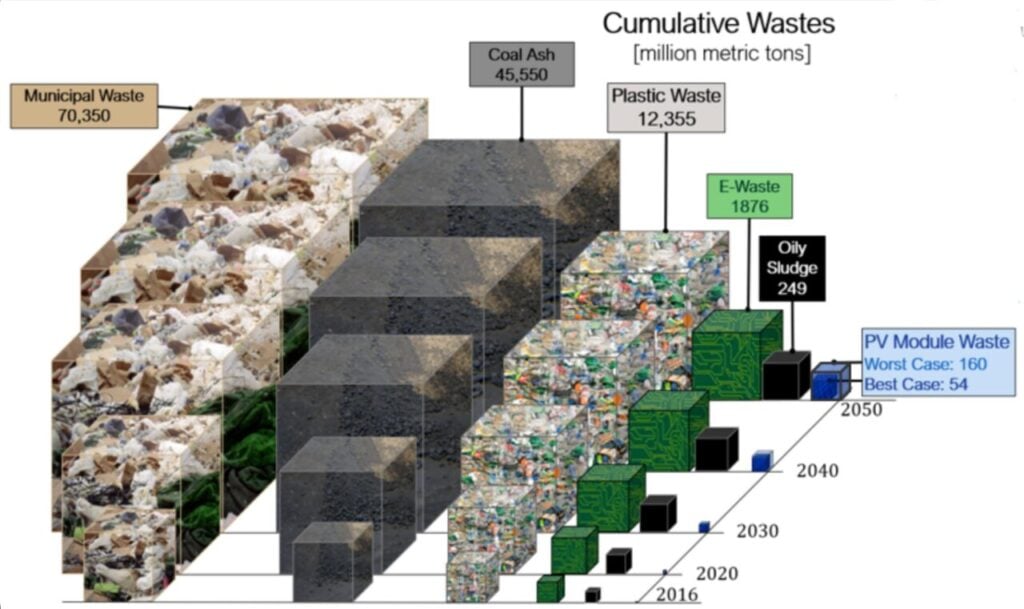
Outdated misconceptions about the toxicity and waste of solar PV modules, including misinformation regarding toxic materials in mainstream PV panels, are hindering the adoption of this technology, according to a US government-funded research lab.
Heather Mirletz, a researcher in circular economy and sustainability of PV at the National Renewable Energy Laboratory (NREL), goes on to tell PV Tech Premium that the most prevalent concerns around PV toxicity may soon become irrelevant. There are fears around lead leaching from solder joints in solar panels and the potential presence of per- and polyfluoroalkyl substances (PFAS), also known as ‘forever chemicals’, in module back sheets.
Unlock unlimited access for 12 whole months of distinctive global analysis
Photovoltaics International is now included.
- Regular insight and analysis of the industry’s biggest developments
- In-depth interviews with the industry’s leading figures
- Unlimited digital access to the PV Tech Power journal catalogue
- Unlimited digital access to the Photovoltaics International journal catalogue
- Access to more than 1,000 technical papers
- Discounts on Solar Media’s portfolio of events, in-person and virtual
However, for several years, there has been a significant shift towards bifacial modules with glass on both sides of the PV panel, eliminating the need for back sheets. Additionally, some manufacturers and even European authorities are moving away from using lead in PV soldering altogether.
There is a need for improved communication from the PV industry to address the concerns of decision-makers, however. A collaborative effort by several NREL authors and an author from DNV last year aimed to dispel misconceptions about PV waste with the publication of the paper ‘Unfounded concerns about photovoltaic module toxicity and waste are slowing decarbonization’.
The paper highlighted that outdated calculations of large future volumes of PV waste, made when module lifetimes were estimated at 12 years, have persisted in communications even though modern modules now have lifetimes exceeding 35 years.
This type of narrative-changing data has not been effectively communicated, but it could be a valuable tool for the solar industry to counter persistent negative perceptions and misinformation regarding the impact of future waste streams. Specialist PV recyclers are making continuous progress in PV module recyclability and can already recycle more than 95% of a panel’s value.
