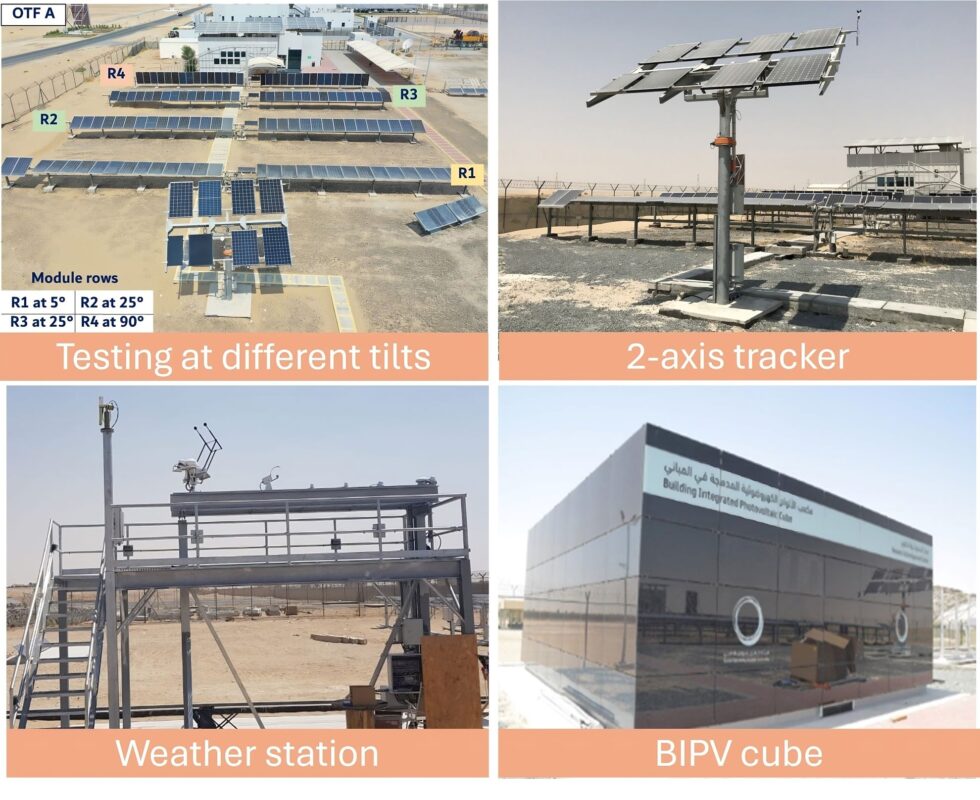
A team of researchers from DEWA R&D Center, Dubai has undertaken a comprehensive review of PV module degradation in desert environments. Their research proposes a new test cycle to identify defects induced in PV modules by harsh desert conditions.
Desert regions are ideal for gigawatt-scale PV module installations because of their large area, abundance of irradiance, high sunshine hours and clear skies. The harsh desert climate, however, tests the dependability and bankability of PV modules. Can current IEC standards dependably assess a PV module’s desert long-term performance? Do the ageing tests used today accurately represent the ways in which modules deteriorate in deserts? Are all modules’ bills of materials (BOM) able to operate dependably in the desert for over 25 years?
Try Premium for just $1
- Full premium access for the first month at only $1
- Converts to an annual rate after 30 days unless cancelled
- Cancel anytime during the trial period
Premium Benefits
- Expert industry analysis and interviews
- Digital access to PV Tech Power journal
- Exclusive event discounts
Or get the full Premium subscription right away
Or continue reading this article for free
The degradation rate of PV modules that have been in use for more than 10 years is higher in hot desert locations, 1.5–2.65% annually, while milder climates show rates of 0.5–1.4% annually [1]. The degradation rate and mechanisms depend on exposure conditions and are directly impacted by different climatic zones worldwide. As a result, the certification criteria for the regional weather should take into account the performance and dependability peculiar to a given geography as an additional measure of improving solar energy performance and reliability.
