’s global ambition and how PV recycling will have to work towards avoiding dumping panels illegally in less developed countries.
Unlock unlimited access for 12 whole months of distinctive global analysis
Photovoltaics International is now included.
- Regular insight and analysis of the industry’s biggest developments
- In-depth interviews with the industry’s leading figures
- Unlimited digital access to the PV Tech Power journal catalogue
- Unlimited digital access to the Photovoltaics International journal catalogue
- Access to more than 1,000 technical papers
- Discounts on Solar Media’s portfolio of events, in-person and virtual
How close to 100% recyclability?
Plastics, which make up around 10% of the weight of the panel – mostly in the module backsheet – and the EVA film used in laminating the panel, are the only material that Solarcycle has yet to find an off-taker for. Since these are the most difficult materials to recycle and reuse. At present, the plastic has so little value that the company pays a small sum to ship it away to be turned into gravel. This process may be marginally better ecologically than having to dig up new gravel, but the company is working with a few large chemical and materials companies to try and qualify these plastics for filler material (concrete or asphalt).
“We hope to have that complete by year end and that way we can get to a zero-waste facility,” says Sharma.
Just 3-5 years ago, there wasn’t enough volume of end-of-life modules for such a thorough PV recycling venture to make economic sense, he adds, but the time is ripe for starting this work as more and more panels are starting to come offline. Spending on R&D also still makes sense since the industry is not yet “drowning” in used panels.
From grid parity to landfill parity
The holy grail for solar energy was reaching grid parity when its costs started to dip below those of conventional power sources such as coal, oil and gas. Simons says the next aim is to reach landfill parity where the cost of recycling PV is less than landfilling it, but there is a lack of market forces encouraging the innovation necessary for this. Instead of requiring “complicated bureaucratic regimes that are funnelling money to non-profits”, Simons believes landfill parity can be reached in the same way that solar competed with gas and coal, which is by innovation at scale. While Europe’s WEEE regulations have value, Simons does not see it driving asset owners to the point where recycling PV becomes a “no-brainer” because it sets a “low bar” for material recovery.
Some landfills have not even accepted solar panels in the past due to question marks over whether they are deemed hazardous waste or not. Sharma claims that solar panels are “pretty benign” though they do contain small amounts of trace lead.
There has been a lot of confusion between how the Environmental Protection Agency (EPA) and states such as California classify hazardous waste versus universal waste, says Sharma. Landfill companies would rather reject PV panels than have to perform an expensive Toxicity Characteristic Leaching Procedure (TCLP), or have the EPA come back a year later to declare the panels as hazardous waste and require them to be dug out of the ground again with a large fine slapped on top.
‘Landfills are our biggest competitor’
Nonetheless, landfills are “actually our biggest competitor right now in the US” says Simons. There are no laws preventing disposing of valuable panels.
The true competition though is around creating value-added products out of solar panels by mining them for those materials and then turning them into new products that can be sold into the PV industry. The true margins come from new solar glass, and new aluminium and silicon that goes into anodes.
“I don’t think anybody else is doing that or has that vision,” says Simons. “And by the time we really get our factory up and running and get these off-taker agreements on with the major manufacturers, I think it will be very hard for other smaller companies to compete, like these local waste companies.”
Global ambitions and WEEE regulations
While Solarcycle has both a domestic focus and global ambitions, both co-founders want to consolidate their PV recycling process across the US before major ventures abroad. The US only has 10% of the market, says Sharma, so the company will need to be recycling panels all over the world eventually.
The company has already started discussions with other companies about partnering on recycling in other regions, but most manufacturers it has spoken to so far are based in the US. It has talked with Korean company Hanwha Solutions, the parent company of Qcells, which has a major PV manufacturing facility in the US state of Georgia, about future manufacturing approaches since South Korea is currently re-evaluating an extended producer responsibility law for solar.
