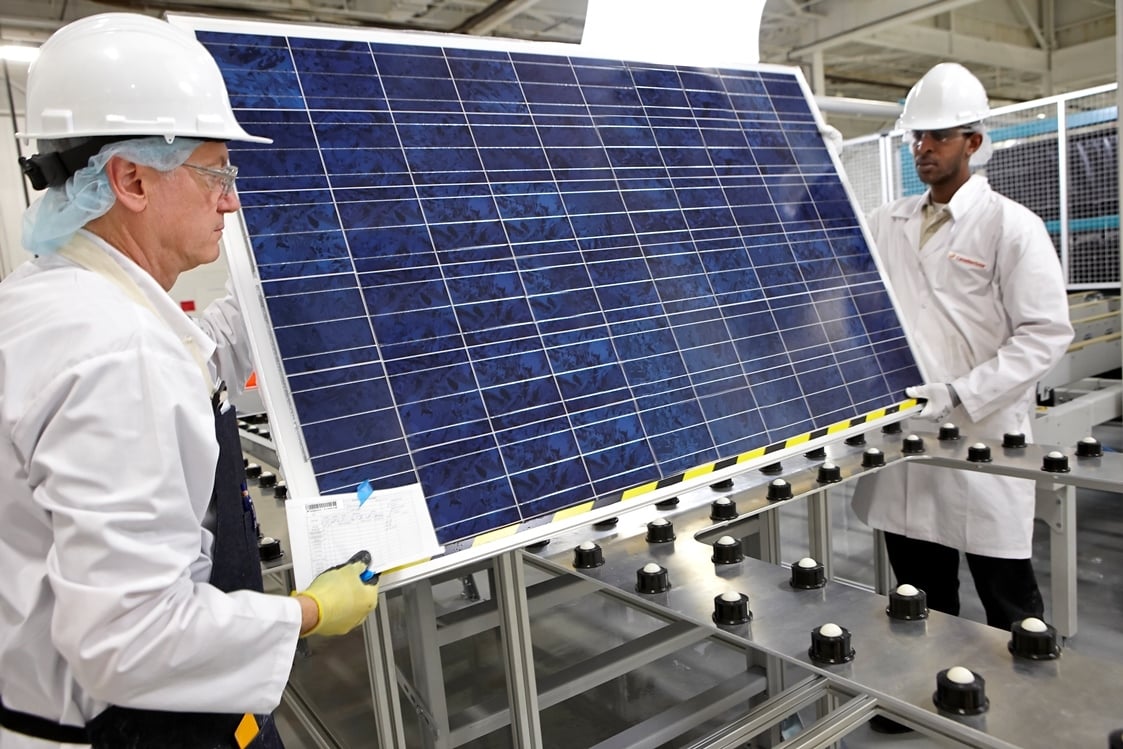
PV Tech talked with PV Lighthouse’s Malcolm Abbot ahead of PV ModuleTech 2017, being held in Kuala Lumpur, Malaysia, on 7-8 November 2017. Malcolm will be a guest speaker at the event.
Australia-based PV Lighthouse is creating a centralised software platform that is attempting to integrate all of the algorithms and data necessary to simulate the PV industry — from raw materials, to solar cells, to modules, to systems, to electricity; from theory, to engineering, to manufacturing, to distribution.
Unlock unlimited access for 12 whole months of distinctive global analysis
Photovoltaics International is now included.
- Regular insight and analysis of the industry’s biggest developments
- In-depth interviews with the industry’s leading figures
- Unlimited digital access to the PV Tech Power journal catalogue
- Unlimited digital access to the Photovoltaics International journal catalogue
- Access to more than 1,000 technical papers
- Discounts on Solar Media’s portfolio of events, in-person and virtual
What do you consider to be the most important issues today for module manufacturers?
At PV Lighthouse we are in the business of helping engineering teams develop and optimise their modules. So from our perspective what we see as the two big issues at the moment are (1) reliability of the products (particularly as people try to bring down costs) and, (2) making the right technology decisions (to help keep pushing the CTM and output power in the right direction). In both cases simulation software has a role to play since it can greatly speed up the research cycles and leads to cheaper more effective experiments in the lab. Module experiments are costly to run, so simulations can be used to screen a wider range of options as well as to gain greater insight into the results that are obtained. For reliability this is still an emerging area for modelling, but here we are able to predict things like degradation and recovery (e.g. due to LID) over the lifetime of the module allowing engineers to properly assess the cost benefit of applying mitigation strategies.
