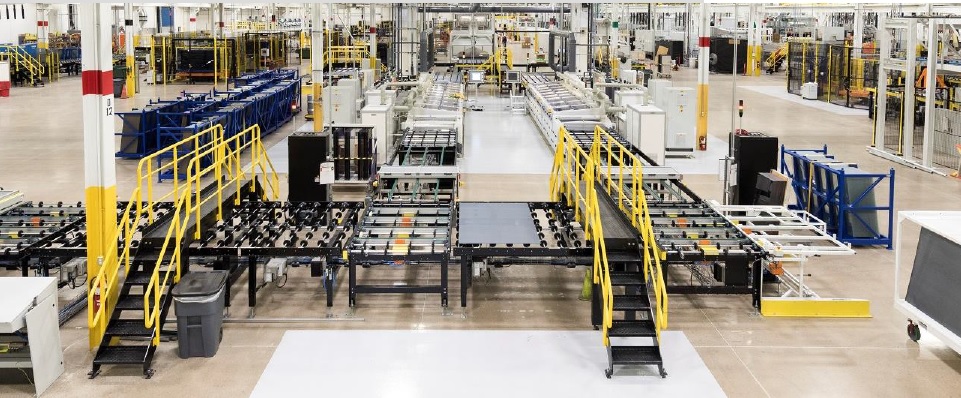
In reporting second quarter 2018 financial results, First Solar revealed that it was having Series 6 production issues at its lead Ohio factory.
The company took the time in its earnings call with analysts to detail the problems, which centred around a yield issue at a specific tool/process at the upstream cell level, that then impacted downstream assembly throughput, aggravated by insufficient buffer stations.
Unlock unlimited access for 12 whole months of distinctive global analysis
Photovoltaics International is now included.
- Regular insight and analysis of the industry’s biggest developments
- In-depth interviews with the industry’s leading figures
- Unlimited digital access to the PV Tech Power journal catalogue
- Unlimited digital access to the Photovoltaics International journal catalogue
- Access to more than 1,000 technical papers
- Discounts on Solar Media’s portfolio of events, in-person and virtual
Not surprisingly, and I would not blame them, First Solar’s management did not reveal the specific tool and therefore cell process that was giving them yield issues. However, the yield issue led to shutting down of specific tools to diagnose, fix and recalibrate before testing and restarting that production step.
In the earnings call, Mark Widmar, CEO of First Solar said, “We have a single point of failure on the production line today.”
It is also important to note at this time that the Ohio factory is still in initial ramp-up mode with the first iteration of a complete new toolset for the large-area Series 6 modules. This is not mature production line(s) and the ability to make a perfect ramp to full nameplate capacity with everything new would be seriously impressive but unlikely.
Theory of constraints
In the typical linear thin-film module manufacturing flow, rather than batch-based flow where steps are generally isolated and have buffer stations, a single point of failure as Widmar described can create bottlenecks or throughput constraints before and after the point of failure.
“If that tool goes down, everything upstream is shutting down and we're starting the downstream processing, right? So, that tool is critical because it's a single point of failure. We have to have the availability and we've identified where those points are and what we're going to do is we'll buffer it with inventory. So, if the particular tool goes down, we aren’t starving the balance of the production and we can continue to run the production as an example, right?
In other words, the throughput impact of First Solar’s single point of failure (yield issue) at the specific tool can be reduced significantly if a sufficient amount of in-spec modules are produced and stored (buffer) so that the next steps are not starved of semi-completed modules so the final steps to complete modules can operate to their cycle time and throughput requirements.
The impact was and can be significant. Management noted that when the point of failure occurred, capacity would go from almost 100%, straight down to 20%.
This was certainly an unexpected point of failure as First Solar is rushing to provide enough buffer stations in the manufacturing flow to minimize the cycle time and throughput issues it is currently experiencing.
“The layout at the back-end of the line was built according to the tool set availability specification which resulted in fewer acquired buffers. As we started to ramp the back-end of the line with a tool set availability not yet at a mature state, we realized there were multiple single points of failure in the line that could shut down production. Effectively, the line was not adequately buffered given the current format of the tool sets”, added Widmar.
“We are in the process of installing inventory accumulators to properly buffer the back-end of the line. Once completed in our Ohio factory, we will use our Copy Smart approach to roll out to Malaysia and Vietnam. Over time, as the tool set availability improves, while the inventory accumulators will remain in place, the need for inventory buffers will decline.”
First Solar noted that the resulting constraints, although minimized eventually would lead to an annual shortfall of finished module output of around 200MW.
This is due in part to the fact that the company would not have all of the buffers in place to hold un-finished module inventory for back-end completion at the end of the third quarter of 2018 or near the beginning of the fourth quarter of 2018, according to Widmar.
“It is important to note that despite the 2018 volume reduction with the actions we are taking we anticipate to exit the year at the originally anticipated throughput levels and enter 2019 on track to our previously announced Series 6 production volume,” noted Widmar in the earnings call.
Editors note: A short 2 hour video by the guru of 'Theory of Constraints' is posted below.