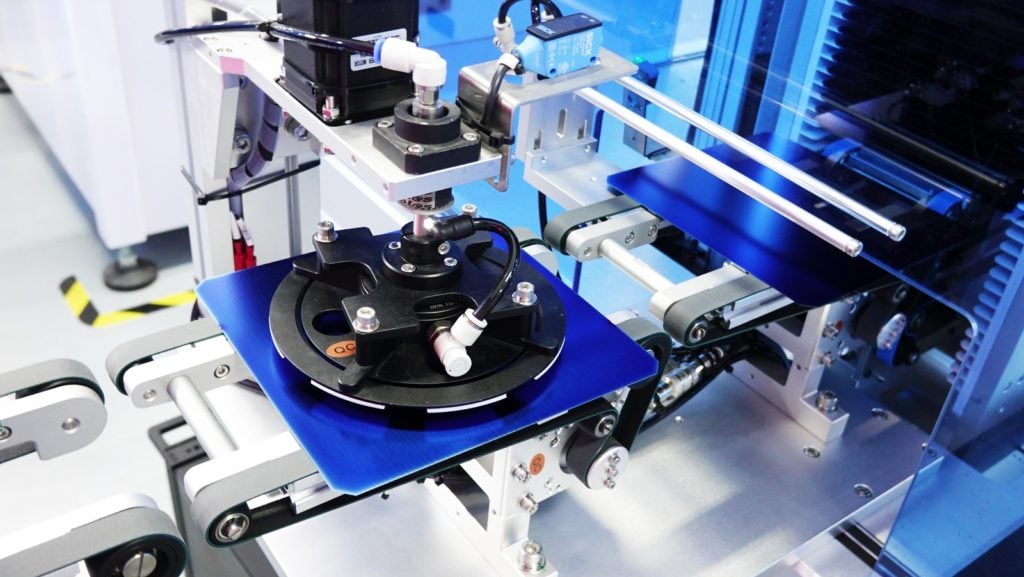
Ahead of a special webinar held next month, Finlay Colville, head of market research at PV Tech, discusses the key trends affecting the PV industry today, from technology leadership, value chain scale and overall financial health of today’s manufacturers.
During the past 20 years, one of the key themes I have constantly returned to when analysing the PV industry is the interplay between technology leadership, volume mass production through the value chain and staying attractive as an ongoing business concern.
Unlock unlimited access for 12 whole months of distinctive global analysis
Photovoltaics International is now included.
- Regular insight and analysis of the industry’s biggest developments
- In-depth interviews with the industry’s leading figures
- Unlimited digital access to the PV Tech Power journal catalogue
- Unlimited digital access to the Photovoltaics International journal catalogue
- Access to more than 1,000 technical papers
- Discounts on Solar Media’s portfolio of events, in-person and virtual
It turns out that being too clever on this issue is not a good idea! What makes sense one year can look completely wrong in 18 months. Sometimes in the PV industry, reality really does defy logic!
Instead, it is better to have a good understanding of each of these three issues: technology used in the PV industry and trends; manufacturing in volume with state-of-the-art production lines; and how companies can make the right decisions to stay in operation and avoid the pitfalls leading to insolvency.
Each year, things change for each of these issues. But every 12 months, we get a bit wiser by way of the industry having grown up another year.
To help explain all this, PV Tech is putting on a special one-off webinar, free to attend on 5 April 2022. Details on how to register can be found here.
This article reveals the start-studded speaker line-up for the two-hour webinar, previews the topics to be covered, and discusses some of the themes that have underpinned PV technology, mass production, and financial stability of leading manufacturers within the PV industry over the past decade.
Outline of the webinar on 5 April 2022
The webinar on 5 April 2022 has four invited speakers that are widely acknowledged as leaders across the key themes outlined above.
For the technology part, two talks will address the new technologies that are seeing massive investments this year across the manufacturing value chain: heterojunction and TOPCon.
The heterojunction talk will be delivered by Martin Green of the University of New South Wales (UNSW). Martin barely needs an introduction. The PV industry is still working its way through a technology roadmap that was basically developed by Martin Green’s PV research team at UNSW back in the 1980s. The talk will explain the basics of heterojunction cell design, what the potential is for cell efficiency and the challenges to bring this into volume production today.