What do you consider to be the key changes module manufacturers are looking to implement in their manufacturing lines?
We have collaborated with companies that are looking at all the different parts of the module, some of them believe in incremental changes while others are looking to totally change the design. Some of the more dramatic changes that are out there would be bifacial designs, shingles, and rounded multi-wires. There are also people interested in improving the more conventional components like glass AR coatings, more reflective backsheets, glass texturing and structured tabbing. The other interesting technology out there at the moment is the mitigation of LID in both mono and multi modules. It seems there is a clear technique to achieve this on Cz wafers but on multicrystalline silicon it is still very much an issue still being developed.
Are there specific performance metrics that module manufacturers are driving towards that require additional testing, inspection or equipment?
Well again reliability is a big metric for module manufacturers and there are a number of well-established testing protocols out there. Following on from my previous answer I would say that the industry is still establishing exactly what is the right testing for LID in multicrystalline modules. There are some good tests (e.g. 96 hours in the dark while driving current in) that will pick up the problem in an untreated module, but what about those that have been partially stabilised? There is some evidence out there that those modules may still degrade somewhat over a longer time scale. At PV Lighthouse we have some projects running to include the latest kinetic models for these degradation processes so that we can try to predict what will occur in a particular design.
The other interesting change in metric that we have observed from the companies over the last few years is a transition away from wanting to simulate the product efficiency under standard test conditions (1-Sun 25°C) towards calculations of total energy yield. So now when we simulate the impact of a change in module design we are calculating the performance under a range of incident angles and illumination intensities. This can even be extended to predict how the product will perform in particular locations where the yearlong trend in intensity, spectrum and angle could be different to other locations.
Are there any key trends emerging for the next generation of mass produced solar modules 12-18 months out?
There are a number of incremental improvements out there (more busbars, half cells, better materials) that will find their way into the end products. Then there are some more interesting changes that I think it is not clear yet if they will gain traction or not. Shingles to me seems a great example of that, there are some clear advantages of that approach but there are also some potential pitfalls. When a company like SunPower acquires a technology it makes everyone look at it very closely. Many companies are also interested in bifacial modules, again this technology can look good on paper, but it needs to prove itself when installed in the field. The final trend to mention is the new texturing techniques (often called black silicon) for the multicrystalline cells. While this is technically a cell technology, it’s interaction with the module encapsulation makes it very interesting (and tricky). Certainly the industry is making great progress in this area and I would expect to see much more of it in a year from now.
What topics do you intend to cover in your talk at ModuleTech?
I’m going to be presenting some of the details of the approach we have developed to predict the performance of modules, to determine CTM and to assess new technology decisions. For the people who are a little cautious about trusting simulations I will be showing the work we did with Trina to accurately reproduce the experimental characterisation of their high performance products. I hope to also show some interesting case studies of some of the more relevant technologies (e.g. black silicon, advanced materials and improved interconnects) and how they perform under realistic conditions.
Which type of companies from the value chain are you excited about meeting over the two days of ModuleTech?
I’m excited to meet companies who are developing any sort of improved technology for modules. We find it works very well when we partner with companies who are experts in developing a specific part of the module since we can provide them with an accurate determination of how that will interact with state-of-the-art solar cells. Obviously I’m also very keen to meet with the module companies, we’ve had some great interactions there and would love to get involved with more engineering teams.
What are the key messages you are hoping to take away from ModuleTech in November?
We have always tried to focus our internal development efforts on what is most needed by industry. The trends can change quickly and new technologies can emerge rapidly so it will be very interesting to see what people are genuinely interested in moving forward with. We found PVCellTech to be a fantastic forum for both becoming informed on the latest trends in cell technology, but also for creating new connections to the industry. PVModuleTech looks like it will deliver a similar result in the broader field of modules so we are excited to be a part of it.
Malcolm completed a PhD at the University of New South Wales in 2006. He then worked for one year in the UNSW School of Photovoltaics researching crystalline silicon solar cells and applications of photoluminescence characterisation. In 2007 he moved to Silicon Valley, California, to join the start-up company Innovalight where he helped develop new products for solar cell manufacturing. After Innovalight were acquired by DuPont he continued to work on next-generation solar cell products until early 2012 when he returned to Australia to work as a consultant to the PV industry. Malcolm joined PV Lighthouse in June 2012.