Minimising toxic coal ash and oily sludge
Energy experts have set a target of 75TW of solar PV deployment globally by 2050 to have a chance of limiting global temperature rise to 1.5 degrees Celsius.
Based on this target, NREL has calculated that the amount of toxic coal ash produced globally from coal burning in just one month is equivalent to the total amount of PV module waste expected over a 35-year period (2016-2050). Additionally, the volume of toxic oily sludge from crude oil production would far exceed the volume of PV waste.
The best-case scenario estimates 54 million metric tonnes of PV waste by 2050, assuming long-lasting modules with a lifespan of 40-42 years, while the worst-case scenario estimates 160 million metric tonnes, assuming shorter-lived modules with a lifespan of 20-25 years.
However, Jessie Simons, COO of US-based PV recycler Solarcycle, told PV Tech Premium last year that modules are reaching the end of their life cycles faster than anticipated, with average lifetimes of just 15 years. Despite this, NREL’s calculations show that even in a worst-case scenario, where modules have shorter lifetimes, the waste volumes would still be minimal compared to continuing fossil fuel use.
When asked why the industry hasn’t communicated these findings effectively, Mirletz suggests that the comparison between fossil fuel and renewable energy waste is not immediately apparent. Established waste streams like coal ash and municipal waste tend to draw less attention, as people generally don’t think about them unless there’s a major incident.
Conversely, solar PV, as a relatively new waste stream, naturally attracts more attention. While it’s arguable whether the industry is currently managing PV waste responsibly, there are clear pathways to doing so effectively.
Therefore, it’s crucial to ensure that global recycling infrastructure is prepared for the gigawatts of panels expected to come offline in the coming decades and to strengthen current traceability processes, which are often lacking.
A mysterious toxic list
There have been longstanding, widespread and unfounded claims that solar modules contain materials harmful to human health. Arsenic, gallium, germanium and hexavalent chromium, for example, have been listed as present in solar panels by several US state health department websites, despite the fact that the two dominant module technologies, which account for over 99% of the market, contain none of these materials.
The repetition of similar language across various state department websites suggests that an initial incorrect information sheet may have led to widespread misinformation.
The authors of the NREL paper are unsure of the exact sources of these claims but have proposed several hypotheses for each material. For example, early perceptions may have been influenced by Wikipedia articles that inaccurately listed these materials as components of solar panels at one point in time.
Gallium arsenide solar cells, which contain gallium and arsenic, existed before silicon-based PV technology became widespread, but they are used only in high-efficiency aerospace applications and a few other niche areas. Mirletz suggests a superficial reading of the Wikipedia page could lead to the mistaken belief that gallium arsenide technology is used in standard rooftop or ground-mount PV, which it is not.
Meanwhile, germanium was used in some amorphous silicon modules that were never produced on a large scale. The authors also struggled to understand how hexavalent chromium became mistakenly associated with modern solar panels, hypothesising that it might be confused with solar thermal panels from the 1970s, where hexavalent chromium was possibly used in small laboratory experiments to create a black coating on tubes for heating water.
“That has nothing to do with photovoltaic technology and semiconductors,” confirms Mirletz, who has not ruled out the possibility that some of the misleading information in the public was disseminated by “bad actors” who don’t have the PV industry’s best interests in mind.
‘No evidence’ of forever chemicals
PV back sheets, which are made from a variety of plastics, often include fluoropolymer due to its resistance to outdoor elements. Mirletz points out that many garden lawn furniture pieces are made of fluoropolymer, a similar material.
Indeed, the idea of the presence of forever chemicals in solar products has raised concerns about their presence in PV back sheets, but the proprietary nature of some fluoropolymer manufacturing processes means that it is not clear if PFAS are involved. While the authors are actively seeking more information, Mirletz notes that there’s been no evidence so far of PFAS in PV modules, nor any indication that fluoropolymers used in PV would leach into water sources.
To further allay concerns, the industry is moving away from using back sheets altogether as bifacial glass-glass encapsulation becomes more prevalent, particularly in utility-scale installations.
