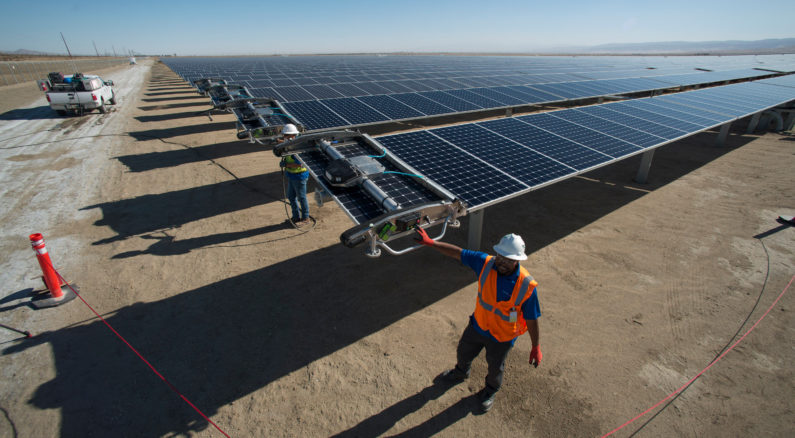
As solar finds itself deployed in further and more far flung climes, it is also having to operate in increasingly harsher climates. In this article, VDE Renewables assesses how such climates affect PV performance and what must be taken into consideration when formulating O&M strategies.
Solar photovoltaic (PV) plants are complex systems, despite being composed of modular equipment that appears simple at face value. The final products such as PV modules, power conversion equipment (inverters, transformers, combiner boxes, etc.), module mounting structure, etc., are installed onsite and the PV plant, together with all the equipment, are then commissioned into operation of a lifetime typically of 25 to 30 years.
Unlock unlimited access for 12 whole months of distinctive global analysis
Photovoltaics International is now included.
- Regular insight and analysis of the industry’s biggest developments
- In-depth interviews with the industry’s leading figures
- Unlimited digital access to the PV Tech Power journal catalogue
- Unlimited digital access to the Photovoltaics International journal catalogue
- Access to more than 1,000 technical papers
- Discounts on Solar Media’s portfolio of events, in-person and virtual
The performance and durability of the different PV plant components varies over the lifetime of a PV plant, and consequently the operation and maintenance (O&M) efforts.
It is obvious that the climatic environment in which the equipment operates will influence the equipment’s rate of aging defect growth, failure progression or degradation; as different materials respond differently to different climatic stress factors such as temperature, humidity, UV light, rain, wind, etc. A combination of these climatic parameters will also create second-order stressors, such as mechanical load from snow or soiling from dust to PV power plants.
Typically, PV plant operators offer a rather standard (O&M) scope of services that could be replicated easily across to reach an optimal point between minimising O&M efforts (and therefore expenditures) while maximising PV plant uptime, performance and durability. However, a shift from the one-size-fits-all approach to a customised O&M approach could offer an advantage that the O&M activities are adapted for the needs of the PV plant, focusing on what maintenance activities are necessary for that specific plant.
Such customisation could be setting an O&M service based on the climate zone in which a PV plant is located. Figure 1 shows a new approach of the Köppen-Geiger PV map [1], which provides classification and implications to worldwide mapping of PV system performance with respect to temperature, annual insolation and precipitation.
