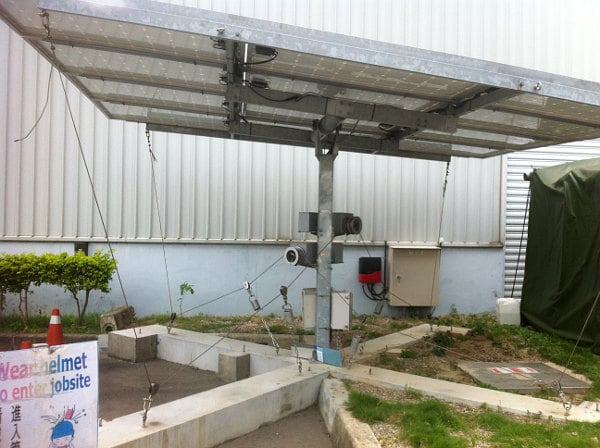
BIG SUN Group, a Taiwan-based PV manufacturer, has developed a commercial dual-axis tracker unit called ‘iPV Solar Tracker’ that is differentiated by using a steel cable drive mechanism.
Unlock unlimited access for 12 whole months of distinctive global analysis
Photovoltaics International is now included.
- Regular insight and analysis of the industry’s biggest developments
- In-depth interviews with the industry’s leading figures
- Unlimited digital access to the PV Tech Power journal catalogue
- Unlimited digital access to the Photovoltaics International journal catalogue
- Access to more than 1,000 technical papers
- Discounts on Solar Media’s portfolio of events, in-person and virtual
Problem
Dual-axis solar tracker is known to harvest significantly more energy compared to other mounting structures. For mass deployment of dual-axis tracking system into the market place, two conditions need to be met; simplifying the hardware structures in order to lower the capital and O&M costs, and also to guarantee stability and reliability against the weather elements. Generally, solar tracking systems use linear actuators, ball screw or slew wheel drive systems which are complex and carry high capital and O&M costs.
Solution
The iPV Solar Tracker drive mechanism consists primarily of electronic control unit, two electric motors, shafts, ball bearings, cable reels, pulleys, anchoring bolts, springs, and steel cables. The two motors are attached to a central pole and positioned perpendicular to each other. Each motor has a two-slot cable reel fitted on a rotation shaft. Steel cables attached to the diagonal corners of the module frame are wound on the reel slots; one in clockwise direction and the other in anti-clockwise direction. When the electric motor rotate the cable reels, the winding and unwinding of the steel cables pulls the module mounting frame into a rotational motion. The pulley connecting the anchor bolt diverts the horizontal force into vertical motion so that less force is used to pull the module mounting frame downwards. The springs connecting the middle anchor bolts help to modulate the tension of the steel cables so that they will not be too tight or too loose. Once the frame moves to the target position, all four steel cables will be tightened, hence providing four anchoring strengths to the mounting frame. The steel cables anchors also provide additional stability to the tracker in the event of gusty wind of up to 137 mph.
Applications
Utility-scale PV power plants.
Platform
The tracking accuracy of the iPV Solar Tracker is managed by an electronic control unit based on astronomical algorithm. This enables a full 360 degree azimuth rotation and altitude tilt of -40 degrees to 40 degrees. The controller algorithm also includes backtracking capability which allows optimization of the ground cover ratio. The performance evaluation of iPV Solar Tracker power plants in Taiwan (23 degrees N) shows an average of annual energy gain of 30% compared to a fixed-tilted PV system.
Availability
June 2015 onwards.