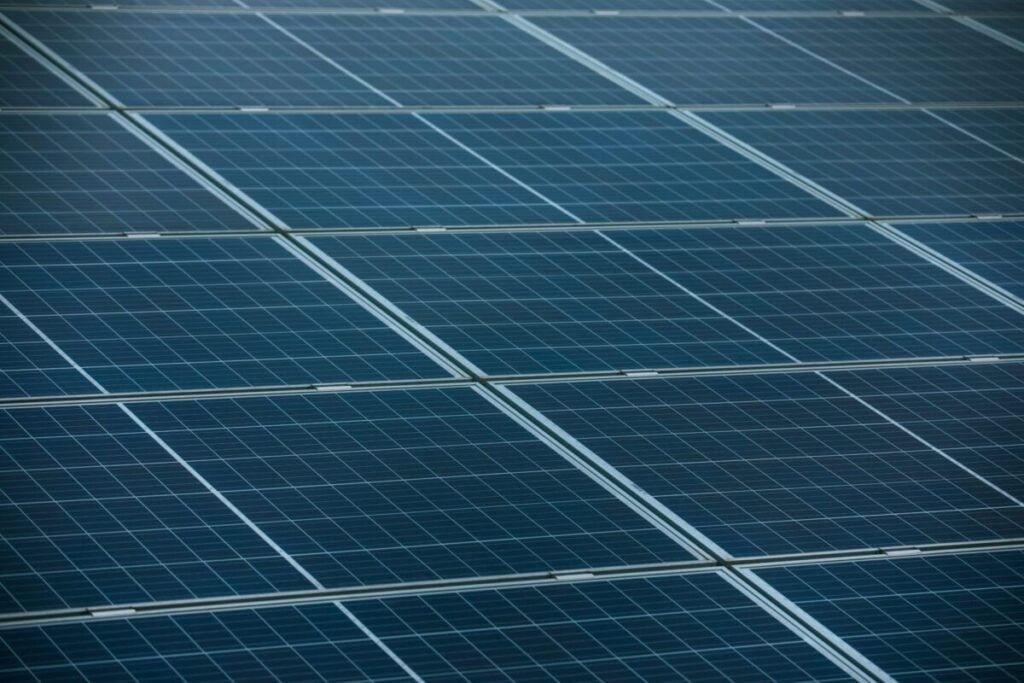
Researchers from the University of New South Wales (UNSW) and the University of Newcastle have found that “hidden contaminants” in TOPCon and HJT modules can lead to a power loss of up to 16%.
The presence of these “hidden contaminants” in damp heat (DH)-induced degradation in heterojunction (HJT) and tunnel oxide passivated contact (TOPCon) glass-backsheet modules resulted in relative power losses of 10-16% after 1,000 hours of DH testing.
Unlock unlimited access for 12 whole months of distinctive global analysis
Photovoltaics International is now included.
- Regular insight and analysis of the industry’s biggest developments
- In-depth interviews with the industry’s leading figures
- Unlimited digital access to the PV Tech Power journal catalogue
- Unlimited digital access to the Photovoltaics International journal catalogue
- Access to more than 1,000 technical papers
- Discounts on Solar Media’s portfolio of events, in-person and virtual
Elemental analysis identified sodium (Na), calcium (Ca), magnesium (Mg), chlorine (Cl), and sulfur (S) as the likely contributors. These elements – element names Na+, Ca2+, Mg2+, Cl−, and S2− – are likely to chemically react with moisture as well as with the passivation layers and/or metal contacts of solar cells under damp heat testing conditions.
These contaminants accumulate on cell surfaces or staging areas before encapsulation and, under DH conditions, interact with passivation layers, causing cell metallisation. According to the research, in the case of HJT, this also happens with the transparent conductive oxide (TCO), and amorphous/microcrystalline silicon layers. The presence of these contaminants results in an efficiency loss.
According to the researchers, the hypothesis for these contaminants to appear is due to ‘improper’ handling during cell or module processing, such as contact with contaminated gloves, cassettes, packaging, or vacuum grippers.
On the other hand, Passivated Emitter and Rear Contact (PERC) modules have shown minimal degradation under the same conditions and showed greater resilience, according to the study.
“These findings underscore the need for strict contamination control of both manual and automated handling tools, especially for advanced cell architectures like HJT and TOPCon, which are significantly more sensitive to contamination than conventional PERC cells,” wrote the researchers.
Some of the solutions, highlighted by the researchers, to reduce the exposure of hidden contaminants are a thorough deionised water cleaning, strict adherence to handling protocols using uncontaminated gloves, cassettes, packaging material, or vacuum grippers, and the exclusive use of clean stages prior to encapsulation are strongly recommended.
The paper was published in the Solar Energy Materials and Solar Cells publication.
This is the latest research that highlights possible issues with TOPCon technology, including issues related to ultraviolet-induced degradation or critical degradation effects caused by moisture ingress and UV irradiation in accelerated ageing. However, research from Fraunhofer Institute for Solar Energy Systems (ISE) published last month found that concerns over the performance of TOPCon cells following UV exposure might be exaggerated.
Earlier this year, another study by researchers at the UNSW reported positive results from using copper plating to protect TOPCon PV cells against contaminant-induced degradation.
Up to 85% silver use reduction for TOPCon cells
Other research from the UNSW recently achieved an up to 85% reduction in rear-side silver usage in 25% efficiency TOPCon solar cells.
The reduction was achieved through a two-step printing process, where a small amount of silver paste is printed as dashes to form contacts with the silicon surface, followed by the printing of floating fingers and busbars with alternative silver-lean pastes.
By implementing the design elaborated by the UNSW researchers, the silver consumption on TOPCon cells is reduced to 2mg/W, with only a marginal efficiency gap (∼0.1 %) compared to TOPCon cells with an industrial standard metallisation design.
With silver continuing to be a key component in the manufacturing of solar cells, with 40-60% higher silver usage in TOPCon compared to traditional PERC technology, according to the researchers, reducing its use has been an ongoing key trend for the industry in recent years.
Among the efforts to reduce the use of silver is an ongoing industry trend to go busbar-less. This trend first started with HJT but can also be applied to TOPCon and even future products, as Markus Fischer, vice president of R&D operations at solar manufacturer Qcells and co-chairman of the International Technology Roadmap for Photovoltaic (ITRPV), mentioned earlier this year to PV Tech (Premium access).
Another recent research, this time from Germany’s Fraunhofer ISE, developed a new HJT solar cells which uses “one-tenth” of the amount of silver cell (1.4mg/W) as a standard cell.