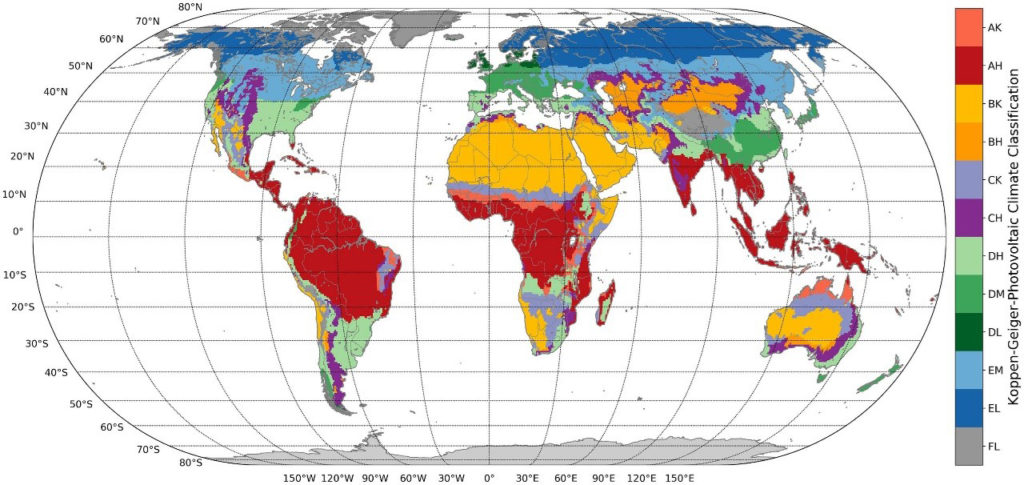
One of the main challenges in customisation of an O&M strategy for a specific climate zone at present is the lack of comprehensive guidelines for O&M providers. Existing guidelines and standards do not fill the gaps or clarify the minimum requirements of climate-specific O&M and their implementation. In this paper, we aim to provide comprehensive guidance on setting up a customised O&M practice for PV plants located in three different climate zones: moderate, hot and dry as well as in flood-prone (monsoon) climates.
While the first two refer to general climate zones, the last one is more specific to extreme weather conditions. The recommendations for an optimal and appropriate O&M strategy for PV plants in specific climates are prepared based on real field experiences of experts from various countries representing the climate zones addressed [2].
Rapid response
There are different key performance indicators (KPIs) for O&M contracts of PV power plants, and they are tied directly to the performance of the PV plant such as the performance ratio (PR) and the plant availability, or the maintenance services performed.
The response time is an O&M KPI that is based on the maintenance service performed. Some O&M operators may opt to guarantee maintenance response time to faults/alarm events. This is usually expressed in minimum time intervals (in time units such as minutes or hours) to trigger an intervention and is timed from the moment the event or fault occurs. In this approach, the response time should be categorised into responses to critical, major, and non-critical events. Faults or events with immediate impacts on the safety operation of the PV plant, such as a fire event, are critical and require immediate intervention. Faults or events with major impacts on the plant production, such as inverter shutdowns, require a response within a day or two from the alarm trigger.
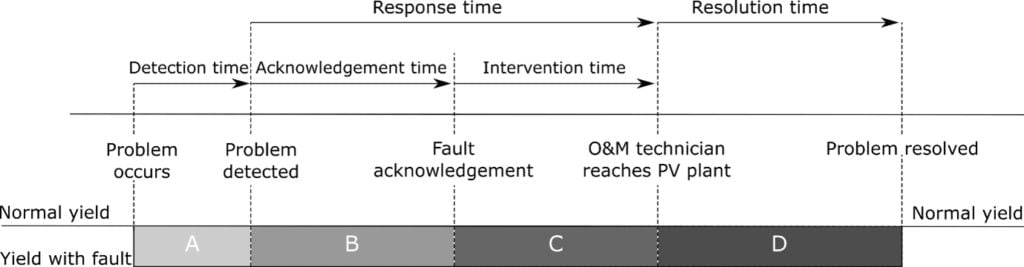
Figure 2 shows the O&M KPIs relating to response and resolution time, and the associated yield losses for each phase. In many cases, the detection time will be very short, although this depends on the nature of the SCADA system and the type of fault. Depending on the contractual framework, the yield lost (the areas indicated by the letters A to D) may be excluded or not from KPI shortfalls and penalties.
- Detection time: depends on type of fault, monitoring software (difference between ((rapid)) degradation, shading, inverter issues, etc).
- Acknowledgement time: depends on detection mechanismand awareness/action by O&M provider
- Intervention time: Time taken for O&M personnel to mobilise onto site. Depending on system scale and remoteness, this is nil (for staff based on site) to days or even weeks for remote/hard-to-reach systems.
- Resolution time: Once the issue has been properly diagnosed and a solution determined and agreed upon with the asset owner (if applicable), resolution time can be short (hours-days) to long (days-weeks) to very long (months). Here, spare parts management by the O&M provider and the risk (and cost) appetite by the asset manager play an important role.