Therefore, understanding weather conditions, degradation rates and failure modes is important for developing testing standards and designing desert-specific PV modules for long-term operation. The graphical overview shown in Fig. 1 indicates the steps taken to create a roadmap for the development of desert standards for PV modules in desert climates.
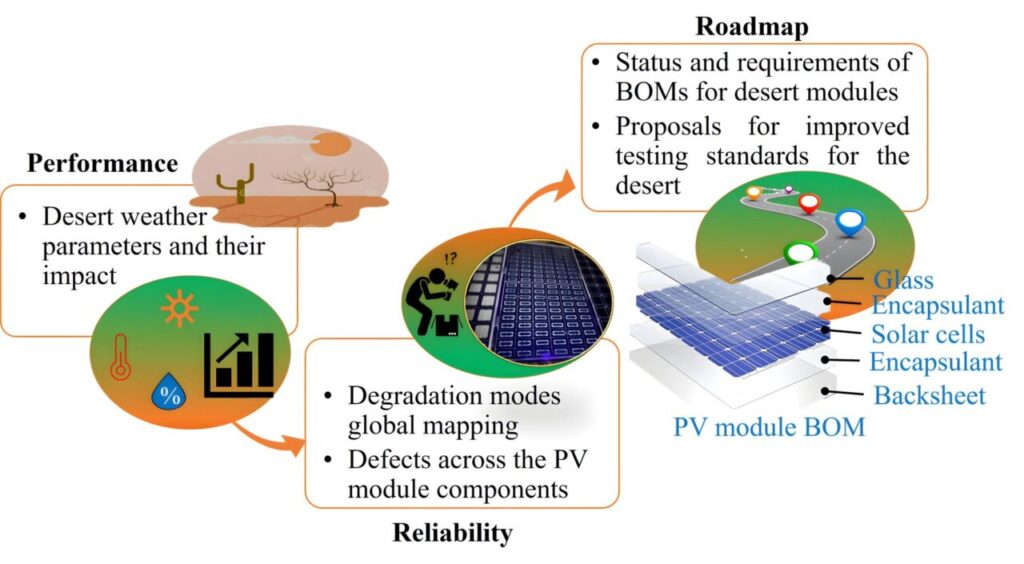
Desert weather parameters and their impact
The reliable performance of PV modules is heavily influenced by the climate conditions in deserts, which include factors such as irradiance, temperature, humidity and dust soiling.
Irradiance is the primary key factor influencing PV module performance, with desert regions exhibiting the highest global horizontal irradiance (2,100–2,700kWh/ m²). This results in an annual power yield of 1,950-2,300kWh/kWp in desert zones, which is over 1.5 times higher than the 1,300– 1,400kWh/kWp yield in moderate climates.
The higher irradiance in desert regions can increase the risk of common light-induced degradations particularly light-induced degradation at elevated temperatures (LeTID) and UV-induced degradation (UV-TID) in c-Si PV modules.
In hot deserts, ambient temperatures typically range from 20°C to 50°C, with maximum module temperatures exceeding 90°C. These large daily temperature fluctuations and high module temperatures are key factors accelerating thermomechanical defects in desert regions.
In contrast to the tropical regions, the relative humidity distribution in the desert climate is moderate (average of 50% RH). A corrosive environment, electrical insulation failure and current leakage in photovoltaic modules are caused by higher humidity levels, which also serve as a source of water vapour ingress.
Soiling can reduce performance by around 1% daily in the soiling-prone zone, especially in the MENA hot deserts. Soiling is a reversible phenomenon that requires adhering to appropriate cleaning testing standards.
Desert degradation modes
The reliable performance of PV modules depends on the prevailing stress factors at a given site, including irradiance, temperature and humidity. The contributions of the degradation rate due to thermomechanical degradation, photodegradation and hydrolysis are largest, moderate and lowest, respectively, in desert regions (Fig. 2).
