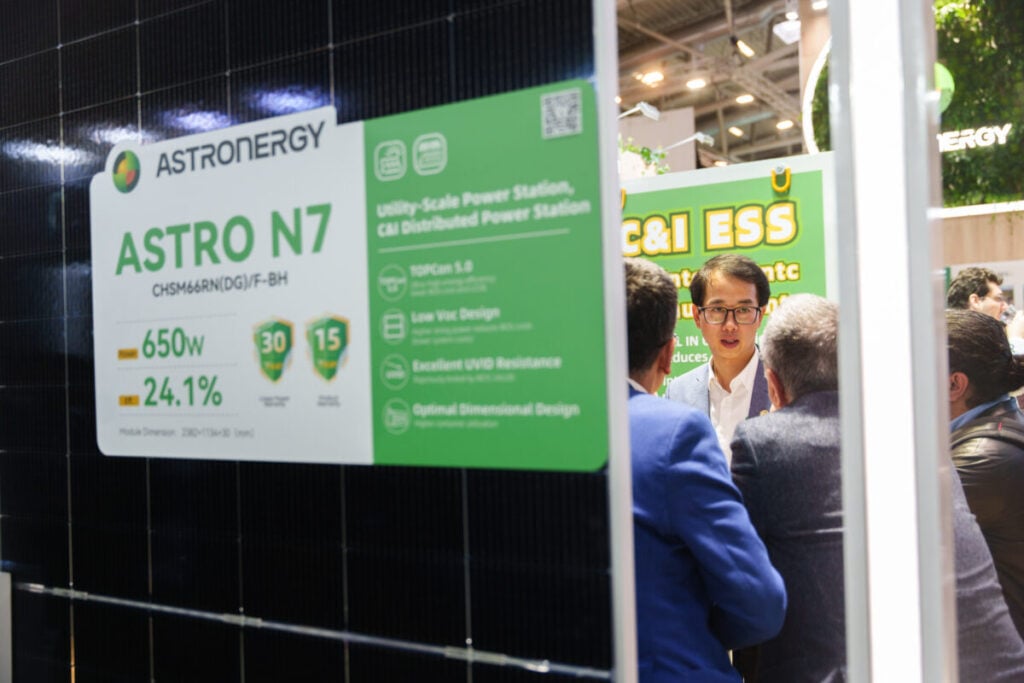
At Intersolar 2025, the global leading PV manufacturer Astronergy’s booth was buzzing as the company showcased some of its latest solar products.
Modules featuring the latest generation of Astronergy’s TOPCon 5.0 technology, which pushes efficiencies to new levels, were among the new offerings the company had on show. Also under the spotlight was Astronergy’s zero-busbar (ZBB) technology, which is claimed to reduce shading losses and enhance overall module reliability by replacing traditional front-side busbars with non-visible contact structures.
Unlock unlimited access for 12 whole months of distinctive global analysis
Photovoltaics International is now included.
- Regular insight and analysis of the industry’s biggest developments
- In-depth interviews with the industry’s leading figures
- Unlimited digital access to the PV Tech Power journal catalogue
- Unlimited digital access to the Photovoltaics International journal catalogue
- Access to more than 1,000 technical papers
- Discounts on Solar Media’s portfolio of events, in-person and virtual
On the sidelines of the event, PV Tech caught up with Shengyong Zhou, Astronergy’s general manager of global product technical services, to get the lowdown on the company’s latest technology upgrades.
PV Tech: Your ZBB technology is one of the big talking points for you this year. Can you give some insight into this new approach?
Shengyong Zhou: We are the first company in the industry to volume-produce solar panels with ZBB technology. For ZBB modules, there are some advantages over previous designs. One is greater reliability because there’s no soldering process as before; we use a carrier film to fix the ribbons on the solar cell surface, and there’s no conventional soldering process. So the temperatures involved are much lower: previously, it was maybe 200 degrees centigrade during the soldering process; now, because we only use the carrier film to fix the ribbons on the solar cells, there is no traditional high-temperature soldering process. The temperature only reaches around 100 centigrade for this process. This lower temperature means there’s a lower risk of internal/hidden cracks, meaning greater reliability.