Digitalisation will enable the creation of BIM/Digital Twin concepts which will allow an asset to be properly followed along the whole value chain down to component level, from the manufacturing phase, through engineering, procurement and construction (EPC), O&M and end of life. The development of data-driven and/or physical models (reliability models of PV modules, inverters and other BOS components) will enable predictions of the lifetime based on field data including climate dependent stress factors, which then feeds into data-driven O&M strategies. Despite the rapid professionalisation of the PV industry, data-driven O&M strategies are still in their relative infancy and require further work.
Recent evolutions in contracts for O&M have seen the KPIs change from PR or energy-based values to service time values: response and acknowledgement time. This reflects the growing awareness that the O&M provider needs to be evaluated on aspects which are (easily) measurable, and that the performance of the PV system was determined in the design and installation phases. From this revised view, the O&M provider is tasked with ensuring that the PV system can operate to the best of its capabilities as they have been received/inherited from the previous responsible party (EPC, or O&M provider), ensuring that inverters are online, that PV module trackers operate within specifications and so on.
Yet the O&M provider is not responsible for the behaviour of PV modules and inverters under weather and operational constraints. It should be clear that the best and most nuanced approximation of the true health of the PV power plant, as well as how well the O&M contractor is performing, are obtained through the judicious application of multiple KPIs.
A key tool to minimise or eliminate risks is the hierarchy of controls methodology, as shown in Figure 3. At the O&M stage, the ability to eliminate risks is limited compared to the design and construction phases (where safety can be designed into (or omitted in the design of) the PV plant) unless additional investments are performed. The O&M operator will have most control of risks from engineering and administrative controls as well as the appropriate use of personal protective equipment (PPE), while elimination and substitution of risks are typically part of the plant design.
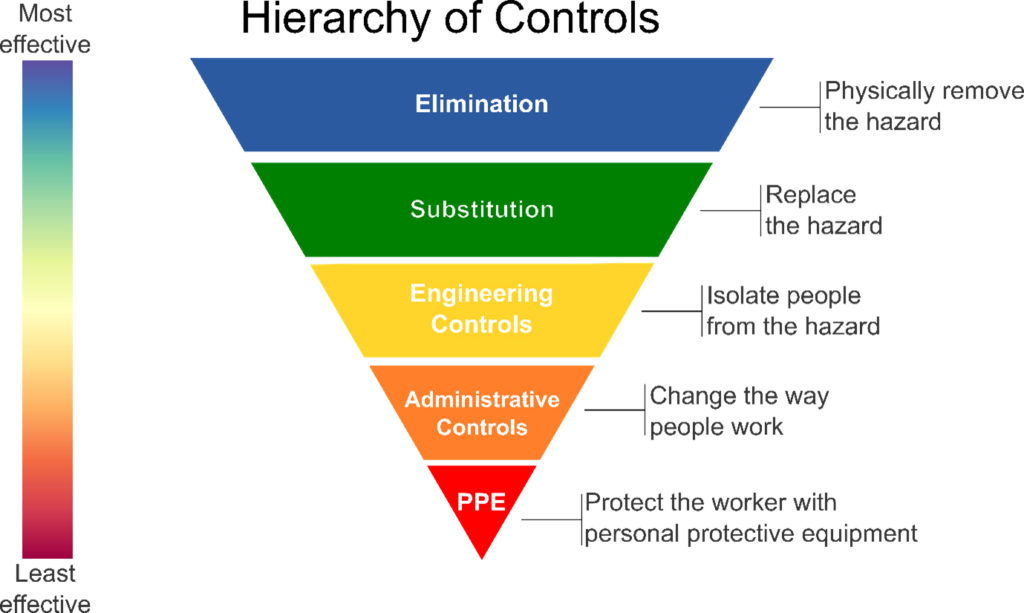
O&M in moderate climates
The O&M guidelines for moderate climates cover the basic or most common aspects and conditions that are common to different climates or regions. More extreme climates have different specificities and may require more attention for operators and strategies for maintenance.
Moderate climates are very well suited for the development of vegetation and wildlife throughout the year, so that the seasonal changes are smooth enough for the survival of many species. Although this may seem contradictory today, the development of nature near PV modules, inverters, etc. is not always welcome.
Among other things, vegetation and wildlife can become a problem during certain periods of the year, affecting energy yields. In temperate climates, soiled PV modules often contain bird droppings, agricultural emissions, pollen, lichen and traffic residues, such as engine exhaust, and show strong seasonal variations. With frequent rainfall, most of the pollution is washed off, but there are conditions, especially during a dry period or heavy agricultural activity, where the pollution rate – the comparison between clean and dirty – can vary by several percent.
