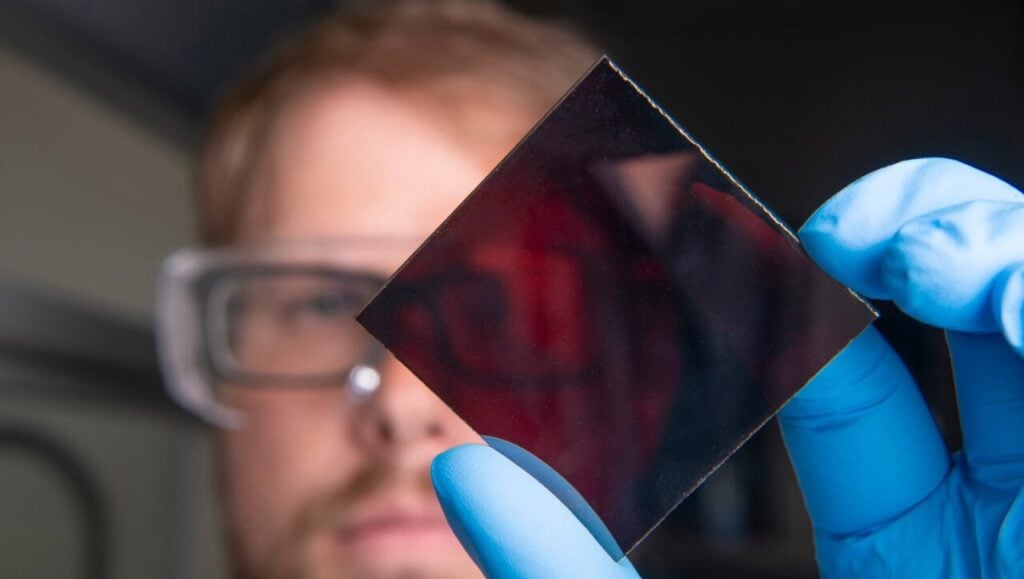
Although perovskite-based technologies offer the promise of high efficiencies and low costs, the route to their commercialisation is far from straightforward. Brian Grenko of VDE Americas assesses the route to market for perovskite PV products and their readiness as an alternative to silicon-based technologies.
The rise of solar power as a safe, reliable and low-cost energy source is made possible by PV module manufacturers achieving economies of scale while steadily improving device conversion efficiencies. To remain competitive in this enduring technological arms race, manufacturers continually chase maximum power output bragging rights.
Unlock unlimited access for 12 whole months of distinctive global analysis
Photovoltaics International is now included.
- Regular insight and analysis of the industry’s biggest developments
- In-depth interviews with the industry’s leading figures
- Unlimited digital access to the PV Tech Power journal catalogue
- Unlimited digital access to the Photovoltaics International journal catalogue
- Access to more than 1,000 technical papers
- Discounts on Solar Media’s portfolio of events, in-person and virtual
This process led manufacturers to adopt passivated emitter rear contact (PERC) crystalline silicon (c-Si) solar cells approximately 10 years ago and motivated the transition to tunnel oxide passivated contact (TOPCon) cells now underway. Despite these power conversion efficiency improvements, the levelised cost of solar energy is approaching an asymptotical limit. PV module suppliers are quickly converging on the theoretical limit for 2-terminal c-Si solar cell conversion efficiency, leading researchers to more aggressively pursue tandem solar cell architectures.
Metal halide perovskite materials have quickly demonstrated a potentially viable pathway to manufacturing ultra-low-cost, high-efficiency PV modules at scale. And perovskite PV research findings have undoubtedly generated a lot of hype. For example, the MIT Technology Review included perovskite solar cells on its Top 10 list of breakthrough technologies for 2024, estimating the time horizon for commercialisation to be on the order of three to five years [1].
Although it is difficult to predict precisely how perovskite-based PV technology development will play out over time, we do know with certainty that bankability is prerequisite to wide-scale commercial deployment. With that in mind, this article seeks to provide a high-level overview of the current state of play regarding perovskite PV product development, specifically evaluating technological readiness within a financial risk assessment framework. But first, we’ll briefly summarise the science underlying perovskites and consider how we first arrived at the incumbent PV cell technologies that currently dominate the market.