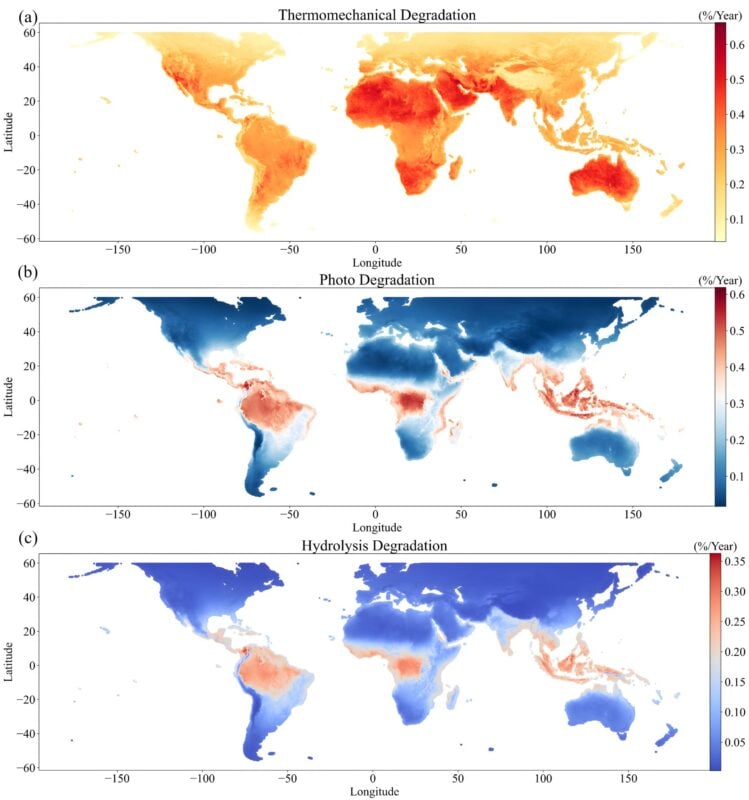
The thermomechanical degradation modes are more pronounced worldwide in the desert than in other zones because of greater swings in both module and ambient temperatures. In contrast, modules installed near water bodies and coastal regions have longer lifespans and exhibit less thermomechanical degradation. Major flaws with desert-operated photovoltaic modules include solder bond failures, busbar/finger breakages and interruptions.
The photo-degradation mode has a major influence on performance degradation because of the greater UV irradiance in the desert. Photodegradation is initiated by UV irradiation and significantly accelerated by temperature and humidity. Encapsulant discolouration, backsheet cracks, chalking and delaminations are found in desert-operated PV modules.
The hydrolysis-degradation mode contribution is quite minor in desert locations due to low air humidity. Solder bonds and fingers corrode more slowly and have a longer lifespan in the desert than in tropical regions.
Hot desert testing standards
Accelerated ageing test standards are used for assessing the degradation modes and predicting the long-term performance of PV modules. Accurately forecasting module lifetimes based on degradation modes and the interaction between BOMs and climatic conditions are of significant interest. However, the existing IEC 61215 and IEC 61730 standards primarily focus on design and safety qualification tests for PV modules under moderate climate conditions. The drawbacks of current standards include:
• Single-stress chambers cannot replicate multi-degradation modes.
• Standard tests do not encompass the evaluation of multiple environmental stressors, new BOMs and new climate-specific failure modes.
• Combined Accelerated Stress Testing (C-AST) and Module Accelerated Sequential Testing (MAST) take several months and are expensive.
• IEC TS 63126:2020 specifies a single-stress approach for qualifying PV modules, components and materials for high-temperature operation.
As discussed in the previous section, desert PV modules often experience defects such as premature encapsulant discolouration, significant thermomechanical damage and glass abrasion.