There are several methods to contain soiling – preventive and restorative – such as manual, semi-automatic or fully automatic cleaning solutions. Fully automated, pre-installed solutions with very low water consumption or even dry brushing are attractive for large facilities in regions with a very high risk of soiling. On the other hand, semi-automatic or manual cleaning systems using demineralised water or some biodegradable chemicals to wash off organic matter might be more cost-effective in temperate climates. There is no one-size-fits-all solution for mitigating pollution impacts. It is a local economic decision based on labour costs, availability and cost of water, feed-in tariffs and medium-term weather forecasting.
Bird droppings are the biggest problem for yield when it comes to soiling of PV modules in temperate climates. It is important to create a cleaning schedule based on the frequency of bird droppings, which is highly dependent on the type of birds that live in the area and pass through it on their migration route. This planning should prevent drops from sticking to the module glass for a long time for the following main reasons:
- Loss of energy output.
- Hot spots leading to material deterioration and increased electrical risk.
- Etching effect on the glass, leaving a non-removable mark on the surface.
It is important to be aware of the risk of various chemical products that can be harmful to the glass, the glass coating and the frames of the PV modules. They can put both the module and the product warranty at risk.
For rodents, it is recommended to secure cable loops and hanging cables as far as possible from the ground or from structures that can easily be climbed. If more protection is required, solutions are available on the market to protect against rodents, such as cable shields.
Most animals living near PV ground-mounted modules are livestock such as grazing sheep. They can control the vegetation in PV installations and usually do not climb on or damage the PV modules. The first row of modules may be exposed to them, which could be pushed by their bodies when they reach the growing grass under the PV modules. In general, it is worth mentioning that both the PV modules and the structures are a good opportunity for them to scratch their skin if necessary. It is recommended to check the mechanical condition of the structure and the first row of modules regularly.
For insects, the cool shade under a PV panel and the empty interiors of metal structures are often ideal for building wasp or bee nests. In the case of metal structures, plugging the holes can prevent a nest from being built inside. On the back of PV modules, nests tend to become entrenched in frames and cables, making maintenance difficult.
Cutting or spraying with herbicide is the common method of controlling vegetation. The herbicide should be applied in an appropriate manner without spraying the PV modules. After a few days, when the vegetation has died, it should be pulled out by the roots and the waste treated accordingly.
In relation to occupational safety and health, international standards and national codes are an important reference (Table [1]). Public guidelines developed by industry, research or national institutions are also a good source of summarised and detailed information, as listed in Table 1.
Country / Continent | Title | Author/Editor | |
Europe | Operation & Maintenance Best Practice Guidelines / Version 4.0 | SolarPower Europe | |
India | Best Practices in Operation and Maintenance of Rooftop Solar PV Systems in India | Gujarat Energy Research & Management Institute | |
Japan | Report on Guidelines for Periodic Inspection and Failure Examination of PV Power Systems | Japan Electrical Safety & Environment Technology Laboratories | |
United States | Best Practices for Operation and Maintenance of Photovoltaic and Energy Storage Systems; 3rd Edition | National Renewable Energy Laboratory and others |
O&M in hot & dry climates
In hot and dry climates (Köppen-Geiger PV classification: BK) there are high summer ambient temperatures (often reaching 40°C / 104°F) and very little precipitation. Typically, precipitation comes in the form of heavy downpours, with little or no rainfall for much of the year.
The combination of physical remoteness and challenging climatic conditions results in a strong preference for remote monitoring of PV plants, with few plants having O&M staff on-site or nearby. This is reflected in the O&M KPIs, where availability values of less than 99% are occasionally observed.
The greatest risks for maintenance staff working on PV systems installed in these regions arise from the high temperatures and high irradiance (with high UV content) that can routinely occur. Therefore, site visits typically need to be scheduled in the early morning hours, often with two or more workers for mutual support and back-up. Similarly, if modules are cleaned with water, the cleaning work must also take place in the (early) morning hours to avoid temperature shocks and glass breakages. Occupational Health and Safety (OHS) requirements dictate the use of appropriate PPE, which must also provide protection against sunburn and heat stroke.