About perovskites
In 1893, German mineralogist Gustav Rose discovered calcium titanate in the Ural Mountains of Eurasia and named the mineral in honour of Russian nobleman and fellow minerologist Lev Perovski. Naturally occurring perovskite is semiconductive and inherently capable of absorbing light and generating the photovoltaic effect. Today, the term “perovskites” is used to describe a broader family of compounds having a similar crystalline structure and “ABX3” chemical formulation, where A and B represent divalent and tetravalent cations, respectively, and X is an anion that bonds to both. This broad family of materials includes both octahedral metal-oxide and metal-halide structures surrounded by organic or inorganic cations.
Synthetic perovskites offer excellent compositional flexibility, meaning it is possible to combine many different atoms and molecules into perovskite compounds. Researchers have shown that metal-halide perovskites have exceptional optoelectronic properties, potentially making them suitable for low-cost semiconductor applications. These characteristic advantages have made perovskites an exciting scientific field of exploration and appear to provide various pathways for product commercialisation.
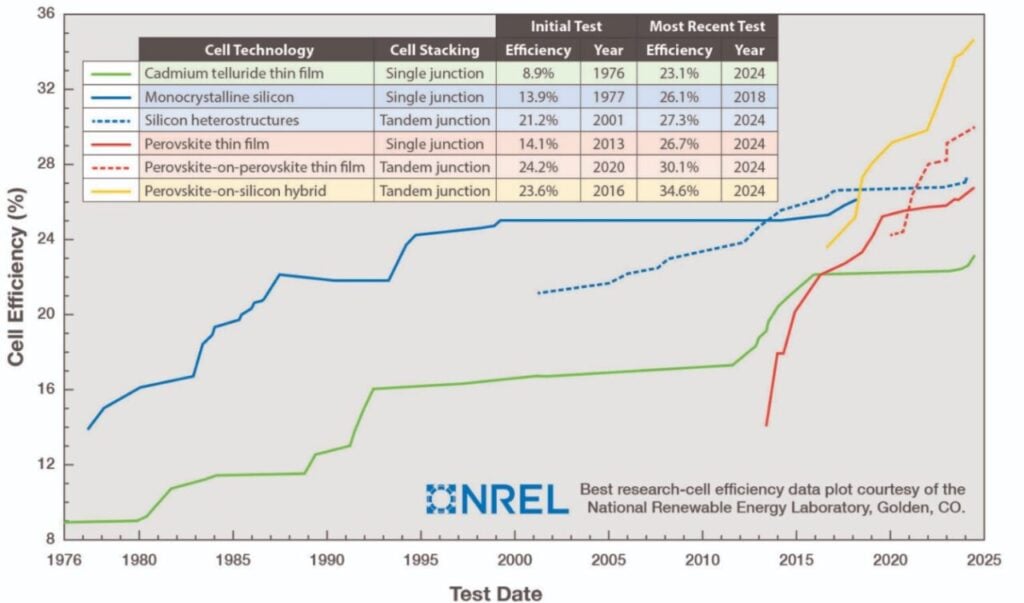
In 2009, the first-ever perovskite solar cell, invented by Professor Riki Miyasaka at Toin University of Yokohama, achieved a conversion efficiency of about 3%. Just 15 years later, the best perovskite cell efficiencies now exceed those for traditional monocrystalline silicon and cadmium telluride thin-film technologies. The learning curve for perovskites is unprecedented, as shown in Figure 1, above.
Thousands of researchers are currently working at colleges, universities, research institutes, established PV suppliers and newly minted companies to accelerate the development of perovskite PV. Though technological advancement remains a work in progress, research in this field is not merely an academic pursuit or the speculative domain of startups. The list of companies making significant investments and contributions in perovskite PV includes leading manufacturers such as First Solar, Jinko Solar, LONGi, and Qcells.
Silicon hegemony
In 1954, Bell Laboratories unveiled its “solar battery”, which many historians recognise as the first practical silicon semiconductor-based solar cell. One year later, Hoffman Electronics released a 14 milliwatt-rated commercial silicon solar cell with a conversion efficiency of 2%, which retailed for more than US$20,000 per watt (adjusted for inflation). Fast forward 70 years, and commercially available c-Si PV modules are roughly 900% more efficient than those products initially sold in 1955 and have decreased in cost by an astounding 99.999%.
