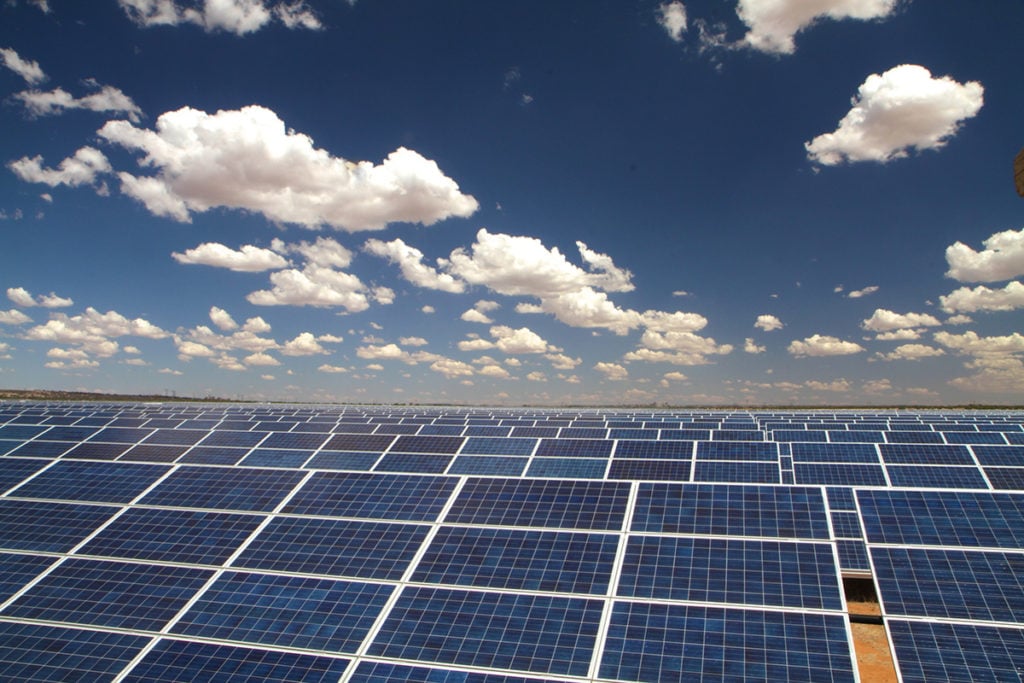
South Africa’s announced 10% import duty on solar modules poses challenges for developers, because while larger projects may absorb the additional costs, smaller projects, with tighter profit margins, could face reduced profitability, delays or even become financially unviable.
These challenges exist amid an environment of struggles with local sourcing and meeting bankability standards, according to Jose Minguillón Forteza, managing director for Africa at Spanish-headquartered solar developer Grupo Cobra.
Unlock unlimited access for 12 whole months of distinctive global analysis
Photovoltaics International is now included.
- Regular insight and analysis of the industry’s biggest developments
- In-depth interviews with the industry’s leading figures
- Unlimited digital access to the PV Tech Power journal catalogue
- Unlimited digital access to the Photovoltaics International journal catalogue
- Access to more than 1,000 technical papers
- Discounts on Solar Media’s portfolio of events, in-person and virtual
During previous rounds of South Africa’s Renewable Energy Independent Power Producer Procurement Programme (REIPPP), attempts to support localisation were met with exemption requests on the local content requirements imposed on solar modules, inverters and trackers. Local production of both inverters and trackers saw progress in recent years, but PV module manufacturing has been harder to localise due to the cost and complexity of silicon wafer manufacturing.
Indeed, there is a disparity between the speed of global technological advancements and domestic manufacturers’ ability to supply the cutting-edge equipment needed to meet competitive tariffs, Minguillón Forteza, tells PV Tech Premium.
“PV module manufacturing facilities are purpose-built for the panel technology and sizing, and with the boom of the solar industry, the technological leaps have been enormous with each year necessitating many new manufacturing facilities to be built to keep up,” says Minguillón.
“Though many tier one manufacturers are strengthening their local manufacturing facilities to satisfy local demand, these facilities cannot reasonably produce the latest capacity panels necessary to keep up with the competitive tariffs required by the market.”
The search for ‘brilliant individuals’
De Wet Taljaard, solar energy technical specialist at the South African Photovoltaic Industry Association (SAPVIA), had said that the 10% import duty adds an administrative burden to PV projects, both in complexity and cost that will be reflected in the overall project costing. Moreover, the entities responsible for the duty and the rebate mechanisms haven’t yet kept up with the requests, which has resulted in a bottleneck.
On the other hand, the global downward trend in module prices could offset the burdens, according to Taljaard.
Indeed, Minguillón Forteza describes the country’s import duty as a “meaningful way” to encourage the industry to find a solution for localising production of PV modules, adding that there are “brilliant individuals” amongst the module manufacturing community. Grupo Cobra believes that, given the rapid growth of the solar market in southern Africa, equitable solutions can be found through changes in the traditional PV module manufacturing process.
“We have seen the US move through this same process over recent years and can be afforded the lessons learned from how they’ve managed it,” adds Minguillón Forteza.
To avoid the duty’s inherent protectionism from disrupting the recent resolution of the country’s major load shedding crisis, the import duty is initially mitigated with permits for a rebate mechanism. These rebates come into play when required panels or quantities are not available in the Southern African Customs Union.
Reduced IRRs and smaller projects hit
Minguillón Forteza notes that while the permit provision is in place, the import tax will not be felt in immediate-term projects. However, once the local manufacturing industry has become strong enough for the permit to no longer be applicable, he expects to see “some reduction in the internal rate of return (IRR) for many solar developments”.
Smaller projects with slim profit margins will feel the burden most heavily, he adds. Aggregating procurement across different developments would become necessary for these smaller developments to maintain viable returns, but likewise such parallel purchasing is also less achievable for smaller local players.
Some development timelines would also have to be reconsidered, while discussions are had with module manufacturers to understand the way forward and the timeframes to increased local capacity.
Minguillón Forteza adds: “It cannot be sugar-coated that the tax issue will remove many projects’ viability. It’s rare that policy change does not incur casualties in the short term.
“So long as the import tax is met equally with rebates for local manufacturers, we are sure amicable localisation can be achieved within the solar module value chain.”
Another major hurdle, for example, is Grupo Cobra’s own requirements to use tier one modules to meet bankability standards. Noting that tier one manufacturers must undergo stringent testing and certification, Minguillón Forteza says that while most producers will aim to procure locally as much as possible, local manufacturing facilities “must ensure such standards are adhered to” in order to promote growth in the domestic market.
Last week, PV Tech Premium reported that domestic PV manufacturers were already utilising the duty announcement by talking with tier one producers—mostly from China—to collaborate on local module assembly facilities for the South African market.