In addition, heat (stress) management and mitigation plans are required to ensure that staff are adequately hydrated and can take a break from the heat. The potential presence of venomous insects and animals also needs to be considered in O&M procedures, such as identifying actions to take in the event of snakebites, e.g. providing antivenom near the PV system, or having wildlife specialists on call to remove venomous snakes from the property.
Regarding the hardware, birds, termites and ants can build their nests near PV modules and inverters, which can lead to fires or short-circuits. Cable ducts should be sealed, and electrical cabinets must be inspected at regular intervals, as termites and other pests can travel towards inverters or cabinets, and extra care must be taken when opening the cabinets.
Travelling to remote PV sites is an underestimated risk by many O&M contractors: stray livestock and other large animals can be encountered during the trip, as can the possibility of flash floods making roads impassable for hours and ensuring that a (charged!) satellite phone, first aid kit and sufficient water for both the car and the passengers are available before the trip can be forgotten for “routine” work. Preparation, communication and logging of travel plans, and O&M activities is therefore of great importance.
When vegetation is present, soiling of PV modules is usually less of a problem in hot and dry climates; instead, yield losses due to rapid crop growth after rain events are possible. In these areas, vegetation management is also implemented together with fire breaks (physical barriers that impede the spread of bushfires, such as cleared roads at the edges of PV plants) to facilitate access to the PV arrays. Vegetation management is often reactive, i.e. following rapid vegetation growth after rainfall events, and the contracts often reflect these reactive activities. Due to the relative remoteness of such PV sites and their impact on the system maintainability, combined with relatively low pollution losses, the use of automatic soiling management systems (e.g. cleaning robots) has been limited to date.
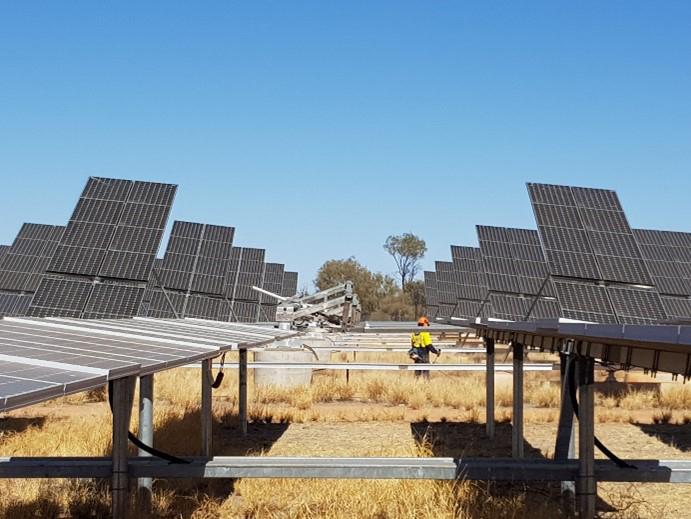
In hot and dry climates without vegetation, on the other hand, soiling losses are usually higher, and therefore the need for automated module cleaning solutions has increased. The difficulty and higher cost of obtaining water (and occasionally, with high mineral content, which can leave mineral deposits such as calcified film on the module glass) have led to a preference for low-water or no-water solutions for module cleaning, such as fully automated dry brushing.
O&M in flood-prone (monsoon) climates
In theory, for easiest O&M and overall lowest cost, PV power plants should be installed in areas that are easily maintained with low weather and climate risks. However, in many countries, social license requirements force PV systems to be built on land unsuitable for agriculture and other commercial activities. Moreover, an underestimation of flooding risk in the development phase, by looking at too short a historical dataset or ignoring changes to the surroundings (such as upstream clearcutting of forests, or newly developed areas), see PV power plants located in areas with high (flash) flooding risks, which is particularly pronounced for areas with monsoon-like climates.
When exposed to floods, PV power plants are subjected to two main types of stressors: fast flowing water and/or impacts with debris, and continuous submergence. The first category often results in (catastrophic) damage that is visible to the eye, whereas the second sees a combination of electricity and water, and unintended/unforeseen current paths, which can cause less obvious damage to infrastructure, requiring specific inspection methods to ascertain the health of the PV power plant (IR, EL, I-V curve measurements, isolation checks).
