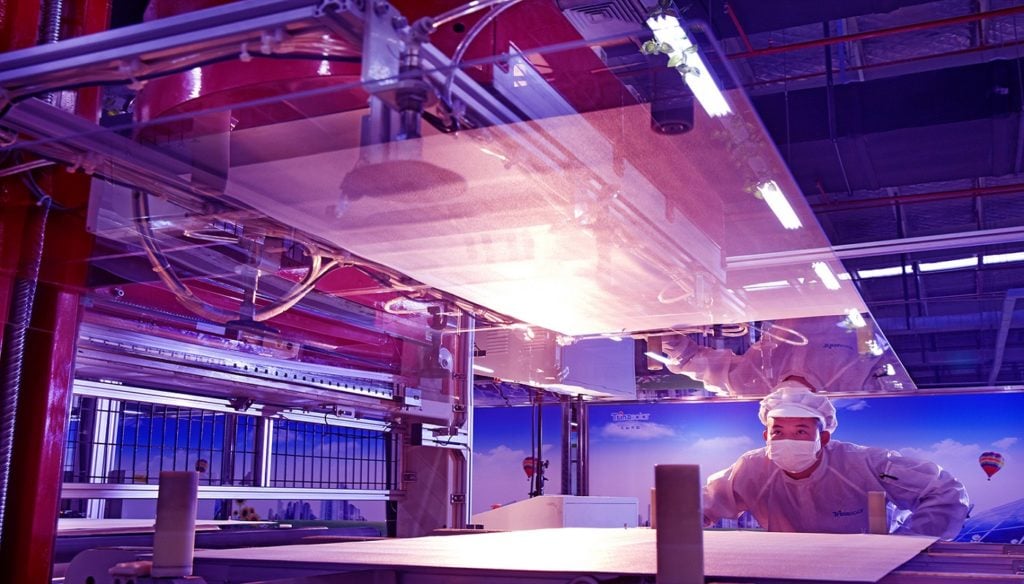
In the second part of a two-part feature on the solar industry’s response to polysilicon price increases, Carrie Xiao hears from industry leaders about the importance of technology innovation, efforts to reduce waste and the need to avoid cutting prices blindly just to appease customers.
Part one, published earlier this week, can be read here.
Unlock unlimited access for 12 whole months of distinctive global analysis
Photovoltaics International is now included.
- Regular insight and analysis of the industry’s biggest developments
- In-depth interviews with the industry’s leading figures
- Unlimited digital access to the PV Tech Power journal catalogue
- Unlimited digital access to the Photovoltaics International journal catalogue
- Access to more than 1,000 technical papers
- Discounts on Solar Media’s portfolio of events, in-person and virtual
Leave room for new production lines, do not cut down on prices blindly, pay attention to advanced technology
Gang Li, general manager, Seraphim
“I’d like to propose a few suggestions for my company and for the industry as well. The first one is to keep up with the trends. 158mm is not available now, 166mm will soon be gone. To meet the customer needs, you must follow these trends. The second is to leave room for possible changes. Future technology routes must be considered in making new investments. Seraphim plans to invest in around 10GW of modules this year, and our plan allows for unpredictable circumstances and needs.
“Finally, let’s come to cost reduction. It is important, of course, but the COVID-19 pandemic, trade frictions and the soaring raw material price have made it impossible to reduce costs substantially. But it can also be seen as an opportunity to teach the customers a good lesson. The price of modules will go up, and we’ve been cutting down the price for ten consecutive years.
“For module companies to survive, they must pay attention to profit making, and if they blindly follow customers’ needs on cheaper modules, it will be very difficult. In case the price is slashed to be even lower than the cost, the company would suffer heavy losses in processing fees, material costs and cash flows.
“Quality always takes an upper hand over price. Customer benefits are tied to quality. What matters is nothing but the length of cost recovery. Quality control is always put in the first place. There is no doubt about it.
“Next, how to reduce costs reasonably? At present, domestic transportation costs account for 5% to 8% of the module costs. A decentralised strategy is recommended for module manufacturing. The industrial chain layout shall be planned in detail to achieve the ‘3060’ target, China’s installed capacity will be greatly increased, which may exceed half of, or even reach two-thirds of the global capacity. As such, module manufacturing must be decentralised.