Solarcycle also has an eye on Europe, whose existing WEEE regulations could support its business model to some extent. There is also a drive for onshoring solar manufacturing within Europe like the US is doing and Europe is a huge solar market with many older vintage solar plants which could supply a feedstock of old panels for Solarcycle’s business.
However, while Europe is far ahead of other geographies from a waste regulation standpoint, Sharma believes it is behind in many ways because the WEEE laws encourage a “very crude recycling” that only involves taking off the frame, extracting some copper and crushing the rest of the panel to use as asphalt filler.
“They’re not getting all the crucial metals or the glass out,” he adds. “So right now in Europe, there is no high value recycling going on for solar panels.”
The company is also looking at India and South America but, Simons says: “Our first thing is let’s nail North America and make sure we’ve really got a strategy.”
The race to stop dumping on the shores of Africa
PV Tech Premium asked both co-founders whether the proliferation of PV recycling technology and infrastructure around the world would come quick enough to prevent large waste streams of panels being dumped illegally on the shores of less developed countries.
“It’s very difficult to prevent it at 100%,” says Sharma. “But I think we can prevent most of it when these volumes really pick up because we’re aiming for landfill parity where it’s just as cheap to recycle with us as it is to landfill. At that point, there’s no reason to landfill. There is also a cost of shipping to Africa so by managing everything including really low cost logistics, our goal is to keep everything onshore.”
Sharma calls the second life panel market in Africa a “wild west” where many “less than scrupulous companies” don’t test the modules properly. Nonetheless, he does expect there to be a market for second life panels in lower income countries so Solarcycle is exploring how to create not only a robust, transparent chain of control, but also how to set up proper recycling infrastructure in such regions. The company does manage reused panels itself but so far most of those panels have stayed in the US.
Peeling a banana versus de-seeding a pomegranate
Simons is very confident that the necessary capacity to recycle major volumes of end-of-life panels can be achieved to match the rate of increasing waste streams. It will require large amounts of capital, leadership and larger companies making pledges towards circularity despite initial extra costs. Some large manufacturers are already supporting it by envisioning that as the recycling technology scales, the costs will drop.
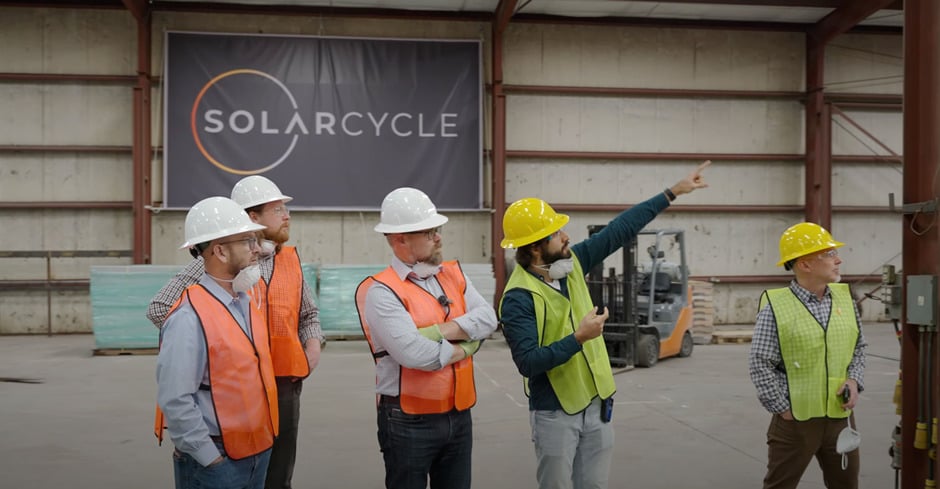
Although PV modules are complex, they are still easier to recycle than many other forms of e-waste. The US, for example, has around 10 million automobiles that reach end-of-life every year and each one has huge amounts of electronics in them, says Simons. Yet, it’s very hard to get the steel or semiconductors surrounded by steel and plastic out of these cars, or even extracting the valuable materials from a laptop, whereas a solar panel’s valuables are far more accessible nestled merely between the frame, glass and backsheet.