However, the current IEC 61215 testing standards fail to adequately account for the increased exposure to ultraviolet (UV) radiation, extreme temperature fluctuations and the irregular mechanical stress caused by cleaning robots, common in desert climates. To improve the reliable performance of PV modules in such conditions, a new qualification test cycle, referred to as the “Hot Desert Test Cycle (HDTC)”, should be developed. This test cycle would integrate various desert-specific environmental stress factors to identify defects induced by desert conditions in PV modules and their components. The proposed HDTC is designed to represent the bill of materials and degradation modes specific to desert environments. The proposed stress sequences for HDTC are illustrated in Figure 3.
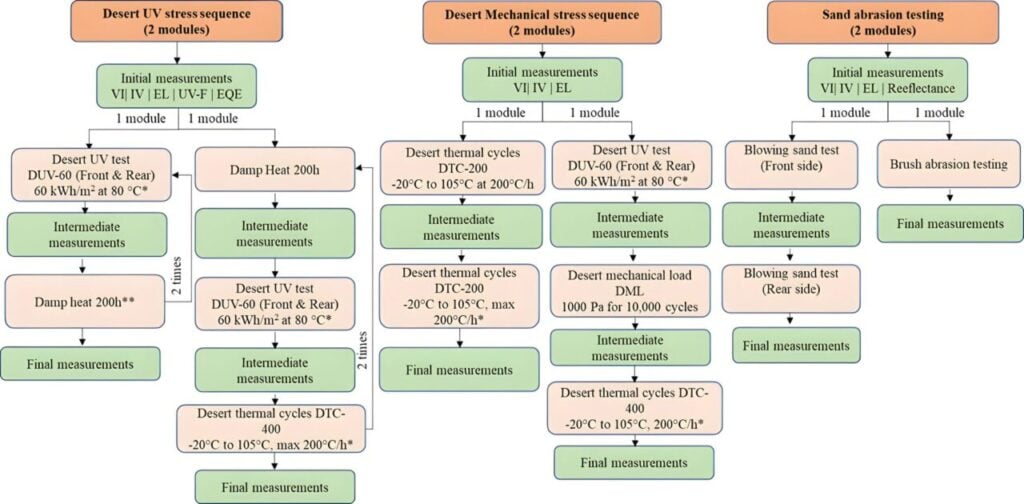
The following is a key conceptual HDTC proposal for testing PV modules in desert climates:
1. Desert UV (DUV) stress sequence: In the desert, due to high UV exposure and module temperature, encapsulant discolouration and backsheet cracks, chalking and delamination are dominant. The first leg replicates the encapsulant discolouration modes and the second leg replicates the backsheet defects such as cracks, chalking, and delamination modes by testing at given UV dose and temperature conditions (Fig. 3).
2. Desert mechanical stress sequence: In deserts, thermomechanical failures in cell components such as busbar/finger breakages, interruption, swellings, ribbon delamination and cell cracks are caused by the large daylight temperature changes and loads caused by cleaning robots. The first leg desert temperature (DTC) represents thermal fatigue failures primarily in PV module cell components.
The second leg replicates combined static mechanical load (caused by a cleaning robot) and thermal fatigue (due to temperature changes in a desert climate) failures in PV module cell components at the given conditions (Fig. 3).
3. Desert sand abrasion test: The constant movement of sand and dust over PV modules is a key factor in studying glass abrasion and the removal of AS and AR coatings in the desert. To simulate moderate to extreme dusty conditions, an enclosed chamber is used with sand and dust movement. The recommended test parameters, based on MIL-STD 810-G standards, include a 1.5-hour test duration, wind speed of 20 m/s, chamber temperature of 60°C, and relative humidity of ≤25%. This abrasion test measures reflectance losses in PV modules.
Additionally, the impact of cleaning brushes on PV modules should follow IEC 62788-7-3 guidelines, with brush strokes at least 14.5 cm long, a speed of 30 cm/s, a rotation rate of 120 rpm, and 10,000 cycles to assess AR/AS coating removal and materials wear and tear.