“The last point is not to blindly pursue large sizes, but to focus on the technology. Technology progress has been the primary force driving down costs for many years. Cell efficiency can barely increase by 0.2% or 0.4% each year as before. To improve cell efficiency, we must resort to cell technology. There will be new technologies soon. In three to five years, non-silicon materials, especially fuel cells, will turn out to be a good starting point, which can bring about significant cost reductions.”
Substantial cost reduction can be enabled by accumulated experience, innovation and large modules
Mengyu Zhao, senior director of quality department, Trina Solar
The rapid development of the photovoltaic industrial chain in recent years has contributed to equipment localisation, which has opened many doors for Trina, Zhao says. Automated production lines have facilitated significant decreases in cost and a mass upscaling in the capacities of manufacturing facilities – what was 100MW a few years ago is now almost equal to 1GW, and Zhao says this is all about the progress of the technology.
“I believe that large size modules cannot be realized without the automated equipment and the ability in equipment R&D,” Zhao says. “Large-size modules were rolled off after a series of equipment-related problems, for the equipment suitable for pulling to the machines used for producing cells and modules, were resolved.”
While cost reduction can be delivered through the development and use of new innovations, it should not be at the expense of quality. Given modules are expected to generate power for at least 25 years, all products must be continually improved to prevent anything risking overall quality. Zhao says Trina has collaborated with its supply chain partners to push products, technology and production processes, which has led to improvements in balance of system costs and levelised cost of electricity (LCOE), with the 210mm cell delivering a “real revolution” for profit margins.
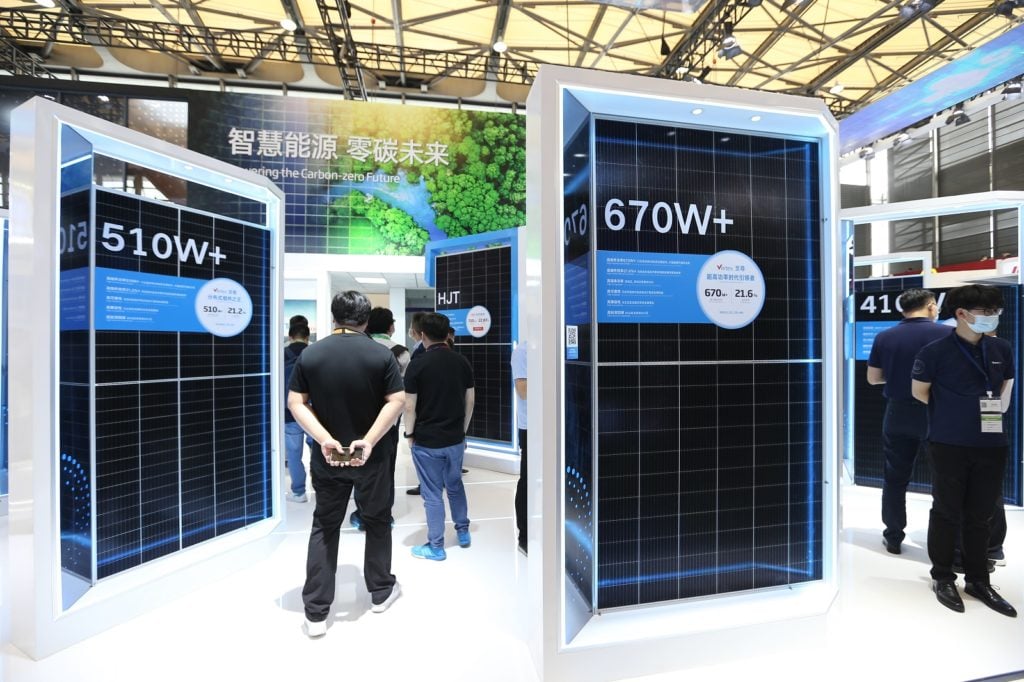
Calling on standardisation to minimize disorderly competition and reduce waste
Wei Zhang, vice president, Wuxi Suntech
Cells and auxiliary materials account for around 60% and 30% respectively in module cost structure, a smaller part of it is the processing cost, and now all solar companies are trying to figure out how to minimise all types of costs. Zhang says there is a need for a “healthy ecology” to form in the solar sector, driven not just by capital and the destination of investment, but by the technology itself.
