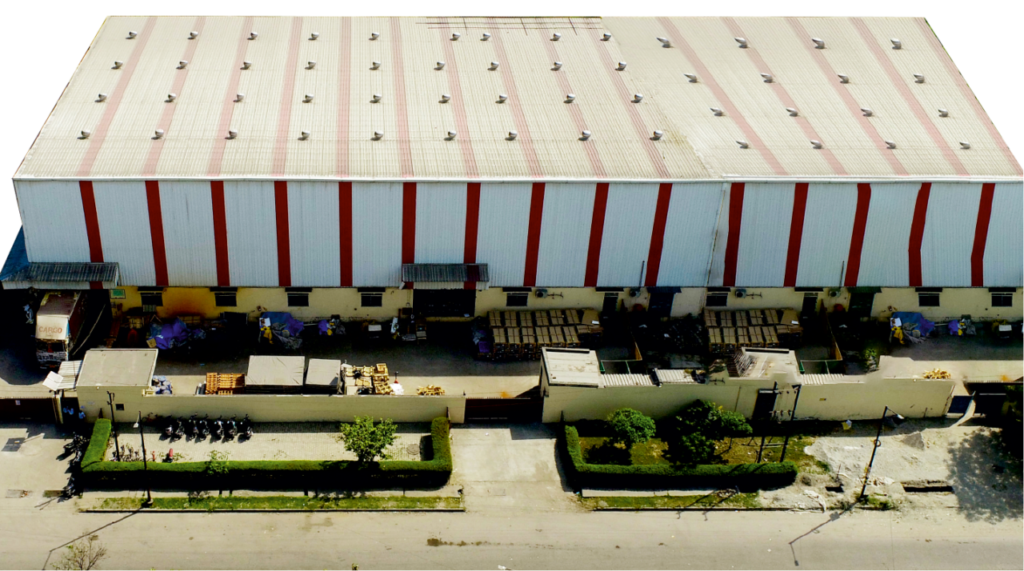
Indian PV module manufacturer Gautam Solar has announced plans to double its module manufacturing capacity to 2GW by the end of this year. The manufacturing expansion will involve a brand-new facility in the North Indian state of Haryana, around 200km from Delhi, and represents a change of direction for the company, which has built its four existing manufacturing facilities based in Haridwar, in the predominantly mountainous state of Uttarakhand.
The company’s CEO, Gautam Mohanka, spoke to PV Tech Premium about the plans, and downplayed the importance of which state a factory is built in, focusing instead on proximity to central cities like Delhi offering access to manpower, skilled engineers and the ability to capitalise on India’s new quality road infrastructure.
Unlock unlimited access for 12 whole months of distinctive global analysis
Photovoltaics International is now included.
- Regular insight and analysis of the industry’s biggest developments
- In-depth interviews with the industry’s leading figures
- Unlimited digital access to the PV Tech Power journal catalogue
- Unlimited digital access to the Photovoltaics International journal catalogue
- Access to more than 1,000 technical papers
- Discounts on Solar Media’s portfolio of events, in-person and virtual
Mohanka also discussed how current demand and policy in both the US and India offer an opportune moment to expand, and why, he believes, the export of PV manufacturing could follow in the footsteps of India’s boom in IT Industry services across the world.
Steady shift towards Indian modules
Asked why Gautam Solar is planning the extension, Mohanka said there are two main drivers. Firstly, the Indian government is supporting the domestic Indian market through its ambitious net zero targets, which aim to install 500GW of renewable energy capacity by 2030.
It is also supporting the top domestic module manufacturers through the Approved List of Module Manufacturers (ALMM), a policy which constitutes an attempt to reduce India’s dependency on imports. At its height, the policy required Indian solar installations to use modules supplied by companies with ALMM accreditations, all of which were Indian companies.
However, India failed to meet its 2022 renewable energy target amid shortages of solar modules, leading to the ALMM being lifted in February, though Mohanka believes it is likely to come back again by March 2024.
Even without ALMM, there are plenty of government projects in India which are mandated to take Indian made modules under the Domestic Content Requirement (DCR) policies.
India’s DCR has two tranches, one which requires both cells and modules to be made in India, while the other requires more than 50% of the module’s components to be produced locally, so either the cell itself, or at least half of its constituent parts, must be made in India.
