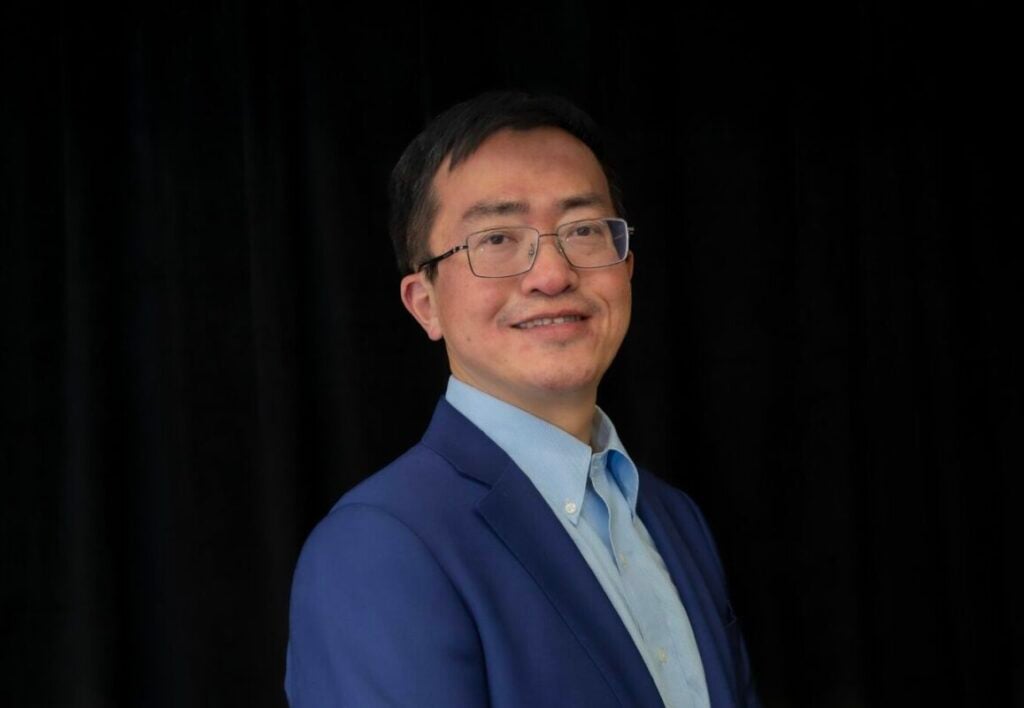
The United States’ second solar cell manufacturing plant opened earlier this month, but the domestic industry’s reliance on tax credits is on shaky ground with the new Trump administration.
Alex Zhu, CEO of US-based solar cell manufacturer ES Foundry, explains why the Investment Tax Credit (ITC) is a critical lifeline for the PV sector and how the country’s complex litigation landscape influenced the company’s decision to adopt PERC technology for its new facility.
Unlock unlimited access for 12 whole months of distinctive global analysis
Photovoltaics International is now included.
- Regular insight and analysis of the industry’s biggest developments
- In-depth interviews with the industry’s leading figures
- Unlimited digital access to the PV Tech Power journal catalogue
- Unlimited digital access to the Photovoltaics International journal catalogue
- Access to more than 1,000 technical papers
- Discounts on Solar Media’s portfolio of events, in-person and virtual
Bucking the TOPCon trend
Despite the dominance of TOPCon modules in today’s solar industry, testing agencies have flagged several reliability concerns, particularly the use of aluminium in the front metallisation paste, which makes the technology more susceptible to corrosion.
Asked whether ES Foundry’s decision to manufacture PERC cells was influenced by these reliability issues, Zhu explains that the choice was made two years ago. At the time, he predicted that the global industry would transition from PERC to TOPCon but believed the US would not follow suit due to intellectual property (IP) concerns. According to him, litigation cases in the sector can take at least two years to resolve.
“Right now, we see all the IP fighting where everyone sues everyone,” he explains. “It’s very difficult for any TOPCon technology factory, especially for solar cells, when you spend so much money while bearing the potential of being sued by other companies, leading to even longer waiting times to start the factory.