Requirements of PV BOMs in desert module application
The new desert testing standard focuses on reducing degradation and BOM failure rates. The BOM of PV modules exhibits a variety of problems and is not climate-optimised.
However, there is a lack of clear selection criteria and BOM properties for PV modules designed specifically for desert environments. PV modules should incorporate desert-abrasion-resistant front glazing materials, advanced high-performance solar cells with robust interconnection, desert-durable encapsulants, and reliable backsheet materials [1].
Frontsheet materials: Textured glass (Tempered soda lime or float silicate) or transparent flexible polymer sheets are the most common front glazing materials for PV modules. Thinner glass reduces weight and increases photon transmission from both sides in hot desert settings, maximising bifaciality and enhancing the albedo effect. However, because of the constant movement of sand and dust in desert areas, glass and coatings are more likely to be eroded. The development of anti-reflective (AR) and anti-soiling (AS) coatings has been a major area of research attention in an effort to improve performance and lessen reflection and soiling on the glass surface.
The goal of the research is to develop glass resistant to deserts that includes AR and AS coatings (thickness 100nm, refractive index 1.2 to 1.3) that will increase the average lifespan of PV modules. Uncertainty persists regarding the cleaning and abrasion-related effects of bifacial PV modules in arid environments.
A high optical transmittance is essential for a polymer front sheet. Flexible front sheets are susceptible to thermomechanical degradations and discolouration due to severe UV dosage and extreme temperature fluctuations. Furthermore, because of adhesion, gathered dirt is harder to remove from a polymer front sheet than from glass, which may speed up the process of soiling. The dependability of flexible front sheets in arid areas needs to be investigated, and their UV stability needs to be further enhanced for the use of desert modules.
Solar cell and module technologies: The c-Si PV modules account for 95% of the PV market. Mono-c-Si and n-type PV modules dominate the current PV industry. The market share of four key cell technologies—Passivated Emitter and Rear Cell (PERC), Tunnel Oxide Passivated Contact (TOPCon), Interdigitated Back Contact (IBC), and Heterojunction with Intrinsic Thin layer (HJT)—has been steadily increasing. The following are the required properties of solar cells for desert module applications:
• Low-temperature coefficient: In hotter climates or deserts, solar cells with the lowest temperature coefficient may perform better. Different materials and junctions that are less sensitive to temperature changes and the related changes in Voc and fill factors can be used to develop solar cells with a low-temperature coefficient like HJT, IBC and tandem solar cells (Table 1).

• High efficiency and bifaciality factor: The albedo and irradiance are higher in the desert. To attain the high bifacility factor, it should be able to collect more photons from both directions. HJT and TOPCon are highly efficient bifacial cells (Table 1) that can be an option for designing desert PV modules.
• Solar cells must be resistant to desert UV radiations; otherwise, the passivation layer may be damaged by the intense UV radiation. The performance of the PV module may be lowered as a result of UV-induced deterioration (UVLID) in the desert. The IBC module shows improved stability compared to PERC, TOPCon and HJT modules [2,3].
• LeTID may occur in desert climates where module temperatures can surpass 60°C. The LeTID effect should be taken into account when designing PV modules for desert environments, especially for new-generation PERC, TOPCON, IBC and HJT modules.
• The impact of albedo should be evaluated at both broadband and spectral levels. A higher broadband albedo will improve the performance of PV modules by increasing the rear-side irradiance.
Similarly, spectral albedo should align with the rear-side response (EQE_rear) of solar cells to maximise spectral utilisation. Variations exist between c-Si solar cells in terms of spectral and broadband albedo. To maximise PV performance in desert climates, cells or modules with high broadband and spectral albedo are essential.
• The use of appropriate connecting technology is critical to minimising shading losses, thermomechanical flaws and soldering effects. For long-term operation in a desert climate, characteristics including increased ductility, electrical bridging between contacts, self-healing flaws and regaining electrical continuity are all advantageous. It is necessary to look into the suitability of integrated back contact, electrically conductive adhesive, and smart wire soldering interconnection technologies for use in desert climates.