Thanks to advances in cell technologies, manufacturing capabilities and efficiencies of scale, silicon-based solar cell technologies now account for roughly 95% of a global solar energy market valued at more than US$250 billion.
While the market has changed profoundly in recent decades, today’s c-Si PV modules still share much in common with those produced in the early days of solar energy. Under the auspices of a US-government sponsored programme that ran from 1975 to 1986, NASA’s Jet Propulsion Laboratory (JPL) pioneered the development of early commercial terrestrial solar PV module designs. In fundamental ways, we can trace the design principles of today’s PV modules—from glass, encapsulant and frame packaging to laboratory testing sequences—to JPL’s ground-breaking Flat-Plate Solar Array Project.
It would, of course, be a mistake to confuse persistence and staying power with a lack of progress. Advances in solar cell design, manufacturing equipment and process controls have been foundational to the many technological achievements that have enabled PV module companies to continually improve conversion efficiencies and reduce the levelised cost of solar energy.
Only a decade ago, the aluminium back surface field (Al-BSF) c-Si solar cell was the predominant industry cell design. As the Al-BSF architecture was approaching its conversion efficiency limit and the market exhibited signs of PV module oversupply, leading manufacturers began adopting PERC and similar cell design variants to differentiate themselves. Companies that failed to quickly adapt struggled to survive the ensuing market downturn.
Today, many of those same players have begun pivoting from PERC to TOPCon, which is projected to be the leading cell technology by market share in 2024. To remain competitive on a global stage, PV module manufacturers must continually drive down their cost of goods sold, which is most easily achieved through increases in conversion efficiency. Complicating this race for survival is the fact that our industry is approaching the physical limitations of single-junction c-Si solar cells.
Taking it to the limit
In their seminal 1961 research paper, William Shockley and Hans Quiesser famously posited that the upper theoretical efficiency limit for a single p-n junction solar cell was 30% [2]. By accounting for solar spectrum measurements and material-specific bandgap values, subsequent scientific work has produced slightly more refined maximum efficiency estimates. Nevertheless, the original Shockley-Queisser efficiency limit still holds true as a rough-order-of-magnitude estimate.
Some researchers and analysts consider heterojunction technology (HJT) solar cells to be the next logical evolutionary step on the commercial c-Si PV cell roadmap. HJT cells feature a single junction formed with two or more semiconductor layers or regions with complementary band gaps to improve charge carrier separation.
As early as 2006, Sanyo released commercial modules featuring its heterojunction with intrinsic thin layer (HIT) cells, comprised of n-type monocrystalline bulk silicon sandwiched between layers of amorphous silicon. The aggregate device captures a relatively greater portion of the solar light spectrum, increasing efficiency while also improving thermal properties related to heat dissipation and temperature coefficients.
In commercialised c-Si PV applications, HJT solar cells remain the industry benchmark for conversion efficiency utilising a single p-n junction. But what if it were possible to build on the success of silicon heterostructures using other thin-film materials? Perovskites, for example, have superior light absorption properties that can be tuned to complement the spectral response of silicon, resulting in a much more efficient device.
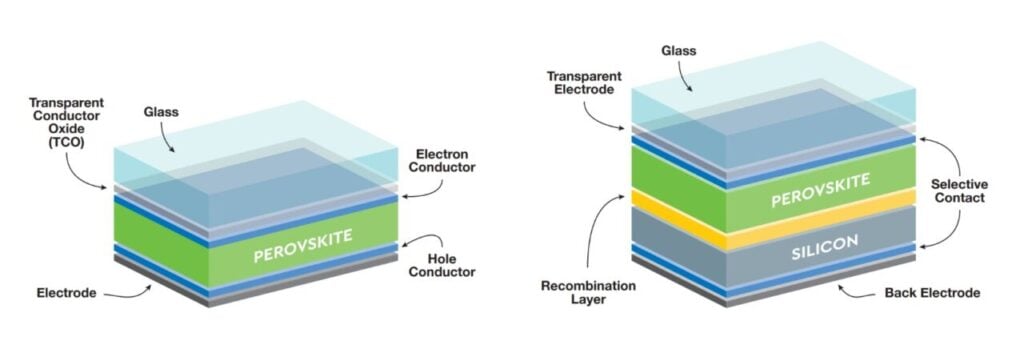
This line of inquiry is precisely what has motivated global efforts to develop low-cost tandem solar cell technologies by stacking multiple p-n junctions. One of the most promising avenues of research seeks to combine a perovskite solar cell with silicon heterojunctions, as shown in Figure 2, above.