Challenges for lead testing
Lead is present in around 33% of the thin coating on top of copper conductors in PV modules, and concerns about lead leaching from solar panels are widespread. However, calculating the leaching potential is challenging.
The Toxicity Characteristic Leaching Procedure (TCLP), used to measure leaching, was initially designed for different standards and products. TCLP involves placing portions of a PV module into a leachate to simulate the effects of acid rain and measuring how much lead or other toxic substances leak out. This is problematic because PV modules are heterogeneous, so the test might focus on a solder joint with a high concentration of lead, or a section with no lead at all.
“So far, it’s very challenging to conduct a consistent and reproducible TCLP test,” says Mirletz. “Sometimes it will pass, and sometimes it will fail, without any apparent rhyme or reason, and we don’t have a good standard for sampling a module.”
These concerns may soon be obsolete as some manufacturers are moving toward lead-free products, and European authorities are working on a mandate to phase out lead.
“It’s definitely something that people would like to leave behind,” adds Mirletz.
There have also been tests on modules cracked by hail followed by rain. After the encapsulant layer, there’s a glass sheet, followed by another clear plastic sheet, often made of ethylene vinyl acetate (EVA), the same material used to make Crocs. In a module, EVA is used to keep moisture out.
“So even if you crack the module, you’ve still got a really strong encapsulation layer that acts as an environmental buffer, isolating it from the rain,” says Mirletz.
Although the authors haven’t conducted acid rain and leach testing, most studies suggest that significant lead leaching would only occur if a module was ground into a fine powder.
However, contextual data can again support PV. Any electronic waste (e-waste) containing a printed circuit board (PCB), such as a laptop, has a much higher lead content than a PV module. Mirletz’s research found that the average e-waste item has a lead content of around 5% by weight, whereas lead content in a PV module is less than 0.1% by weight.
These findings are also relevant to cadmium telluride (CdTe) modules, which made up 3% of the global solar market in 2022. There is a similar concern regarding the cadmium layer in CdTe modules, but tellurium and cadmium make up less than 0.1% of a CdTe module.
Is recycling infrastructure sufficient?
While waste management is crucial for ensuring low toxicity, the global infrastructure for solar recycling is still in its infancy. Mirletz is optimistic, however, noting that the industry is beginning to address end-of-life issues and is scaling up efforts at “approximately the right time,” alongside necessary research and development (R&D) initiatives.
PV Tech Premium has also held encouraging interviews with Solarcycle and PV Cycle, an EU-based solar module take-back scheme.
Beyond supporting new entrants like Solarcycle, there is also a need for improvements to foster more research, development, and future scalability. Currently, the overall recycling ecosystem faces challenges, such as the fact that it is still cheaper to dispose of waste in a landfill than to recycle it.
Mirletz explains that the initial goal of NREL’s paper was to “allay the fears that PV waste streams are imminent and going to be a problem in everyone’s backyard”. She emphasises that the industry is ramping up its efforts at the right time and that R&D should continue to be supported.
Countering misinformation
“I would love to see more people asking good questions and getting good facts to answer those questions,” says Mirletz.
She points out that it’s easy to find misleading information online, which can lead to unnecessary concern and widespread misinformation.
For instance, several local city governments have approached NREL seeking expertise on the potential toxicity of solar panels and whether their materials might leach into the environment.
Mirletz stresses the importance of context when discussing these issues. Instead of focusing solely on the waste generated by solar panels, it should be highlighted that deploying solar power significantly reduces waste and toxicity, especially when compared to the oily sludge from crude oil production or the coal ash resulting from fossil fuel combustion.
She frames it as a choice between continuing down the same problematic path or embarking on a new, less toxic one. While the new path may be intimidating because it’s unfamiliar, it ultimately offers a better and less toxic outcome.
Ultimately, the NREL paper states that without a full transition to renewable energy sources, toxic coal ash and oily sludge waste generated from fossil fuel energy would be 300-800 times and two to five times larger, respectively, than PV module waste.
“Putting things into context before jumping at all of these scare headlines is a really good way to go,” says Mirletz. “Don’t panic until you have the facts.”