The other leading candidate for next-generation technology in the industry today is TOPCon. This technology is well advanced in terms of mass production, in particular from Chinese companies Jolywood and JinkoSolar. The talk on TOPCon will be given by Ralf Preu of the Fraunhofer Institute for Solar Energy Systems in Germany. This talk from Ralf is one I have been looking forward to for more than five years. Back at the first PV CellTech event in 2016, while the industry was still debating the move from p-type multi to mono and Al-BSF to PERC, Ralf gave a presentation that highlighted TOPCon cell technology as a next technology platform within the sector.
The third presentation addresses the second theme of the Webinar: mass production manufacturing of solar cells. While the industry has been through massive changes in the past 20 years, regarding cell process flows and wafer substrates, JA Solar has probably been the most technology-credible silicon-based proponent. Indeed, when Chinese companies started mass production on a competitive basis, JA Solar was one of the few that prioritised technology at the cell production stage. Many of the other Chinese entrants at the time set up module assembly factories and imported cells from Taiwan producers. While this provides the backdrop for JA Solar’s technology leadership position in the industry today, it is also important to make the right decisions at the right time, in terms of introducing new technologies into mass production. In this respect, JA Solar has led the way in China. And this is precisely what the talk from JA Solar will focus on, to be delivered by Xinwei Niu.
The last piece of our Webinar jigsaw focuses on what makes PV manufacturers profitable, investable, and valuable as ongoing entities. Anyone tracking the PV industry over the past couple of decades will have seen companies enter the sector, make strong investments into capacity, production and technology, only to ultimately run into cash-flow and debt problems. During a fireside chat, I will be discussing these issues with Philip Shen, the managing director and senior research analyst (Cleantech) at ROTH Capital Partners. ROTH has probably been the leading equity analyst firm covering the PV industry during the past 20 years, and Phil is known to many today as the first person to ask the probing questions on PV manufacturers’ quarterly earnings calls. We will discuss what trends can be gleaned from years of tracking PV manufacturing investments, return-on-capital and valuation.
Some thoughts on technology, manufacturing and financial health of the industry in 2022
To set the scene for the webinar on 5 April 2022, I will now look at some of the issues today regarding technology, manufacturing and financial health.
Let’s address this from a value chain perspective, although one could alternatively review these same issues by geography or end-markets served. I will stick mainly to 2022 issues, with an eye on 2023. The analysis is taken from the most recent PV Manufacturing & Technology Quarterly report release.
First up are polysilicon producers. Production here is dominated by just eight companies making about 95% of the material used within the PV industry, of which more than 75% of production this year comes from the top five companies that are all Chinese. All expansion plans today (some real, some speculative) are coming from Chinese companies (existing players and new entrants), with all new capacity outside Xinjiang, and predominantly located across Inner Mongolia. Technology change is all about being n-type cell purity compliant. This follows the upgrades of legacy plants a few years ago to allow for the p-type multi to p-type mono industry change.
From a financial health standpoint, these are halcyon days for polysilicon producers. Being the gating factor in supply keeping up with blistering end-market demand growth is where every manufacturer wants to be. Profitability has rarely been as good as it is today making polysilicon, and this extends to the two main non-Chinese companies, Wacker and OCI (former Tokuyama site in Malaysia). One only wonders what OCI is making of its decision to exit polysilicon production (for the PV industry) in Korea a couple of years ago!
Moving on to ingot production, this has become way more technical than it was a decade ago. When the PV industry moved from gigawatt annual production to the 50GW level, it was characterised by multi ingot casting (more accurately, bricks not ingots); a low-spec process that was fit for purpose at the time and helped keep wafer costs low through the value chain. However, as soon as the time came for mono to prevail in the sector, all this casting capacity became obsolete overnight. Ingot pulling today is a mass produced solar sector phenomenon, and no longer an off-spec by-product of the semiconductor industry.
Technology advancement has been exceptional in the past few years, with wafer quality (essentially defined by ingot purity) likely soon to reach or surpass what is available to the semiconductor industry. Who would have thought that 15 years ago? Even more so than polysilicon however, ingot pulling is a China-owned sector, with just a couple of companies outside China (or Chinese-owned) making product today. Ingot pulling is driven by LONGi Solar and Zhonghuan Semiconductor with more than 60% share this year. In fact, a select group of 10 companies in China will make about 99% of all ingots for the PV industry in 2022. Ingot pulling by itself is not a viable business however, and there are no pure-play ingot producers in this 99% grouping. Ingot pulling exists with wafer slicing.
Wafer production shares all the Chinese market-share metrics to ingot pulling, discussed above. From a technology standpoint, there are fundamental differences. On the one hand, wafer slicing is simply to generate wafers from the ingots for cell production. However, there is one technology driver today that elevates the importance of this value chain stage; wafer thickness reduction. And this has just started to get interesting in the past 18 months, after years of stagnation at the 180-200 micron level.