In May 2024, LONGi announced that it had produced a perovskite-on-silicon tandem research cell with a then-record efficiency of 34.6%. In other words, one of the most bankable solar companies in the world just crushed the Shockley-Quiesser efficiency limit for an ideal single-junction PV device using a novel hybrid tandem-junction solar cell stacking perovskite thin film atop crystalline silicon. Some might argue that breaking a single-junction limit with a tandem-junction device is a bit like bringing a gun to a knife fight. But students of history know that groundbreaking technology advancements win arms races.
Proof of concept
In the context of high-volume manufacturing, the commercialisation of novel PV technologies is invariably more of a marathon than a sprint. After all, technology development timelines for novel cell technologies often span years or even decades prior to mass-market adoption. Although perovskites represent a fundamentally new optoelectronic device class, the general path to market for perovskite-based PV modules could parallel that of previous silicon-based cell technologies.
Consider PERC cell technology commercialisation, as an example. In 1983, an Australian research team at the University of New South Wales, led by Martin Green, invented the PERC structure. By 1989, when the team published its first paper on PERC technology, the researchers had increased cell efficiencies from 18% to 22.8% [3]. Despite this record-setting performance, PV cell manufacturers did not begin to transition to PERC production until 2013, in part due to technology limitations of high-volume vapour deposition processes.
In other words, it took solar industry stakeholders roughly 30 years to develop the scientific knowledge, manufacturing processes and supply chain required to facilitate the commercialisation of low-cost, high reliability PERC c-Si PV modules. Perovskites, however, could benefit from an accelerated go-to-market timeline.
“Anyone working in perovskites today stands on the shoulders of giants,” explains Colin Bailie, founder and chief technology officer at Tandem PV, a Silicon Valley-based perovskite solar startup. “Twenty or 30 years ago, companies had to invent a lot of new technology just to figure out how to deposit thin semiconductor layers as part of a high-volume serial production process. Today, those advances pioneered by First Solar or flat-screen TV manufacturers or required for PERC and heterojunction cell production—are simply part of the world we live in.
“Since we can take advantage of what are now off-the-shelf technologies, the process of improving the performance and durability of perovskites as a PV cell technology is a much lower lift than it might have been previously. Working on analogous technologies and applications, researchers and manufacturers have already figured out solutions to many perovskite commercialisation challenges. That’s why so many Tier 1 module companies have perovskite-based tandem PV modules on their technology roadmap.”