Encapsulant materials: Encapsulant materials are crucial for ensuring the long-term stability of PV modules. PV encapsulants are generally divided into two categories: crosslinking and non-crosslinking. Crosslinking encapsulants include ethylene-vinyl acetate (EVA) copolymer, polyolefin elastomer (POE), and silicone, while non-crosslinking encapsulants consist of thermoplastic polyolefin (TPO), ionomers, and polyvinyl butyral (PVB).
EVA remains the industry standard, with polyolefins (POE, TPO) emerging as promising alternatives to EVA in the PV industry. The properties of EVA and polyolefin are shown in Table 2. Furthermore, the following properties should be considered for selecting the desert module encapsulants and related BOM:
• High optical transmittance (greater than 90%) to increase photocurrent,
• High melting point (over 90 °C) to improve thermal stability and decrease creep and adhesion loss,
• Low glass transition temperature to prevent brittle failure and to improve flexibility,
• High UV stability to prevent delamination and discolouration,
• Low rate of water vapour transportation (less than 3g/m2 per day) to prevent corrosive environments and insulation failure,
• High volume resistivity (greater than 1016 Ωcm) to reduce current leakage and possible potential induced degradation,
• Zero acid/vinyl acetate groups encapsulant to prevent the deacetylation mechanism,
• Low crosslinking materials, such as POE, and non-crosslinking materials like TPO, to reduce lamination time and improve recyclability.
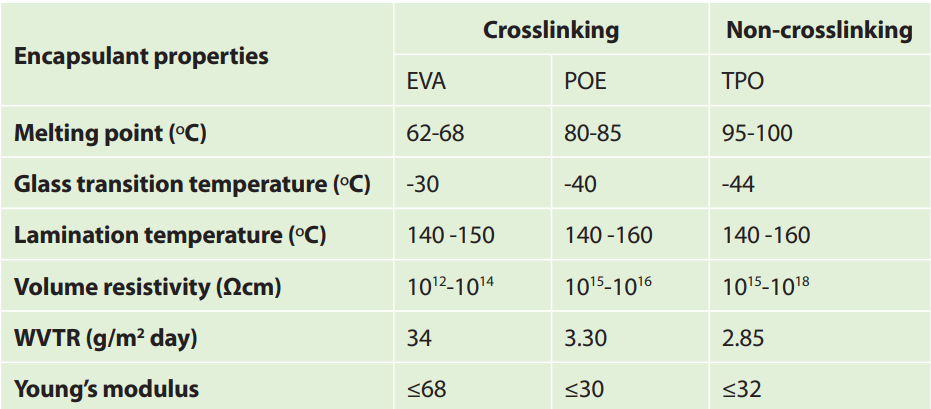
Backsheet materials: Multi-layered polymeric composite films are widely used for PV module backsheets. The inner layer (cell side) should offer strong adhesion and UV protection for the core layer, while the core layer provides electrical insulation and mechanical stability. The outer layer (air side) must shield the module from UV radiation and other environmental stresses. When designing PV modules for desert applications, the following properties should be considered:
• High UV stability to prevent cracking and delamination.
• Free of metastable morphology or blended compositions to minimise shrinkage, embrittlement, and cracking.
• High acetic acid transmission rates (AATR above 0.5-1g/m² per day) to reduce acid corrosion in components and mitigate potential-induced degradation (PID).
• Low water vapour transmission rates (below 4g/m² per day) to reduce insulation and delamination failures.
• Co-extruded backsheets resolve issues like delamination and cracks seen in laminated backsheets (e.g., polyamide or fluorine-based films).
• High thermal stability (180°C) to avoid softening and deformations.
The combination of the above BOM (glass, a solar cell with interconnection technology, encapsulant and backsheet) properties, and their reliable outdoor performance should be considered while designing the PV module specific for desert climates called Desert PV modules. These recommendations provide a basis for further research into climate-specific standards and PV module designs for desert applications.
