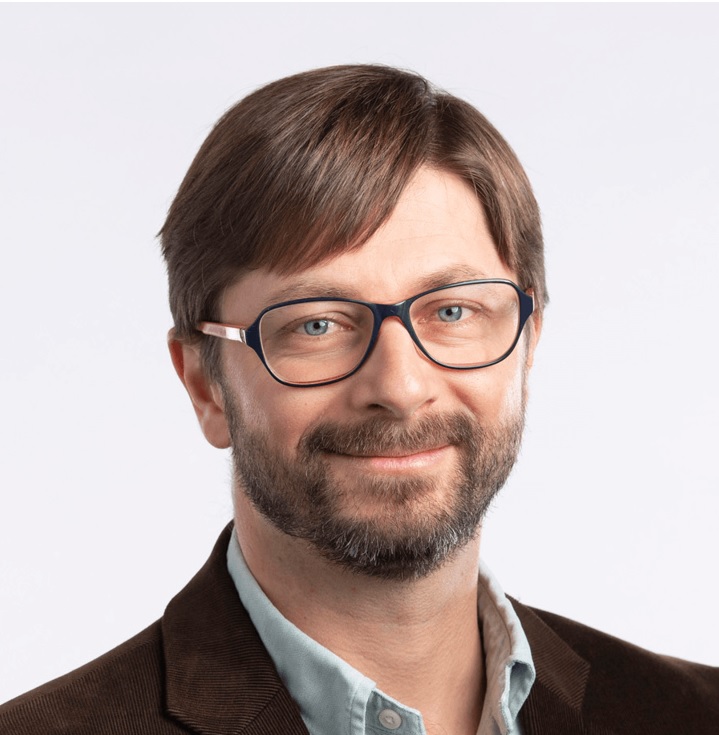
Ahead of the forthcoming PV CellTech 2020 Online event, on 27-29 October 2020, PV-Tech’s head of research and Chair of PV CellTech, Finlay Colville took the time to catch up with Jenya Meydbray, CEO at PV Evolution Labs (PVEL), about why PV cell and module technology remains a critical issue for site performance and reliability globally.
Finlay Colville is asking the questions to Jenya Meydbray.
Unlock unlimited access for 12 whole months of distinctive global analysis
Photovoltaics International is now included.
- Regular insight and analysis of the industry’s biggest developments
- In-depth interviews with the industry’s leading figures
- Unlimited digital access to the PV Tech Power journal catalogue
- Unlimited digital access to the Photovoltaics International journal catalogue
- Access to more than 1,000 technical papers
- Discounts on Solar Media’s portfolio of events, in-person and virtual
The PV CellTech events are focused on current PV technologies in mass production, but also what new PV technologies are expected to become mainstream in 2021 and beyond. What new PV technologies are you seeing at PVEL during 2020?
Jenya Meydbray, CEO at PV Evolution Labs (PVEL): “After nearly a decade of producing look-alike 60 and 72 cell modules with Al-BSF cells, manufacturers are now bringing a steady stream of new and different designs to market. It has been exciting to see such a diverse array of PV cell and module technologies at PV Evolution Labs (PVEL). Here’s a round-up of the different product types and technologies that PVEL has either tested this year or is currently testing for our PV Module Product Qualification Program (PQP):
• Cell types: Bifacial, PERC, PERT, TOPCon, HJT, CdTe
• Cell aspect ratio: Full cell, half-cut cell, shingled
• Busbars per cell: 4, 5, 6, 9, 12
• Cell to cell Interconnect types: busbars, multi-busbar with round wires, ECA, and tiling with round wires
• Wafer sizes: Eight wafer sizes with edge lengths ranging from 156.75mm all the way to 210mm for M12 wafers
• Substrate/backsheet types: PET, PVG, PVDF and other backsheet formulations, as well as transparent backsheets and glass-glass designs
The products that PVEL tests for our PQP are commercially available and in mass production; they are not R&D prototypes or hand-made samples. We confirm this by conducting an independent factory witness and audit during the production of PV modules. From a manufacturing perspective, the majority of the technologies in the PQP have the potential to become mainstream – but they must first be accepted as bankable by the investors, institutions and asset owners that provide solar project financing.”