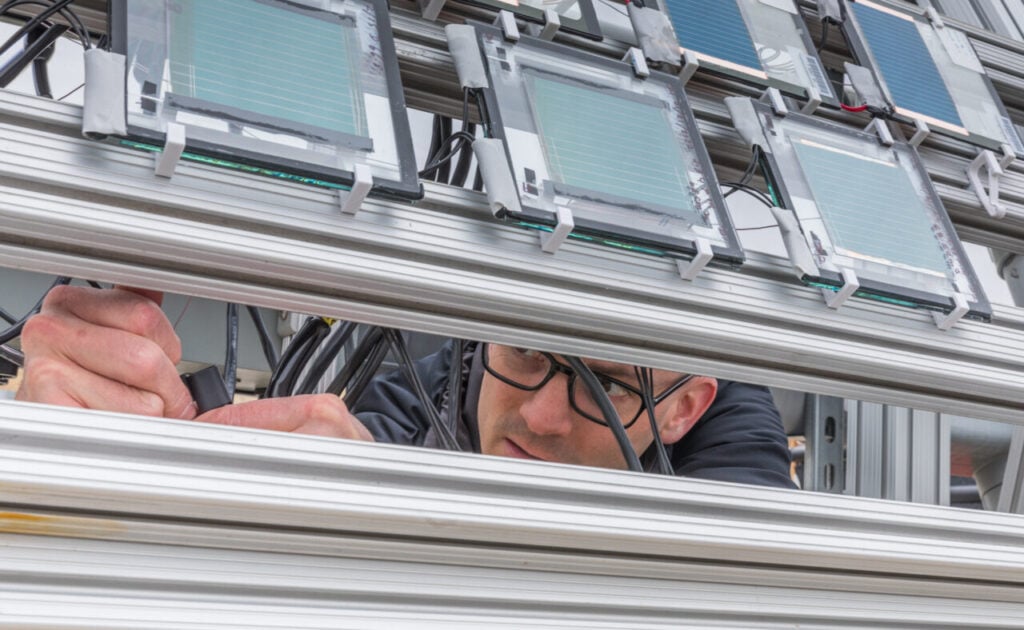
Collectively, PV module manufacturers are already making progress scaling perovskite-based technologies from laboratory-scale “minimodules”, like those in Figure 3, above, to small- and standard-area solar panels. In China, multiple companies claim to have already fielded demonstration projects with perovskite PV. A 1MW-rated ground-mount project announced in December 2023 and owned by Three Gorges Energy reportedly integrates 11,200 small-area perovskite thin film PV modules.
In September 2024, UK-based startup Oxford PV announced its first commercial shipment of tandem perovskite-on-silicon PV modules from a manufacturing facility near Berlin to an undisclosed utility-scale solar project in the United States [4]. Though public details are scant, some speculate that the demonstration project is on the order of hundreds of kilowatts. If true, this pilot may represent the first deployment of standard-area perovskite-based solar modules at scale.
Long-term performance
From a bankability perspective, the marathon that matters most to solar project investors, lenders and insurers generally starts on the project’s commercial operation date, which is the day when the asset becomes fully operational generating power and earning revenue. To meet financial expectations, fielded PV modules must withstand environmental stressors and often harsh operating conditions while meeting or exceeding performance predictions over the planned economic useful life of the project, which is typically on the order of 30 to 40 years.
Like other thin films, perovskite materials are known to be highly susceptible to chemical decomposition when exposed to moisture, due to their ionic structure. Additionally, perovskite solar cells are highly sensitive to temperature and prone to voltage-induced degradation mechanisms. Consequently, a lack of long-term field data is one of the biggest bankability hurdles for manufacturers working to commercialise perovskite-based PV modules.
“There is a commercial aspect to new technology that can make it difficult to integrate,” says Benjamin Lemkau, senior director of solar PV systems technology for RWE. “It’s one thing to have a better, more efficient cell technology. Convincing people to buy it is another thing. Stakeholders sitting on the other side of the table from us are often very conservative. It’s hard to sell a utility on a 25- or 30-year power purchase agreement using a technology with a limited time in the field.”
The investment community that provides construction loans or tax equity financing for early-stage solar project development is similarly conservative. These stakeholders evaluate investments opportunities according to a financial pro forma, which models energy production and cash flows over time. Open questions or concerns about product stability, durability, or reliability are typically reflected in the form of higher uncertainties in energy yield assessments, which may increase borrowing costs or weed out potential investors.
PV module lifetime is often considered as the length of time it takes for performance to degrade by 20%. The threshold is likely related to the fact that virtually all PV module manufacturers currently provide a performance guarantee that warrants minimum power output on a yearly basis for up to 35 years, typically down to about 80% of its original nameplate power rating. While all PV modules degrade over time—due to environmental exposure, material defects, mechanical stresses, or other causes—the expected rate of degradation is better understood for more established and deployed solar cell technologies.
