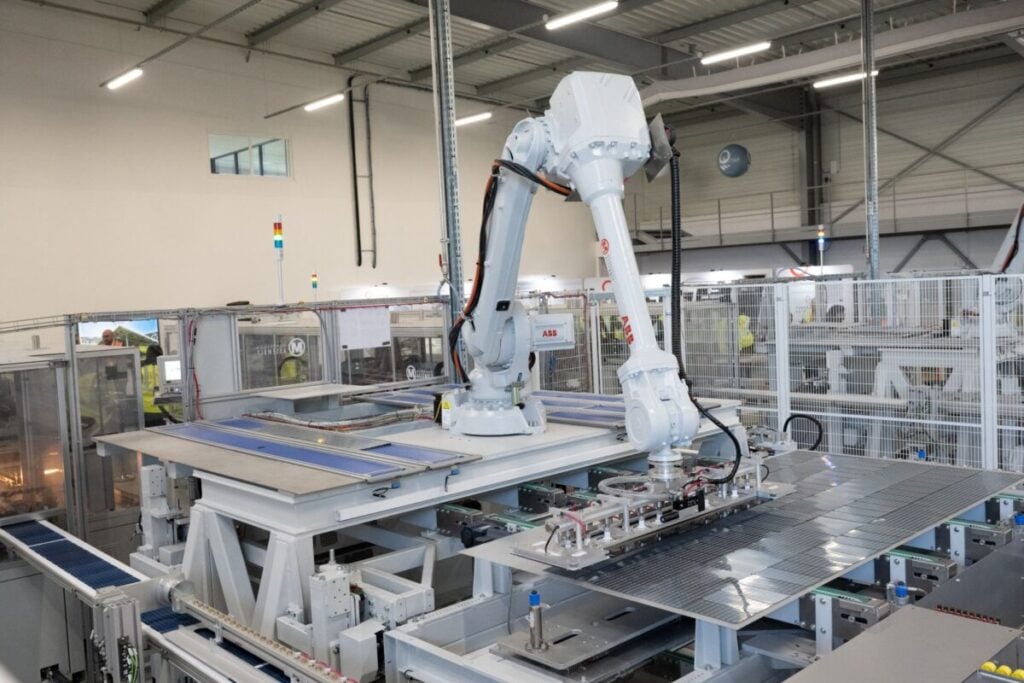
French independent power producer Reden has recently launched a module assembly line with an annual nameplate capacity of 200MW. This new line increases the company’s previous annual nameplate capacity, which sat at 60MW.
Located in the south-western French commune of Roquefort, the module line will produce Passivated Emitter and Rear Contact (PERC) modules, a choice that might seem strange at a time when tunnel oxide passivated contact (TOPCon) is the dominant technology in the industry.
Unlock unlimited access for 12 whole months of distinctive global analysis
Photovoltaics International is now included.
- Regular insight and analysis of the industry’s biggest developments
- In-depth interviews with the industry’s leading figures
- Unlimited digital access to the PV Tech Power journal catalogue
- Unlimited digital access to the Photovoltaics International journal catalogue
- Access to more than 1,000 technical papers
- Discounts on Solar Media’s portfolio of events, in-person and virtual
Tony Proutier, director of operations at Reden, told PV Tech that this was because, when the production line was ordered from Spanish equipment manufacturer Mondragon Assembly in April 2023, TOPCon technology was as advanced as PERC.
Another reason for choosing PERC over TOPCon is Reden’s own personal knowledge and usage of glass backsheet, which Proutier says is still at a testing stage for TOPCon. “We didn’t want to be part of this testing phase and we’re not looking to have the highest square meter power. We seek a good quality product,” added Proutier.
Proutier also highlighted the reliability issues that have arisen with TOPCon, which were demonstrated in a recent study from the Fraunhofer Institute for Energy Systems (ISE) in Germany. The institute conducted an analysis of 20 TOPCon modules and uncovered critical degradation effects caused by moisture ingress and UV irradiation in accelerated aging.
However, Proutier did not close the door to the production of TOPCon modules in the future, especially when the TOPCon glass backsheet technology became reliable.
Modules produced at the Roquefort plant will primarily be used on agrivoltaics (agriPV) applications on Reden’s own projects, since agriPV represents 90% of the company’s portfolio, explained Proutier.
Even though the company now has its own module production line, it still secures some of its capacity from Asia. Proutier says the fact that Reden has its own module production line makes it more knowledgeable technology-wise when purchasing modules from other manufacturers. This also extends to the partnership with the company’s solar cell provider for its own solar panels, with whom it works closely.