When we look across these new PV technologies, how are the different options performing relative to one another?
Jenya Meydbray, CEO at PV Evolution Labs (PVEL): “Thus far, we have observed a range of results from the different new technologies that have undergone PVEL’s full Product Qualification Program. Cell design and technology are not the only factors in performance and reliability – the bill of materials (BOM) and production process matter a great deal.
To illustrate, consider the trend of using half-cut cells instead of full cells. Using half-cut cells reduces current in the cell, thereby reducing resistive losses and improving power output. Theoretically, half-cut cells are also less susceptible to microcracks than full cells due to their smaller surface area. Full cells have a larger cell surface area so cracks can propagate further and impact more cell area. However, cutting cells improperly on the production line can actually create defects that become microcracks. In the field, those microcracks can propagate and reduce energy yield.
Overall, we see novel technology performing very well sometimes and mature technology performing quite poorly sometimes. Technology maturity alone is insufficient to judge risk: many manufacturers do a great job with new product introduction and these are the manufacturers that will succeed pushing the technology envelope. However, all manufacturers are under intense cost pressure along with increasing pressure to innovate.”
From PVEL’s perspective, why do module buyers care about PV technology, and in particular, when these technology offerings appear to be changing at a rapid rate?
Jenya Meydbray: “Planning, engineering and constructing a large-scale project is a multi-year process that requires developers to forecast the future prices, form factors and power classes of PV modules, among many other predictions. Profitability hinges on prediction accuracy, but the extremely rapid rates of technology change we are observing today have made accurate forecasting more difficult.
PV modules used to be interchangeable to a large degree because they had fairly standardized dimensions and electrical specifications. With changing wafer sizes, there is now a great deal of PV module size variation. There are balance-of-system ramifications, too – from compatibility with tracking and mounting systems to the number of required strings, combiner boxes and other components. If a product is not available as predicted at the time of procurement, re-engineering the project may be necessary. The project re-engineering process is slow and expensive, and development is a time-sensitive exercise. Changes to modules could require changes to tracker designs, electrical layout, and other areas. Every developer tries to avoid costly re-engineering if possible.”
Much is made today of cell efficiency gains and module power rating increases coming from larger format panels. What matters most however when looking at module returns to site owners?
Jenya Meydbray: “Net Present Value (NPV) is how most developers judge the economic success of a project. This simply includes the build cost, ongoing operating costs, energy production, and useful life. Each of these factors needs to be understood as much as possible. PV module cost and power output in insufficient. Module dimensions impact build cost beyond the module. And power translates to energy differently for different module designs.
PVEL’s test data helps downstream buyers understand how to translate power to energy. Degradation rates, pan files, IAM coefficients, useful life and other failure mechanisms are the top concerns of large module buyers. Cell efficiency gains and higher power ratings usually increase the total value of the project and reduce costs – but changing PV module dimensions have system-level ramifications. If higher power classes require the trade-off of higher-cost balance of system components, the project economics may not pencil out. Similarly, if increased power causes a reduction in yield, then the economics may change.”
What aspects of PV technology and manufacturing are you most interested in learning more about during PV CellTech 2020 Online?
Jenya Meydbray: “Over the past 12 months we have seen no shortage of announcements of higher power, higher efficiency, as well as the addition of huge production volumes. PVEL advises many large developers in the U.S., so we’re always trying to look into our crystal ball to determine what is real versus what is marketing in terms of manufacturing advancements. PV CellTech is a great forum to hear what manufacturers are working on and where their efforts are focused. We expect the industry to continue to change rapidly, and we look forward to helping bring the new technologies to market by supporting the bankability of this new class of modules.”