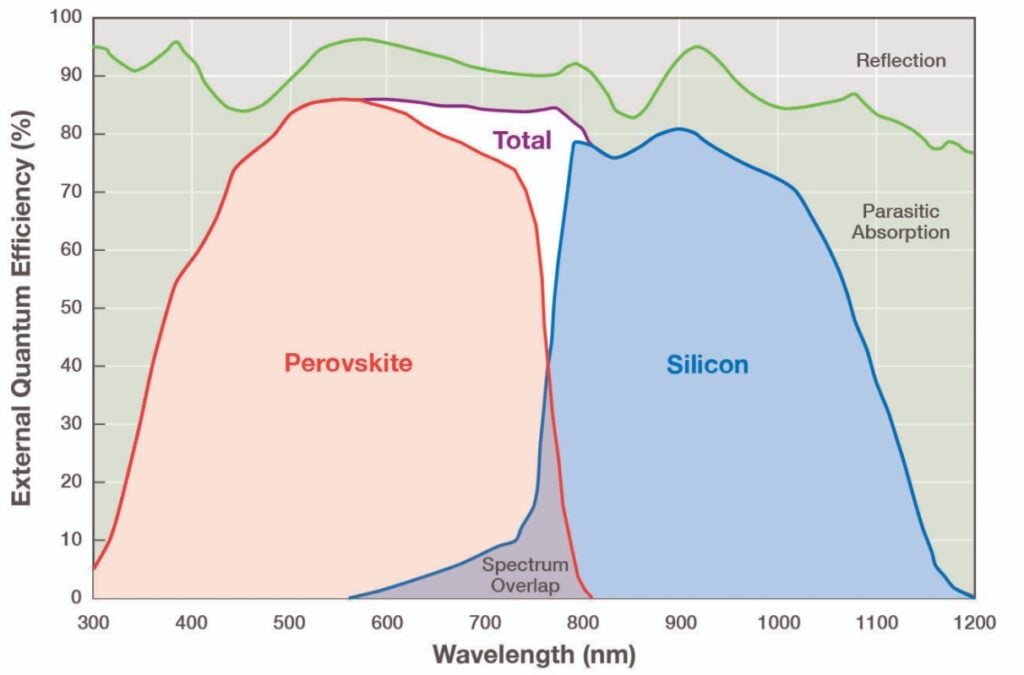
Due to the nascency of perovskite PV development—not to mention the many variations of perovskite compounds and associated materials currently under evaluation— technology-specific degradation rates are not yet well understood. Manufacturers largely remain focused on developing or optimising their formulations. However, accurately characterising perovskite degradation rates is a high priority for the U.S. Department of Energy-funded team at the Photovoltaic Accelerator for Commercialising Technologies (PACT) centre.
“To even begin to assess the lifetime of perovskite PV technologies, we likely need at least two years of field performance data,” explains Laura Schelhas, a deputy director of PACT, which is collaboratively operated by the National Renewable Energy Laboratory and Sandia National Laboratories. “This is especially true for perovskites, which are subject to seasonal performance variations due to metastability. Calculating a long-term degradation rate requires separating long-term trends from seasonal variance. My best estimate is that this requires at least two years’ worth of time-series data as an absolute bare minimum.”
Although the technical due diligence community is rightly concerned that novel solar cell technologies may behave or degrade in novel ways, manufacturers have demonstrated a remarkable ability to solve complex problems at the nexus of material science and high-volume manufacturing.
Light- and elevated temperature-induced degradation (LeTID), for example, is a field degradation phenomenon that was shown to affect boron-doped p-type PERC cells in hot climates. This degradation mode was observed after developers began integrating PERC modules in fielded projects. Today, with tighter manufacturing process controls and the use of gallium as a doping agent in bulk silicon, the performance risk associated with LeTID is negligible.
The process of de-risking the adoption of next-generation perovskite technologies is likely to follow a similar template. In other words, industry stakeholders can improve investor confidence over time by continually identifying novel field degradation mechanisms, adapting laboratory test sequences to expose these vulnerabilities and enhancing technology-specific production modelling software capabilities.
Metastability effects
While many agree that demonstrating reliability and durability at the PV module level is the crucial next step on the path to market adoption for perovskite materials, another significant challenge lurks around the corner. As mentioned by Schelhas, perovskites are metastable, meaning that their electrical behaviour is subject to hysteresis effects. In other words, the power output of perovskite PV at any given time depends not only on instantaneous irradiance and temperature conditions, but also on previous conditions and recent device performance.
One of the more interesting phenomena researchers evaluating perovskite PV field performance have observed is a light-soaking effect in which diurnal voltage degradation during nighttime hours recovers upon illumination. This recovery process can take minutes to hours, depending on the material formulation and potentially the age of the device [5]. Based on these findings, we could theorise that improvements in perovskite PV performance over the course of a day may to some extent offset temperature-related performance losses in summer months when days are longer.