“Each company is limited in resources. The industry is still not mature now. You can integrate vertically and pursue extremely low costs, which would often involve huge risks. Technology is always advancing, and will continue to change. No matter if it’s cell or module, each company must build up its expertise to form its own competitive advantage. This may take time, but I think that in the future, a healthy business model should be like this. One company doing everything is not conducive to a robust development,” he says.
The best companies in five or ten years’ time will be the ones that establish competitive edges in technology now, Zhang says. “Take cell efficiency as an example, if I can take it to 26%, then a barrier will be created. This is the same for materials. In this way, the company will grow strong. [But] It is not always the larger the better, if you are not capable of controlling scale, then technology change will pose great risks.”
It has been 20 years since Wuxi Suntech was established and the company has been actively preparing for future technology developments, launching 2GW of TOPCon manufacturing capacity. Suntech’s capacity will grow to 10GW by the end of this year, and Zhang said the firm has placed technology at the heart of that expansion. “To survive and thrive, a company must take the leading position in technology first. For PV power generation technology, cell is the core. Of course, innovation is very important in all aspects.”
Companies could, however, be aided by a collaborative front, with an industry association or alliance tasked with taking action to minimise what Zhang refers to as “disorderly competition” and to reduce waste in the industry. That will allow the companies to focus on what their core competencies, which is making modules.
Be wary of disorderly cost reductions, and keep in mind the objective of improved products
Yichi Zhang, TÜV Rheinland
“Quality control is also one of the most important tasks for us to assist the industry growth,” says Zhang, adding that TÜV Rheinland has witnessed an increasing number of short-term failures in module testing as a result of material innovations and increases in product sizes.
“Taking the mechanical load test as an example, it is a very simple test. It used to be 2400 Pa, now it is 5400 Pa, with possible increases in the future. Why does such a simple test show increasing results? It is very simple. You’ve mentioned cost just now. With glass and aluminum framework going thinner, cells and modules as well are getting larger, and thus the mechanical performance is reduced. This is a question that needs to be considered comprehensively.”
Design-related margins for error are gradually being eating away as module sizes increase, Zhang says. “There used to be 50mm framework. At that time, the modules were not as big as they are now. Now that the current is getting larger, more consideration should be given to the selection of materials in module design,” Zhang says, stressing that module performance is limited by material performance.
In the past, problems found in one field may be partially compensated by design margins but things are different now. Suppliers of module, spare parts and materials need to work together to identify solutions.
The quality or performance degradation arising from cost reduction is also obvious in other tests or applications. Outdoor testing and application can reflect the real module power output.
Over the past two years, the notion of ‘remaining true to our original aspiration’ has become increasingly popular with solar manufacturers. “Instead of blindly pursuing profits, the manufacturing industry should instead prioritise accumulating more experience,” Zhang says.
Companies throughout the industrial chain should cooperate to seek development and benefits in the long run
Tongxin Wang, general manager, Zhongtian Photovoltaic
“It was glass last year and it is silicon this year that have experienced a surge in price. The price rise of various materials, auxiliary materials and cellophanes is closely related to the smiling curve mentioned earlier [by Mr. Zhang]. While these are the materials for producing solar modules, we should work with all players throughout the entire industrial chain to pursue long-term growth.
“Taking glass as an example, last year some manufacturers made huge profits because of strained glass supply. Many peers were attracted into this business, including companies of other products. It may generate short-term benefits, but does pose to harm the company in the long run.
“In my view, to pursue long-term benefits, all companies within the industry need to work together. Materials are very important to module reliability and delivery, especially backsheet materials, which play a vital role in the module’s lifetime.
“In the long run, the photovoltaic industry should plan its structure from the top to balance all types of materials. Some companies should not be pushed aside because of the supply and demands situation in the market. Do not forget the pain once the wound is healed.
Long-term planning can prevent irrational pricing of some materials. Some critical materials were not being highly valued and sometimes manufacturers will cut corners to reduce costs, resulting in long-term hazards. That’s what happened to 3A back sheets.
“How to coordinate and solve the problem of cost and quality? As far as we are concerned, we have to work in this industry for another ten, twenty or even thirty years. We are looking at the long term and healthy development of this industry and the material reliability. There are ways to solve the cost issues, but not at the expense of quality. There may be difficulties for a while, but this will be profitable sooner or later. From an economic point of view, value determines price. Price may temporarily deviate from value, but a dynamic equilibrium can be reached sooner or later. This is my view as a material manufacturer.”