In this regard, experiences from Kerala, India (Köppen-Geiger PV AH: monsoon climate) are illustrative of the challenges experienced by asset owners and O&M contractors with flooding of PV power plants. In general, (partial) submersion of PV system infrastructure (arrays, cabling, string combiner boxes, inverters, electrical cabinets and transformers) can lead to large, yet unexpected forms of damage or yield loss. Forms of damage range from bent modules, broken or melted module glass, deformed or damaged junction boxes, or even permanent forms of soiling can be seen after flood events, all the way to unexpected current paths resulting in short circuits in string combiner boxes, electrical cabinets, inverters and transformers. It’s important to note that, if a system has been (partially) flooded, damage may be present in hardware, regardless of whether it has been submerged, and this can manifest even days or weeks after the flood event.
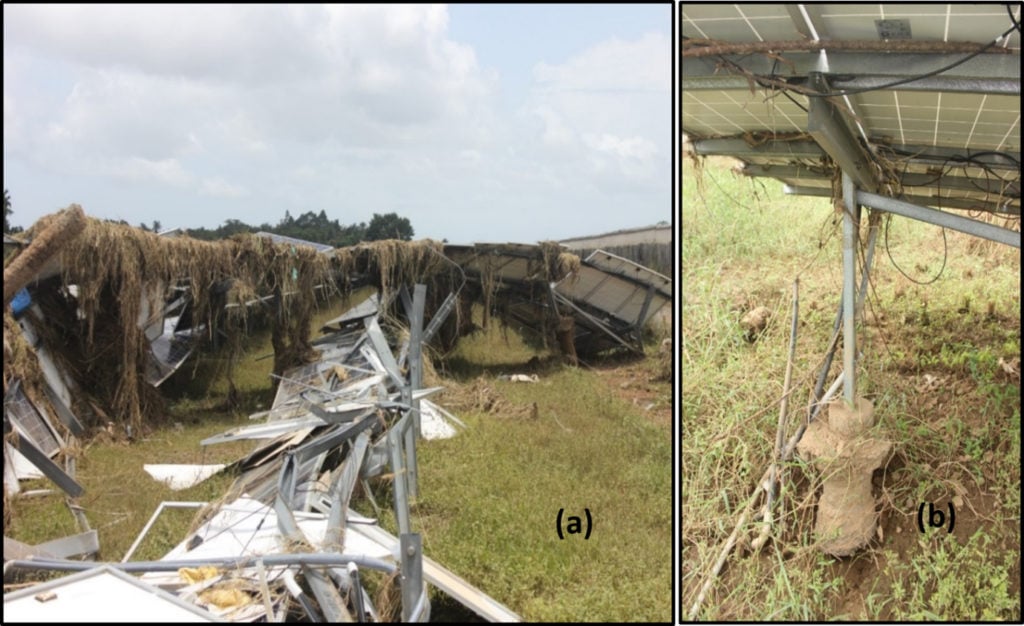
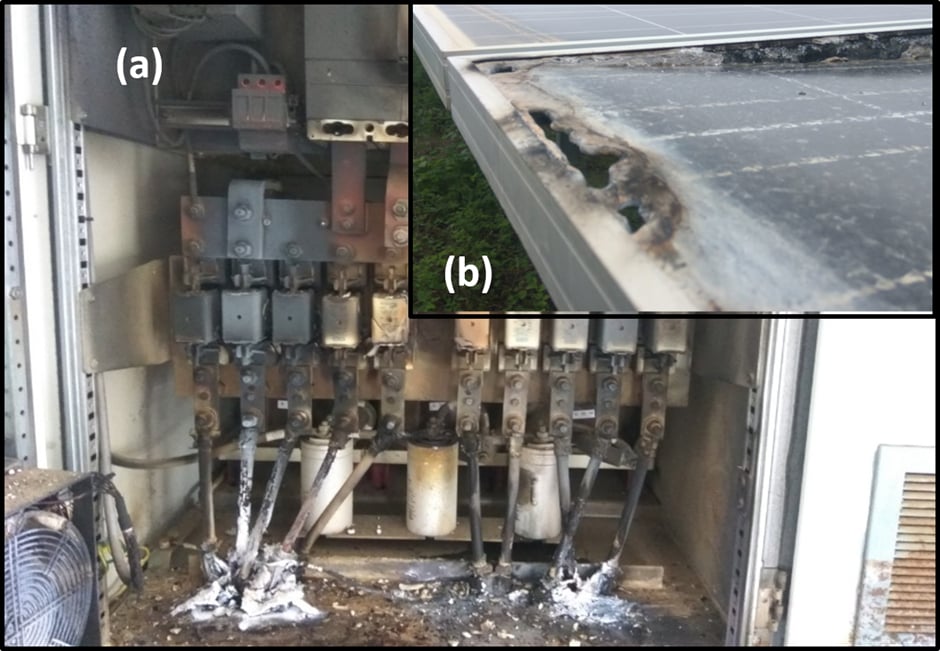
Figure 5 and Figure 6 show the spectacular damage that can occur for PV systems subjected to flooding. Figure 7 shows how some PV systems can be fully submerged for days or weeks.