These hysteresis effects make factory flash-testing and PV module binning more challenging. Moreover, these effects present a major headache for those modelling PV module performance and conducting energy yield assessments. Today’s modelling software simply does not consider metastability influences on performance, introducing additional uncertainty when estimating electrical production. Further complicating this dilemma is the fact that different perovskite compounds appear to have significantly different metastability and burn-in traits [6].
The variation of materials currently under evaluation and the embryonic state of perovskite solar cell development complicates due diligence efforts and progress toward commercialisation. Our industry is simply not ready to engage in a productive discussion about adapting and standardising performance characterisation testing sequences and procedures for perovskite PV modules.
Shape of things to come
If you work deploying commercialised solar products at scale, as I do, the constant buzz around perovskite-based PV technologies can start to feel like background noise. After all, many emerging solar technologies have failed to cross the startup valley of death, the chasm of technological and financial challenges that separate the one-off hero cell produced in a laboratory from a commercially viable mass produced large-area PV module. While the bankability hurdle is high, I do believe perovskites could rise to the occasion and play a meaningful role in the global energy transition.
Having said that, I am also keenly aware that the path forward is not an equitable one. In the context of an oversupplied and hyper-competitive global market, a perovskite PV technology or business model will not succeed or fail on technical merits alone. Winning an arms race requires funding, whether in the form of government subsidies, venture capital investment or legacy product cash flows. Access to capital will give some perovskite PV companies inherent structural advantages over others.
As part of a holistic bankability assessment, technical advisors like me typically review third-party product test data, factory inspection reports and manufacturing audits. Additionally, we evaluate a company’s financial strength, global manufacturing capacity, deployed fleet and fielded product reliability and ability to honour warranty claims in the event of a serial defect. Large, established companies will naturally have an easier time than start-ups clearing the bar in this type of technology review process.
The latest PV ModuleTech Bankability report from PV Tech Power publisher Solar Media’s market research arm indicates that the six top Chinese PV module companies—specifically, Canadian Solar, JA Solar, JinkoSolar, LONGi, Tongwei, and Trina Solar—control roughly 60% of the global solar market and are particularly well positioned financially in terms of liquidity and debt ratios [7]. If one of these companies released a commercial tandem perovskite-on-silicon PV module tomorrow, that product would arguably meet some minimum threshold for bankability based on the criteria discussed above. In effect, the company’s financial strength and installation history would to some extent assuage technology risk concerns.
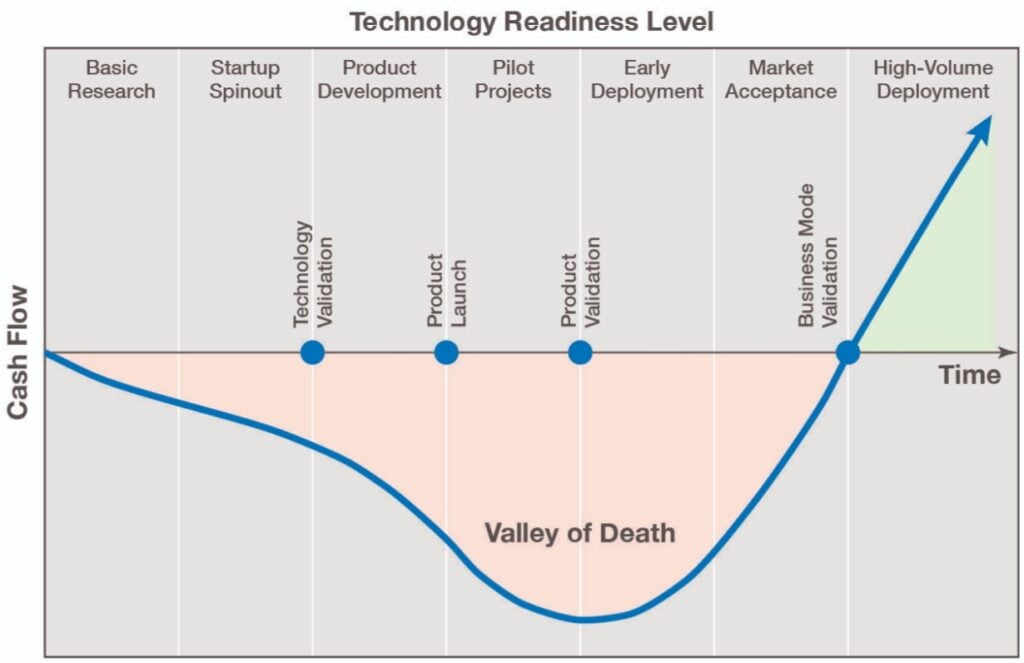
Barriers to bankability are inherently higher for early-stage companies. By many accounts, capital investment has slowed in the past two years given macroeconomic headwinds and geopolitical uncertainty. Some climate tech investors no longer see solar as the bright shiny object it once was and are instead looking to invest in emerging technologies such as super-small nuclear reactors or carbon capture and storage. This cautious view may overlook the disruptive market potential of perovskites in the terawatt era of PV.