What other performance or reliability benefits are there from the ZBB approach?
Because there’s no soldering process as before, no flux is needed. This means that the damp-heat reliability of ZBB modules is much better, because with damp heat, the [damp heat] risk is influenced by the soldering flux. But there’s none of this now because there’s no soldering process. The ZBB modules also have a higher static mechanical strength.
How does the ZBB approach compare cost-wise with your previous designs?
For ZBB, there are no PAD points and no cell busbars under the ribbons, so the silver paste cost is reduced. And there’s less shading for the light, because there are no PAD points. This means we can make full use of the light on the front side, and so the solar cell efficiency is improved. So even though we have an additional film and 20 ribbons in the ZBB module, the cost is balanced out by the improved power of the module.
The modules that you’re offering with these new technologies, then, can you talk me through those and where you’re targeting them in terms of the segments that they’re most appropriate for?
Taking European market as an example, we can divide this market into maybe two or three aspects: one for utility, one for C&I (commercial and industrial) or rooftop applications. For utility, we can use a TOPCon 5.0 and ZBB – the module efficiency is improved, and the reliability is also much better. So I think we can use this panel to face utility customers’ demands, because the BOS will be reduced, the power increased and the price kicks in as before.
And for the rooftop application, besides price, I think the key points that a customer pays attention to are, first, reliability, second, power class, and third, appearance. For the rooftop we provide customers ASTRO N7s and we will introduce TOPCon 5.0 and ZBB here as well. So the appearance is very beautiful, and the reliability is good. The power class increased, so it’s really welcomed by customers for this module.
How do you see demand in Europe in the coming years? The region clearly has some ambitious decarbonisation targets, but growth by all accounts looks set to be a little flat for a year or two because of issues such as grid constraints.
The European market is really important, and, besides China, I think it is the second [most important]. The customers here are very experienced and very professional. The grid condition here is not as good as it will be in the future. But I think this situation will be solved in the future with a much better grid condition, and I think the demand will keep going up.
You operate a one-stop service for key customers. What does this mean and how does this model help your customers in project development and long-term asset performance?
We realised that, even though we provide customers with a very good product, during delivery, unloading and installation at the project site, if the operation is not qualified, there may be some quality issues after the solar panels have been installed. So we wanted to provide customers with a service where, before the first batch of solar panels is shipped to the project site, we will go there first and give the on-site operators training and tell them how to do the unloading, unpacking and handling. We show them some of the frequent issues that have occurred in past projects, and after we highlight these issues, I think operators will pay more attention to those kinds of negative situations. It’s really welcomed by our key customers.
TOPCon is obviously the dominant technology at the moment, but what are you doing as a company to invest in the next generation of PV technologies?
It’s a very hot topic, because there are some technologies like HJT, BC or perovskite, being talked about as the next technology after TOPCon. Based on my understanding, actually, we think that in the coming three or four years, TOPCon will still be the mainstream. The key reason is that TOPCon is very cost-effective, and that’s the key point; even though with HJT or XBC maybe the efficiency is a little higher, the cost is also much higher.
The second point is that TOPCon still has a long way to run; currently the average efficiency in the industry is around 25.3%, but the upper limit for TOPCon is 28.7%, so there really exists a big space in the future for the whole industry to make improvements. We have a very clear roadmap to continue making efficiency improvements in the coming two or three years.
So that’s my understanding of TOPCon. And for other technologies of HJT or BC, we will also do some research and reserves. Maybe in the future, XBC will have a cost breakthrough and will be a good option for residential applications, because the appearance is perfect, we have to accept. So we will do research for BC, but we will expand capacity based on cost and efficiency. For example, if TOPCon’s efficiency can go up very quickly and at the same level as BC, why not keep it? So it depends.