There are two drivers today for continued wafer thickness reduction: decreasing g/W requirements to utilise more of the polysilicon that is in short supply; and optimising thicknesses more amenable to some of the advanced cell concepts such as heterojunction. Profitability playing purely at the ingot/wafer stage is hard to sustain in the PV industry, unless implicitly linked to polysilicon production or as part of an integrated ingot-to-module business model. Ultimately, pure-play ingot/wafer manufacturers get squeezed on cost/price within the value-chain; only economy-of-scale can come to the rescue, and only Zhonghuan today is making the case for this route (although affiliated activities exist for the company in the PV industry most notably with its investments in Maxeon).
Similar to ingot/wafer manufacturing, cell production as a pure-play strategy is very hard to sustain. The most ‘famous’ case study of this was seen during the rise and fall of the Taiwanese solar sector more than a decade ago. Taiwan Stock Exchange listed pure-play cell manufacturers were once the champions of the solar sector, with names such as Gintech, Motech, Neo Solar Power and others rarely off the front pages of the media.
Pure-play cell activity today exists only with a handful of Chinese companies, most however keen to forge upstream (wafers) or downstream (modules) activity as their ultimate sector positioning. That said, cell production is the name of the game when it comes to industry technology changes. To be a technology leader in the PV industry, it is essential to be a top cell producer: but ideally, link this activity to ingot and module vertical integration. All the talk today – and to be covered in the forthcoming webinar – is about the prospects of heterojunction and TOPCon, and nothing matters more here than developments at the cell production stage.
While all the value chain discussion so far has been one of China domination, low-cost and high volume manufacturing, technology differentiation and upstream vertical-integration interplay, module assembly presents an altogether different picture. Module supply is the only part of the value chain today that has a global element to it, largely because the barrier to entry is extremely low and Capex is measured in pennies not pounds: but the key difference is that module suppliers are the ones connected to end-market supply and demand. Let’s look in more detail at module manufacturing now.
Recall that there are about 100 companies today selling modules globally. Most of them make modules, far fewer cells and modules (about 20-30 companies), and even less ingot-to-module (no more than half a dozen). Some simply resell modules made by other companies under their own brand. There are prominent module suppliers in abundance outside China; India, the US, across Europe, South Korea, Taiwan, and in low-volume throughout the Middle East, South America and Canada. Most of the companies outside China rely upon cells produced in China, South Korea or Southeast Asia.
Module assembly is not a part of the value chain that drives technology differentiation. It relies upon changes in technology undertaken by the cell production segment. As such, only the companies in control of cell and module manufacturing have the scope to be technology advocates. Companies that simply assemble cells into modules are beholden to what their cell suppliers decide to produce. Memo to module buyers: check if your shortlisting of potential suppliers actually make their own cells.
However, fiscal analysis of module suppliers is way more important than any other stage in the value chain. This is because final module supply to downstream channels matters more than anything else. Therefore, module suppliers (or upstream integrated companies that are heavily module-revenue-dependent) are scrutinised mainly on operational efficiency and longevity.
Greater than 98% of all module supply comes from 53 companies featuring in the PV ModuleTech Bankability Ratings analysis. Of this grouping, 38 are publicly listed (either as standalone entities, or within larger companies that have a solar module revenue generating business unit); 20 of these are listed in China, with the remainder spread across stock exchanges in Hong Kong, India, South Korea, Taiwan and the US. Of the top 20 module suppliers, only a few are privately-held. Therefore, direct accounting visibility is on show for most of the module supply universe today, albeit with different approaches to assigning cost of operations within reported filings.
Historically, surviving as a company based mainly on net profits selling modules globally has been a tough proposition; consistently falling prices and government incentive seasonality being the key risks. However, recently these factors have become less impactful, driven largely by the huge uptick in demand globally for renewables (including solar) and the diminished importance of justifying PV installations based purely on production-based hand-outs.
Webinar to explain key features in more detail
The purpose of the webinar on 5 April is to hear from leading experts today focused on the various aspects outlined above. The two-hour session will hopefully give all industry stakeholders (from R&D specialists to module buyers, and anyone investing in upstream manufacturing or downstream infrastructure) a broad overview of factors that will shape what the industry will look like over the next 3-5 years.
To register to participate in this free webinar session, please complete your details at the link here. For those unable to attend at the specified time, an option will be provided to listen to a recording afterwards. I look forward to your feedback during and after the event!