“I personally don’t believe anyone can successfully launch TOPCon cell production in the US.”
Indeed, a report published last week by Clean Energy associates bears these comments out, identifying the threat of patent litigation as one of a number of factors putting the brakes on TOPCon investments in the US.
The key role of tax credits
Tax credits have become a fundamental support for the US industry, taking the form of ITC credits for solar developers and 45X credits for domestic manufacturers.
“The ITC is more important on the policy side,” says Zhu. “Any changes related to the ITC will seriously affect the whole industry.”
All utility solar project financial models are based on 30-50% ITC credits, he adds, making the sector heavily dependent on them as a crucial driver of growth. Thus, if the ITC structure were changed, it would severely impact the financial returns of projects, leading to the potential for independent power producers having to renegotiate their power purchase agreement (PPA) or even cancel the project.
“If those things collapse, the whole industry will disappear – not only manufacturers,” Zhu warns.
On the manufacturing side under 45X, tax credits for finished solar components, such as panels, are calculated based on their electrical output. For example, solar modules are eligible for a credit of US$0.07 per watt. Zhu describes this module credit as “generous”, which explains why many US-based manufacturers are now focusing on module production.
In contrast, the approximately US$0.04 per watt available for solar cells is insufficient to bridge the cost gap between producing cells and modules – especially given the higher upfront investment required for cell production.
Asked how ES Foundry has been able to devise a credible business model based on only producing cells given this cost disparity, Zhu says ES Foundry can “charge a premium price on cells”, which is higher than the 45X credit and can cover the cost differences.
There are rumours of potential policy changes linking the ITC to domestic content requirements, which could be highly beneficial to ES Foundry. One rumour is that only projects qualifying for domestic content will receive the 30% ITC.
“Were this to come to fruition, it would immediately reduce the amount of ITC credits that can be used in 2026/2027 period due to [insufficient] supply of domestic content components,” says Zhu. “However, it will give significant incentive for industry players to invest in more capacity of domestically produced components and the supply will meet the demand in two-year cycles.”
As a result, short-term domestic content qualified product would increase in price, but would gradually drop to normal levels in two years, Zhu predicts.
Such a policy would be a boon to ES Foundry as it would drive demand for both US-made cells and modules. However, Zhu is also concerned that the ITC could end as soon as this year or next, creating significant uncertainty for the industry.
Although most analysts believe the bipartisan Inflation Reduction Act (IRA), which facilitates clean energy tax credits, will remain in place, there is still speculation about potential repeals under the current administration. President Trump has already taken steps to disrupt the renewables sector, adding to concerns about the industry’s future stability.
Leveraging Southeast Asia’s wafer surplus
For ingots and wafers, ES Foundry is sourcing products from Southeast Asia, where manufacturing capacity is expanding rapidly. However, many factories in the region, particularly in Thailand, Vietnam, Cambodia, and Malaysia have been hit by the US AD/CVD anti-dumping cases. As a result, several vertically integrated Chinese-branded manufacturers in these countries are dealing with excess wafer capacity and are eager to sell to external customers like ES Foundry.
The company’s new factory is located in South Carolina on a brownfield site, with products shipped directly to module assemblers within the US. ES Foundry is already working on its Phase 2 expansion, which is scheduled for completion in August this year, bringing the facility to 3GW capacity.
Looking forward, the biggest challenge facing the industry remains policy uncertainty, says Zhu. The Solar Energy Industries Association (SEIA) is urging the sector to lobby Washington for more favourable conditions. Earlier this month for example, in what SEIA described as a “lobbying blitz”, more than 1,850 clean energy companies sent letters to Congress expressing the economic importance of clean energy tax credits and urging lawmakers to preserve these incentives.
Zhu hopes that by the end of the year, the industry will have a clearer policy direction, allowing ES Foundry to engage with customers on their 2026 technology needs. At that point, the company will decide whether to expand its PERC production or pivot toward heterojunction (HJT) technology.
“I do think HJT will be the next technology in the US, not TOPCon,” Zhu concludes.