Conclusions
The growing rate of installation of PV modules in desert climates raises concerns about bankability and reliability due to the harsh environmental conditions. Performance loss and degradation in deserts differ significantly from moderate climates, with common failure modes including encapsulant discolouration, interconnect breakages, backsheet cracks, chalking and glass abrasion (ARC removal). However, current IEC 61215 testing standards do not adequately address these issues. To promote reliable PV module performance in desert conditions, a new qualification test cycle, the “Hot Desert Test Cycle (HDTC)”, should be developed.
HDTC would involve multiple tests targeting problems such as encapsulant discolouration, backsheet cracks/delamination, thermal fatigue, mechanical stability and glass abrasion caused by desert conditions. To mitigate degradation and failure rates in deserts, PV modules should incorporate desert-resistant glazing materials, advanced high-performance solar cells with robust metallisation, durable encapsulants, and reliable backsheet materials. These recommendations serve as a foundation for further research into desert-specific testing standards and PV module designs.
References
[1] Adothu, B. et al., 2024, “Comprehensive review on performance, reliability, and roadmap of c-Si PV modules in desert climates: A proposal for improved testing standard”. Progress in Photovoltaics: Research and Applications 32, 495–527.
[2] Jeff Kettle et al., 2022, “Review of technology-specific degradation in crystalline silicon”. Progress in Photovoltaics: Research and Applications. 30, 1365–1392.
[3] Sinha, A. et al., 2023, “UV-induced degradation of high-efficiency silicon PV modules with different cell architectures”. Progress in Photovoltaics: Research and Applications 31, 36–51.
Authors
Dr. Baloji Adothu has been a principal researcher at Dubai Electricity and Water Authority (DEWA) R&D Center since 2021, focusing on the development of desert PV modules, bill of materials, local and safety standards development, and the establishment of outdoor and robotic cleaning test fields (OTF & CTF) for PV module performance and data analysis. He has a PhD in the field of development and reliability testing of PV modules from the Materials Science department, IIT Bombay, India.
Dr. Bengt Jaeckel has been active in the PV industry since 2007 and currently leads the modules, components and manufacturing group at the Fraunhofer Center for Silicon Photovoltaics (CSP). His work focuses on the reliability of PV modules and systems. He holds his PhD in materials science from Darmstadt University of Technology. He represents Germany in the module group at DKE and also serves as the German representative for IEC TC 82 and CENELEC TC 82 at the international level.
Dr Gerhard Mathiak has worked as head of PV performance and reliability testing at DEWA R&D Center in Dubai since 2021, following several jobs in PV manufacturing and testing. He has worked on the operation of PV modules and cleaning robots in the harsh conditions of hot deserts. He is also active in several PV standards committees.
Dr Vivian Alberts has been the senior research manager of the solar department at the DEWA R&D Center since 2021. He leads efforts in perovskite tandem and desert PV module development. With a PhD in Physics and over 25 years of experience in semiconductor science, he specialises in the design and development of c-Si and thin-film PV modules.
Dr Sgouris Sgouridis has been the director of research programmes at the DEWA R&D Center since 2019. He was an associate professor of engineering systems at Masdar Institute, head of the Institute Centre for Smart and Sustainable Systems, and review committee chair of the Zayed Future Energy Prize (ZFEP). He holds a PhD in technology management and policy.
Eng. Ahmed Alheloo has been working as an R&D technologist at DEWA R&D Center since 2019. His research interests focus on renewable energy technologies, including photovoltaics, wind and hydropower systems, as well as certifications and standards related to these fields.
Eng. Ali Almheiri has worked as an R&D technologist at DEWA R&D Center since 2019. His research interests are centred on solar energy technologies, with a particular focus on PV module reliability, the impact of arid desert conditions on solar energy systems, experimental design and the development of solar standards.