Depending on the power plant design (e.g. raised inverters, channels to guide flood waters), equipment used (e.g. IP67 or IP68 junction boxes of PV modules), and the extent of the damage, post-flood equipment checks similar to the commissioning of power plants are required to ensure the continued safe operation of the asset.
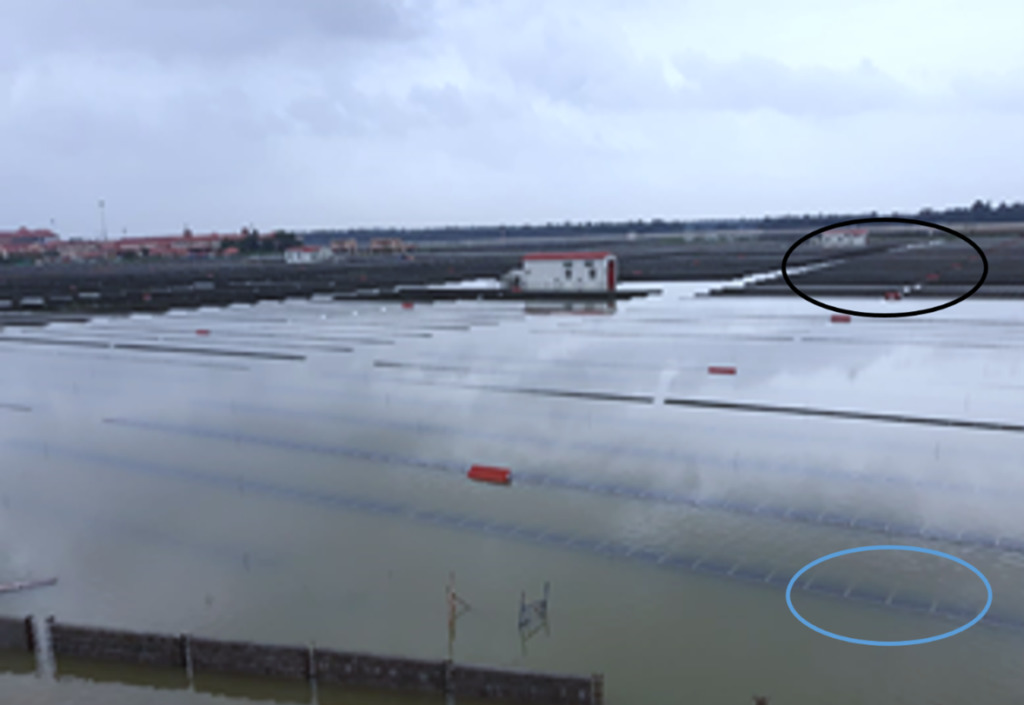
It should be clear that the magnitude of damage to PV power plants can be so large that evaluation of O&M contractor performance using standard KPIs is not always feasible, instead becoming an insurance matter.
For OHS, the precautionary principle mandates that for O&M activities the entire system should be treated as if it was submerged (with higher risk for staff and hardware), unless there are objective reasons to treat (part of) it as safe. Similarly, snakes, spiders or crocodiles may have been transported to the flooded PV power plant area and due care should be exhibited by staff when performing inspections or remedial work.
Outlook for the future: risk appetite, climate change and incentive structures
As the capital expenditures (Capex) for PV plants has rapidly decreased in the recent years, operational expenditures (Opex) play an increasingly important role in the system’s return on investment and the system levelised cost of energy (LCOE), especially, when the lifetime of PV plants exceeds 25 years.