It is this relative simplicity that makes Simons “quite confident” in the scalable recyclability of both solar panels and energy storage batteries. He likens solar recycling to the ease of peeling a banana whereas automobile recycling is like the frustrating de-seeding of a pomegranate.
Make panels last longer or design for recyclability?
Whether PV modules will be designed for ease of recycling in the future will be a huge factor in how industry circularity progresses. Simons notes that wind energy blade manufacturers are already starting to design the next wave of blades to be much easier to take apart than the original models.
Meanwhile, using its own PV recycling experience, Solarcycle is already notifying big PV producers what design quirks make recycling harder or easier and these companies are responding to these ideas. In true circularity, it will be these manufacturers who also become the off-takers of Solarcycle’s recovered silver, glass and other recycled PV materials.
“A cell phone might last for 20 years if it’s well taken care of, but is it going to be used for that long?”
There is a tension in the industry between designing a robust panel to last for 50 years, versus designing panels that cost less and have shorter lifecycles but are also easier to recycle. Both co-founders believe it is a mistake to focus on 50-year lifecycles instead of reuse because very few semiconductor-based technologies like phones or laptops are used for the maximum amount of time they are capable, as technology progresses so rapidly.
“I don’t think that we should be looking at how to make a panel last 50 years,” adds Sharma. “We should be willing to make a panel that may last for 15 years, but it’s very sustainable and easy to recycle, because the technology just keeps marching.
“The reason why solar has won and is the king of energy now is basically because of better and better technology with efficiency improvements every year. So today, if you’re an asset owner, you can replace your 200-Watt panel with the 550 or 600-Watt bifacial panels, so maybe you can use it for another 20 years.”
Second life solar for green hydrogen
Some modules processed by Solarcycle are not yet old and only need minor repairs such as having a broken diode or junction box. The company is using some of these panels onsite behind-the-meter to power its own recycling facility in Texas rather than to power the grid.
However, some companies are already in talks to buy these second life panels for a number of uses. Several large energy companies, for instance, are looking at how to make green hydrogen using second life PV modules that have lower efficiency but are significantly cheaper than brand new. This model makes sense in geographies with plentiful land availability such as the ranches of Texas, where it is less important to have the maximum efficiency in every square metre used.
From recycled materials to value-added products
Large solar asset owners are signing up to long-term deals with Solarcycle to take the panels when they reach end of life. The company charges a per panel takeback fee that covers three things: the reverse logistics from the project site; the recycling process; and a recycling certificate combined with a transparent sustainability impact report explaining what was done with the materials. A second revenue stream comes from selling the extracted materials and putting them back into the supply chain.
Many of these asset owning clients also have large stationary storage assets which Solarcycle may eventually include in its recycling strategy.
“Eventually, we want to be more than just a materials company; we want to be a value-added products company,” says Simons. “Instead of just selling very pure glass into the recycled glass market, imagine if we built our own solar-powered electric arc furnace that melted that glass down and could make new solar glass to sell to Hanwha Q cells or Silfab, or one of these manufacturers who is onshoring. That’s the ultimate business model. And not just glass, we want to be able to do the same thing with perhaps micronizing silicon and selling that into anodes for the new wave of batteries that are replacing graphite with silicon. We want to do the same thing with aluminium frames.”
Biggest barrier to PV recycling: proliferation
The biggest barrier to this comprehensive recycling technology spreading across the globe is getting the technology to work at scale and at low cost, says Sharma. If that becomes a reality, then Solarcycle can envision setting up these facilities in places like the UK, France, Nigeria, India and other worldwide hubs.
“That’s our focus to just get the technology working really well at high scale and low cost,” says Sharma. “It’s not going to be overnight, but we can get there in a pretty short amount of time.”
The most recent edition of our downstream journal, PV Tech Power, features a piece on PV end-of-life and recycling.