Mohanka adds that there is “not a very stable relationship” between India and China, the world’s leading solar manufacturer, making it challenging for India to rely heavily on Chinese imports. Beyond this, a perceived unpredictability on China’s part has encouraged project developers in other countries to look to India as a new source of solar modules.
“They have all started at least considering or taking Indian modules even when it is not mandatory,” says Mohanka.
Gautam Solar is currently using imported solar cells in its module making, but Mohanka said the company will be discussing whether to also set up a cell manufacturing plant depending on the market environment when planning for its next financial year.
Exports to the US booming
The second driver of Gautam Solar’s factory expansion is the US imposing restrictions on Chinese-made modules, leading to demand for Indian-made modules within the US and driving a large export market for Indian manufacturers.
Once US market demand grows, Gautam Solar will then consider setting up a manufacturing facility in the US, aiming to capitalise on the Inflation Reduction Act incentives offered by the US government for setting up manufacturing within America.
“Our first priority is to get to a market scale to reach 1GW of supplies to the US,” says Mohanka.
The US market makes traceability extremely important under its forced labour restrictions, so Gautam Solar has diversified its upstream feedstock such as polysilicon away from China to a more expensive supplier, specifically to cater for these restrictions. However, for the Indian market, all of Gautam Solar’s polysilicon is still coming from China at present.
“The next IT industry of India”
Through flourishing shipments to the US in particular, India is establishing an “extremely good quality brand name in the export market”, says Mohanka. He even suggests that the PV manufacturing industry could be “the next IT industry of India”, with IT having been amongst the strongest exports from India for many years.
There are supportive government initiatives such as the ALMM and the Production Linked Incentive scheme, in which the Solar Energy Corporation of India (SECI) invites bids for PV module and cell manufacturing within India. There are also duties on cells and modules imported from China.
However, India also has several free trade agreements with Southeast Asian countries, including Malaysia, from where Chinese companies are still sending their solar modules to India duty free, says Mohanka. This circumventing has been highlighted to the government and Mohanka expects some form of preventative action to be taken.
Contrasting the US market demand for Indian modules versus the Chinese product circumventing its way into India, Mohanka says it was “one step forward and one step backwards”.
“Gautam Solar is very focused on filing patents for the process that we use to manufacture the solar modules,” he adds. “Because right now the entire world and possibly India is also dependent upon China in the process to manufacture. So, we are focused on developing indigenous technologies that can help us to manufacture by using our own in-house developed machines and automations to give us a good grip on the products.”
From Mono PERC to n-type TOPCon
Gautam Solar’s capacity expansion will include both mono passivated emitter and rear contact (PERC) and n-type tunnel oxide passivated contact (TOPCon) technology, which Mohanka claims are the “most acceptable” technologies in India right now. Furthermore, there is a high availability of n-type TOPCon cells.
The two types of technologies were also chosen because it is easier for a cell manufacturer making mono PERC cells to expand to n-type. Such a manufacturer can also produce a higher wattage using n-type TOPCon, but maintain the same the module size, whilst also keeping the same glass and other parts of bill of materials.
Mohanka says this relatively simple technology transition becomes highly attractive for utility-scale engineering, procurement and construction contractors because more power can be produced without taking up extra space through repowering existing installations. This demand is drive by both land and rooftops being amongst the biggest constraints for PV development in India at present.
“Through the entire chain, looking at cells, module makers and developers, from the raw material to the end customer, this is an incremental change but the technology is giving you much higher returns,” says Mohanka.
The switch to new n-type TOPCon products does require changes to parts of the machinery, such as the stringers, as well as the product branding. However, some other new PV technologies require changing the entire factory setup, says Mohanka, suggesting that the transition to n-type TOPCon modules will be more straightforward than other technological changes.
The domestic industry is “extremely upbeat”, says Mohanka, but the market is also consolidating in India and may see a narrowing down to a few top manufacturers that are financially stable, because PV module manufacturing is a heavy capital expenditure business and machinery needs to be changed regularly.
Mono PERC machinery, for example, has a lifespan of between one and two years. Stability is also needed for companies to keep investing into their systems without getting throttled by the oscillating fortunes of the market. Nonetheless, the recent REI Expo in Delhi demonstrated that the domestic industry has grown enormously and Mohanka describes it as a “celebration of sorts”.
“I would say that these are good days for Indian solar module manufacturers,” he says.