“We pay close attention to welding and the junction box. The junction box might seem insignificant, but with the effects of the diode inside it, it can have a large impact on the life shelf of a solar panel,” explained Proutier.
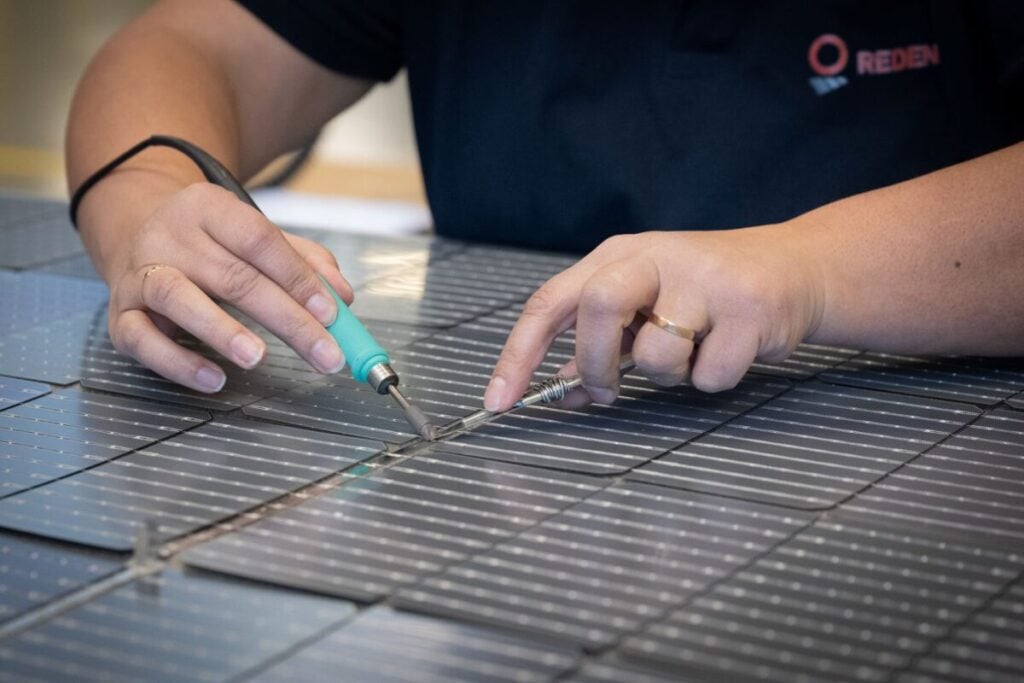
Being an IPP first and foremost
Despite looking to increase its annual module nameplate capacity, Proutier was clear that Reden does not intend to place itself as a module manufacturer solely but is, first and foremost, an independent power producer (IPP).
“We don’t want to be relegated as a module manufacturer. We want to be an IPP with a module production line because it has a meaning in our strategy,” said Proutier, adding: “Today, if I was a module manufacturer in France, in a mid-long term, there might be some business case. But in the short term, it would be complicated.”
Reden aims to integrate the whole value chain of being an IPP, which includes building its own projects, carrying out the operation and maintenance of these when they are operational and operating its own module production line.
“This allows us to be pretty flexible on the entire [IPP] value chain,” said Proutier, adding that this flexibility allows the company to be better prepared in case the development price of a solar project suddenly changes.
“We can adapt depending on the market. However, had we not internalised everything, we would not be able to adapt. We would be forced to follow the market.”
Greater flexibility
In that vein of being able to more easily adapt to the different circumstances of the market and the solar industry, owning a production line for modules gives Reden a security in case of any disruption, especially to the supply chain, such as container costs, delays in shipments among others.
This supply chain issue was seen earlier this year, when ships avoided the Red Sea due to increased violence. Even though most of these ships were transporting oil and gas, this raised an important issue of increasing prices and, more importantly, delays in delivering the products.
Localising the production of the supply chain, even at a smaller scale, gives more certainty and security that a company’s own projects will not be affected by it and will not incur in delays or halting the entire project for a certain duration.
“We decided to be proactive, and obviously, this is a cost, but we aim to make it profitable on other aspects,” explained Proutier.
Moreover, having made-in-France modules could give the company an advantage further down the line when securing power purchase agreements with companies that might look more closely into participating in projects that use domestic production. Proutier also mentioned how European legislation, such as the Net-Zero Industry Act or the Solar Charter, aims to drive the growth of domestic manufacturing in Europe and the use of domestic modules in tenders.
When asked if the company aims to increase the capacity in the future, Proutier replied that: “We would like to do it. The market will tell us if we will need it.” This will not necessarily translate to reach a plant at the gigawatt-scale, explained Proutier, outlining the company is not a manufacturer.