The promise of a more streamlined supply chain is part of what makes perovskites compelling as a next generation solar technology. To produce conventional silicon PV modules, raw silica must be purified at high temperatures in an arc furnace to produce polysilicon. This purified material is then shipped long distances and remelted to form ingots, which are subsequently sliced into wafers. In many cases, wafers are then shipped to yet another manufacturing facility for conversion into solar cells prior to PV module assembly.
In contrast to this energy-intensive, logistically complex manufacturing process, imagine a perovskite PV module manufacturing process where raw materials enter one end of a factory and finished products exit the other. Perovskite thin films are suitable for either solution-based fabrication approaches or vacuum deposition on a rigid base, such as flat glass or a polysilicon wafer. Perovskite PV fabrication at scale could one day even resemble newspaper printing, with affordable ink-like coatings applied to a flexible substrate in a roll-to-roll process.
Hype and hope walk hand in hand with perovskites for good reason. Perovskite PV has a viable path to market in the mid-term as a complement to single-crystal silicon in hybrid tandem PV cells. Beyond extending the technology roadmap for incumbent solar companies and cell technologies, low-cost single- or tandem-junction perovskite thin-film PV products could also eventually provide a roadmap beyond silicon, potentially disrupting the solar market as we know it today.
References
[1] Merchant, E. F., 2024, “Super-efficient solar cells: 10 Breakthrough Technologies 2024,” MIT Technology Review.
[2] Shockley, W. and Queisser, H.J., 1961, “Detailed Balance Limit of Efficiency of p-n Junction Solar Cells,” Journal of Applied Physics, Vol. 32, No. 3, pp. 510–519.
[3] Green, M. A., 2015, “The Passivated Emitter and Rear Cell (PERC): From conception to mass production,” Vol. 143, pp. 190–197.
[4] Norman, W, “Oxford PV ships first commercial perovskite tandem modules,” PV Tech, September 5, 2024.
[5] Renec, M., et al, 2024, “From Sunrise to Sunset: Unraveling Metastability in Perovskite Solar Cells by Coupled Outdoor Testing and Energy Yield Modelling,” Advanced Energy Materials, Issue 29.
[6] Le, T.-H., et al, 2023, “Perovskite Solar Module: Promise and Challenges in Efficiency, Meta-Stability, and Operational Lifetime,’ Advanced Electronic Materials,” Vol. 9, Issue 10.
[7] Colville, F., “Tsunami of Chinese solar company insolvencies in 2025 revealed in latest PV Tech Bankability Report,” PV Tech, October 31, 2024.
Author
Brian Grenko has over two decades of renewable energy industry engineering and operations experience. As the head of technical advisory services for VDE Americas—a wholly owned subsidiary of one of the largest technology organisations in Europe—Brian works to advance the deployment of large-scale solar and energy storage projects that are financeable and insurable. Previously, he served in executive, due diligence and manufacturing quality management roles at Amplify Energy, Yingli Green Energy Americas, GE Energy and AstroPower. Brian is Lean Sigma Black Belt certified and holds a Bachelor of Science degree in Civil and Environmental Engineering from Pennsylvania State University.