Although PV power plants have relatively low Opex compared to other electricity generation technologies, they still require maintenance to achieve their full potential over their lifetime. Assessing the balance between potentially lower returns (i.e. higher revenue losses) at lower Opex and higher returns at higher Opex is a risk assessment that may need to be reviewed during the life of the plant, to ensure that the risk-return structure is as intended. This raises questions about spare parts management: should critical spare parts be purchased at the beginning of the power plant’s life and stored nearby, or are there mechanisms to defer certain purchases to a later stage in the life of a PV system? The risk tolerance of the asset owner will play a role in this decision. Given the supply chain disruption resulting from the Covid-19 pandemic, it is worth re-evaluating whether the spare parts strategy is still fit for the purpose, especially for critical items with long lead times such as inverters in the MW range.
For larger O&M contractors managing a portfolio of PV power plants, it may be worthwhile to centralise the storage and purchase of critical/important spare parts (inverters, PV modules, Ring Main Units (RMUs), etc.), although this depends on how the O&M strategy for individual PV power plants has been designed and the contractual framework for multiple plants. Similarly, evaluating the risk profile of PV power plants in different climates may prove beneficial – the interested reader can consult [3] for best practices for O&M in other climates.
The increased frequency of extreme weather events (EWEs) due to climate change poses a challenge for asset owners and PV plant operators, as the assumption of a constant probability of extreme weather events over the lifetime of the PV system no longer applies, and can lead to catastrophic damage to the system or nearby grid infrastructure. For example, 100-year rain or flood events may occur more frequently than expected/assumed during planning, or hurricane-force winds may damage the modules and their mounting systems. Consequently, the asset owner needs to re-evaluate their risk appetite and the willingness to pay for higher resilience of the PV system (e.g. physical elevation of inverters, installing flood barriers, installing hardware and software to proactively shut down PV plants in case of EWEs).
For O&M providers, preparing for the consequences of EWEs may involve updating procedures for staff safety, proactive weather monitoring (both for staff visits before/after EWEs as well as for the PV plant itself), re-evaluating spare parts supply management and storage locations (having a spare parts warehouse on site can reduce “standard” O&M costs, but may result in additional problems if that site is hit by an EWE, as the spare parts are also likely to become unusable).
One topic that the PV industry needs to work on further concerns incentive structures and attitudes: the contractual framework as currently used in the majority of systems provides an incentive for the O&M provider to try (only) “good enough” efforts, as there is no benefit sharing. Related to this is the binary attitude shown by some asset owners: if return-actual > return-target: take no action, if return-actual < return-target t: contact/penalise O&M provider. In some cases, such as those with greater solar irradiation, the absolute yield increase may be greater than the expected performance loss rate (and thus a happy asset owner), but the health of the PV system may decline faster than anticipated, which is masked by the higher absolute yield. On the other hand, a year with poor insolation can lead to lower absolute yields than expected, even though the PV system is well maintained.
The PV industry is therefore best served if well-informed stakeholders can discuss and evaluate system performance, the objects of which are better aligned with the long-term reliable operation of power plants. Only if plants meet or exceed their expected lifetime and associated yields, facilitated by sound operation and maintenance, will they fulfil their potential for cost-effective low-carbon power generation.
References
[1] Ascencio-Vásquez, K. Brecl and M. Topic, “Methodology of Köppen-Geiger-Photovoltaic climate classification and implications to worldwide mapping of PV system performance,” Solar Energy, vol. 191, pp. 672-685, 2019.
[2] National Institute for Occupational Safety and Health, Hierarchy of Controls, https://www.cdc.gov/niosh/topics/hierarchy/default.html, 13/01/2015.
[3] Report IEA-PVPS T13-25:2021, Guidelines for Operation and Maintenance of PV Power Plants in Different Climates. U. Jahn, B. Herteleer, et. al., ISBN 978-3-907281-13-0., December 2021.
[4] | N. Shiradkar, “Reliability and Safety Issues Observed in Flood Affected PV Power Plants and Strategies to Mitigate the Damage in Future,” in 46th IEEE Photovoltaic Specialists Conference, Chicago, IL, USA, 2019. |
Authors
Ulrike Jahn, VDE Renewables, Germany
Dr. Bert Herteleer, KU Leuven, Belgium